Пока "Газпром" строит газопроводы, Siemens сворачивает выпуск турбин. Газовые турбины газпром
Siemens поставит «Газпрому» турбины для строительства ТЭС в Грозном :: Бизнес :: РБК
«Газпром» объявил, что Siemens поставит для Грозненской ТЭС две газовые турбины. С прошлого года немецкий концерн находится в процессе судебного разбирательства со структурами «Ростеха» из-за поставки турбин в Крым
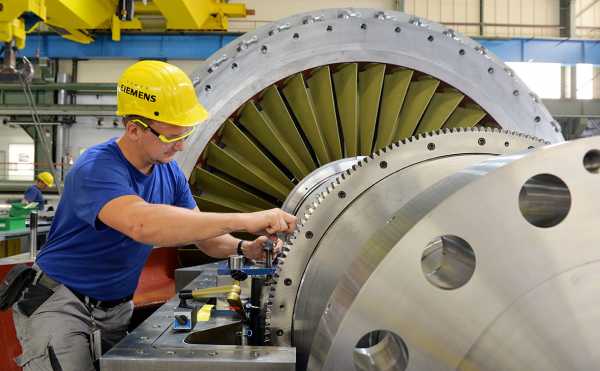
Фото: Maurizio Gambarini / DPA / ТАСС
«Газпром» приобретет две газовые турбины Siemens для Грозненской ТЭС. Об этом говорится в заявлении российской компании, поступившем в РБК. В нем уточняется, что 16 марта в Санкт-Петербурге состоялась встреча главы «Газпрома» Алексея Миллера и президента Siemens Джо Кэзера, где обсуждались перспективы сотрудничества.
«Особое внимание было уделено поставке оборудования для Грозненской ТЭС. Согласно подписанному контракту, специалистами Siemens будут отгружены, установлены и введены в эксплуатацию две газовые турбины для электростанции общей мощностью до 360 МВт. Запуск объекта планируется в 2019 году», — сообщает «Газпром».
О том, что российская корпорация закупит турбины Siemens для Грозненской ТЭС, стало известно в апреле 2015 года. Тогда сообщалось, что немецкая компания стала победителем конкурса на поставку оборудования для ТЭС, строительством которой занимается «Газпром энергохолдинг». Изначально речь шла о поставке паровых турбин.
Siemens заключил первую крупную сделку в России после крымского скандалаВ апреле 2017 года наблюдательный совет «Совета рынка» утвердил замену оборудования на Грозненской ТЭС с парогазовой установки (ПГУ) на газотурбинную (ГТУ), писали «Ведомости» со ссылкой на источники, близкие к участникам заседания.
Летом 2017 года разгорелся скандал с поставками газовых турбин для строящихся электростанций в Крыму. Сообщалось, что они могли попасть на полуостров вопреки санкциям. Siemens и его «дочка», ООО «Сименс технологии газовых турбин» (СТГТ), подали в 2017 году два иска против структур «Ростеха» — ОАО «Технопромэкспорт» и ООО «Технопромэкспорт». Siemens сначала просил об аресте турбин, а затем признать незаконными два договора об их поставках. Ни один иск удовлетворен не был. 1 марта Девятый арбитражный апелляционный суд Москвы отклонил жалобу немецкого концерна на решение столичного арбитража по спору о поставках турбин в Крым.
www.rbc.ru
Пока ″Газпром″ строит газопроводы, Siemens сворачивает выпуск турбин | Экономика в Германии и мире: новости и аналитика | DW
Слова "Сименс" и "турбины" у информированных россиян наверняка ассоциируются сегодня со скандалом вокруг поставки продукции немецкого концерна в Крым в нарушение санкций ЕС. В Германии широкая публика, слыша эти два слова, думает в настоящее время совсем о другом: об угрозе закрытия градообразующего сименсовского завода в восточногерманском Гёрлице и надвигающихся массовых увольнениях на других предприятиях концерна, выпускающих газовые турбины.
Немецкие ожидания противоречат российским прогнозам
Данная тема, активно освещаемая немецкими СМИ, на самом деле представляет немалый интерес и для россиян. Для них ключевое слово здесь "газ". Ведь российская государственная компания "Газпром" строит сейчас газопроводы "Северный поток-2" и "Турецкий поток", объясняя многомиллиардные вложения в них растущей в Европе потребностью в природном газе для производства электроэнергии и тепла.
В Грайфсвальде рядом с действующим первым "Северным потоком" должен появиться второй
В то же самое время руководство Siemens радикально сворачивает производство газовых турбин, объясняя это главным образом отсутствием перспектив строительства новых газовых электростанций в Европе. Таким образом, ожидания немецкого концерна явно противоречат прогнозам и инвестиционным решениям российской компании. DW знакомит читателей с позицией ведущего технологического концерна ФРГ.
Председатель правления Siemens Джо Кезер (Joe Kaeser) вкратце изложил ее 31 января 2018 года в Мюнхене на годовом собрании акционеров. По его словам, в ближайшие два-пять лет в одной только Германии придется сократить примерно 3 тысячи рабочих мест на производстве оборудования для электростанций, работающих на ископаемых энергоносителях, т.е. на нефти, угле и газе.
Джо Кезер не видит в Европе рынка для газовых турбин
Это, подчеркнул Кезер, не чисто "сименсовская проблема", а результат структурных изменений в мировой электроэнергетике. Падение глобального спроса на оборудование для работающих на ископаемом сырье электростанций составило свыше 40 процентов, цены снизились более чем на 30 процентов. "Особенно в Германии: здесь практически больше нет спроса", - заявил глава Siemens.
Джо Кезер
Таким образом, на крупнейшем для "Газпрома" экспортном рынке, немецком, строить новые крупные газовые электростанции никто особо не собирается. "Мы убеждены, что мировой рынок газовых турбин будет и дальше существовать, - заверил акционеров Джо Кезер. - Но рынки уменьшатся, и находится они будут не в Европе, а в Америке, Китае, на Ближнем и Среднем Востоке".
Иными словами, в мюнхенской штаб-квартире Siemens исходят из того, что более активно использовать газ для получения электроэнергии будут в США и КНР, где растет добыча сланцевого газа, и в богатом голубым топливом ближневосточном регионе, но не в Европе, так что ждать отсюда заказов на турбины для новых газовых электростанций не стоит.
Мировая энергетика: коренной перелом из-за возобновляемых источников
За более подробными разъяснениями позиции немецкого концерна DW обратилась к его пресс-секретарю Альфонсу Бенцингеру (Alfons Benzinger). Он отвечает за подразделение Power and Gas, которое как раз занимается выпуском газовых турбин. Siemens - один из мировых лидеров по их производству.
Принадлежащий совместному предприятию Siemens Gamesa ветропарк в Ирландии
"В мировой энергетике происходит сейчас коренной перелом. Рынок оборудования для производства электроэнергии из ископаемых источников сокращается с большой скоростью", - отметил собеседник DW и проиллюстрировал это следующими цифрами. В 2014 году Siemens и все другие производители продали на планете в общей сложности порядка 200 больших газовых турбин мощностью свыше 100 мегаватт, в 2016 году - около 180, а в 2017 - всего 110 единиц.
Главной причиной такой тенденции в Siemens считают глобальные успехи возобновляемой энергетики, на которую и сам немецкий концерн все больше делает ставку. Джо Кезер напомнил участникам годового собрания акционеров, что после слияния испанской Gamesa с сименсовским подразделением ветровой энергетики возникло крупнейшее в мире (по размерам установленной мощности) предприятие в области возобновляемой энергии: по всему миру оно управляет оснащенными им ветропарками суммарной мощностью 83 гигаватта (для сравнения: это сопоставимо с 70-80 энергоблоками атомных электростанций) .
"Золотой век газа" пока не предвидится
"Затраты на производство электроэнергии из возобновляемых источников в 2011-2016 годах резко снизились. В ветровой энергетике, к примеру, издержки ежегодно сокращались примерно на 8 процентов, в фотовольтаике - почти на 20 процентов в год. Поэтому сегодня они уже существенно ниже, чем на парогазовых установках", - указал Альфонс Бенцингер.
В результате возобновлемая энергетика быстро увеличивает свою долю в Европе и особенно в Германии, где она форсированно развивается благодаря широкой государственной поддержке. И именно возобновляемые источники все чаще приходят сейчас на смену угольной генерации, которую Евросоюз стремится сократить в рамках борьбы против изменения климата. При этом какие-то европейские страны развивают атомную энергетику, другие от нее, наоборот, отказываются, но значительного роста доли газовых электростанций в производстве электроэнергии нигде не наблюдается.
По данным Федерального объединения предприятий энерго- и водоснабжения (BDEW), в Германии доля природного газа в 2017 году незначительно выросла с 12,5 процента до 13,1 процента, тогда как доля возобновляемых источников увеличилась за год с 29 сразу до 33,1 процента. Уже в 2018 году они, по всей видимости, станут главным источником электричества в Германии, обогнав каменный и бурый уголь, доля которых упала в течение года с 40,3 до 37 процентов.
Всего несколько лет назад, в 2011 году, Международное энергетическое агентство (МЭА) заговорило о грядщем "золотом веке газа". Тогда было много надежд на то, что именно природный газ как наиболее экологичное ископаемое топливо станет идеальным "партнером" возобновляемых источников электроэнергии, способным оперативно заменять их в ситуации, когда нет солнца или не дует ветер.
Обнародованное в ноябре 2017 года намерение концерна Siemens сократить по всему миру 6 тысяч рабочих мест на производстве турбин, а также декабрьское решение его американского конкурента General Electric упразднить на своих заводах такого же профиля 12 тысяч мест, свидетельствуют о том, что ни о каком "веке газа" в мировой электроэнергетике, тем более европейской, пока и речи быть не может.
В какой мере ситуация изменится к тому времени, когда "Газпром" введет в строй "Северный поток-2" и "Турецкий поток", покажет будущее.
Смотрите также:
-
Взлеты и падения концерна Siemens
Все началось с телеграфа
В 1846 году Вернер фон Сименс (Werner von Siemens) изобрел стрелочный телеграф, ставший предшественником факсимильного аппарата. Чтобы наладить серийное производство, вместе с механиком Иоганном Гальске (Johann Halske) он создал фирму Telegraphen-Bauanstalt von Siemens & Halske. В берлинской мастерской десять умельцев выпустили первую партию таких телеграфов.
-
Взлеты и падения концерна Siemens
Из мастерской на фабрику
В 1850-е годы на фабрике Siemens наладили стандартизированное серийное производство. Здесь сконструировали паровые двигатели и придумали первые генераторы. Открытие электродинамического принципа - одно из главных достижений Сименса: он создал условия, при которых производство электроэнергии в больших объемах стало реальностью.
-
Взлеты и падения концерна Siemens
Уникальное судно
В 1864 году фирма потерпела серьезные убытки, связанные с неудачной прокладкой телеграфного кабеля через Средиземное море. Спустя десять лет при помощи специального судна "Фарадей", оснащенного кабелеукладочной машиной, удалось связать Ирландию и США. В последующие годы таким же способом было проложено еще шесть трансатлантических линий.
-
Взлеты и падения концерна Siemens
Транспорт будущего
В 1879 году фирма Siemens & Halske представила первую в мире электрическую железную дорогу, работающую от внешнего источника питания. Уже в 1881 году открылось трамвайное сообщение с длиной пути в два с половиной километра. Электрический трамвай мог развивать скорость до 30 км/ч и следовал от берлинской станции Лихтерфельде.
-
Взлеты и падения концерна Siemens
Социальный предприниматель
Помимо технических изобретений Вернер фон Сименс был известен и как меценат. Деньги он жертвовал на развитие науки, в частности, на основание Берлинской национальной физико-технической лаборатории. Кроме того он заботился о сотрудниках своей компании: создал пенсионный фонд и библиотеку, сократил рабочий день. В 1890 году Сименс ушел в отставку, а спустя два года скончался от воспаления легких.
-
Взлеты и падения концерна Siemens
Город-фирма
Компания увеличивалась с каждым годом. В 1897 году фирма Siemens & Halske приобрела незаселенную территорию на северо-западе Берлина. Постепенно здесь концентрировалось произоводство и строилось жилье для работников. В 1914 году эта площадь стала районом города и получила название Сименсштадт (Siemenssstadt).
-
Взлеты и падения концерна Siemens
Труд подневольных рабочих
Во время Второй мировой войны Siemens & Halske использовала труд подневольных рабочих, в частности, узников женского концлагеря Равенсбрюк, на территории которого компания возвела завод. Женщины занимались сборкой телефонов и другого оборудования связи. Лишь в конце 1990-х фирма создала специальный фонд для выплаты компенсаций.
-
Взлеты и падения концерна Siemens
Больше заводов и фабрик
Турбины, средства автоматизации, железные дороги, электростанции, частные коммуникационные системы, медицинская техника, стиральные машины, - чего только не выпускала компания Siemens. К началу 1980-х годов фирма открыла свои производства в 37 странах. В 1990-х годах две трети выручки составили именно зарубежные доходы.
-
Взлеты и падения концерна Siemens
Громкий скандал
В 2006 году компания оказалась в центре громкого коррупционного скандала. Около 1,3 миллиарда евро оказались в черной кассе, из которой деньги ради выгодных сделок направлялись сомнительным посредникам. Пострадала не только репутация компании - многие топ-менеджеры и члены правления потеряли свою работу. Позже концерн провел радикальную реструктуризацию.
-
Взлеты и падения концерна Siemens
Большой куш
Самый большой заказ в истории концерна - на более 6 миллиардов евро - Siemens получил от немецкой железнодорожной компании Deutsche Bahn на создание новых поездов ICE. Еще одна крупная сделка была заключена в Египте: там строится самая мощная газовая электростанция в мире.
-
Взлеты и падения концерна Siemens
Siemens сегодня
Сейчас концерн представлен в 140 странах и насчитывает около 348 тысяч сотрудников по всему миру. Современная индустрия формата 4.0 бросает компании новый вызов: привычная производственная цепочка должна полностью измениться.
-
Взлеты и падения концерна Siemens
Новая проблема
В июле 2017 года концерн оказался замешанным в скандале из-за поставки двух турбин Siemens в порт Севастополя. Он обвинил российских партнеров в несоблюдении условий договора. Газотурбинные установки предназначались для проектов в Тамани, а не для аннексированного полуострова. Представители Siemens подали в суд на заказчиков.
Автор: Хильке Фишер, Ксения Сафронова
Сердце газотранспортной системы
11 апреля 2016
Как транспортируют природный газ
«Газпром» располагает крупнейшей в мире газотранспортной системой. Она представляет собой уникальный технологический комплекс, включающий в себя объекты транспортировки (о некоторых из них мы уже рассказывали в наших фоторепортажах: «72 часа», «„Сахалин — Хабаровск — Владивосток“ — испытано стихией», «Готовим „сани“ к зиме», «„Грязовец — Выборг“: газопровод повышенной проходимости», ) и хранения («Хранители газа»), а также обеспечивает непрерывный цикл поставки газа от скважины до конечного потребителя. Общая протяженность газотранспортной системы на территории России составляет 170,7 тыс. км. В транспортировке газа используются 250 компрессорных станций, на которых установлено 3825 газоперекачивающих агрегатов (ГПА).
Сегодня мы расскажем вам о том, как создаются ГПА — важнейшие элементы газотранспортной системы, благодаря которым становится возможным транспортирование природного газа по магистральным газопроводам.
В настоящий момент российская газовая отрасль полностью обеспечивает себя отечественными ГПА. Их делают в России несколько заводов — в Казани, Перми, Рыбинске, Санкт-Петербурге и Уфе. В северной столице газоперекачивающие агрегаты производит «РЭП Холдинг», входящий в структуру промышленных активов «Газпромбанка». «РЭП Холдинг» образуют крупнейшие промышленные предприятия «Невский завод» и «Завод ЭЛЕКТРОПУЛЬТ», а также собственный научно-проектный «Институт энергетического машиностроения и электротехники».
«РЭП Холдинг» выпускает широкую номенклатуру энергетического и турбокомпрессорного оборудования, в том числе газоперекачивающие агрегаты «Ладога» на базе стационарных газовых турбин мощностью 16, 22/25 и 32 МВт. Все процессы производства и испытаний газовых турбин локализованы на «Невском заводе», который мы посетили в первую очередь.
Завод был основан в 1857 году. Уже более 75 лет здесь разрабатывают и производят продукцию энергетического машиностроения — газовые и паровые турбины, центробежные и осевые компрессоры, нагнетатели. В 2007 году завод вошел в состав «РЭП Холдинга». При инвестиционной поддержке «Газпромбанка» была проведена глобальная реконструкция — построены новые производственные цеха, внедрены современные технологии, приобретены уникальные станки.
На «Невском заводе» работают высококвалифицированные специалисты. К слову сегодня в Санкт-Петербурге активно развивается промышленность, а технические специальности востребованы и престижны. «Училищем» наши остроумные собеседники на заводе просторечно называют не ПТУ, а МГТУ имени Баумана — ведущий технический вуз страны, а турбины именуют по цифрам мощности «тридцать вторая», «двадцать пятая».
Сейчас основной продукт «Невского завода» — ГПА-32 «Ладога» (выпускается по лицензии GE Oil & Gas) разработанный специально для российского рынка на основе базового семейства газовых турбин MS5002E. Это единственный газоперекачивающий агрегат мощностью 32 МВт, производимый в России. Его КПД составляет 36%, и что немаловажно — этот агрегат отличается образцовыми экологическими характеристиками — эмиссия вредных выбросов составляет не более 18 ppm (ppm означает «частей на миллион», от английского parts per million).
Мощность 32 МВт точно гармонирует с пропускной способностью магистральной трубы диаметром 1420 мм — самой большой по диаметру, используемой для магистральных газопроводов (в исключительных случаях мощность ГПА может быть и больше, например, на компрессорной станции «Портовая», перекачивающей газ по газопроводу «Северный поток», установлено несколько ГПА мощностью 52 МВт).
На примере «Ладоги» инженер — кстати, родом из Италии, но давно проживающий в России, — Филипп Пицци рассказывает нам, как устроена газовая турбина: «„Сигара“ турбины делится на две части: газогенераторная и часть низкого давления — так называемая силовая часть».
В газогенераторной части (справа) атмосферный воздух сжимается лопатками и затем подогревается в камере сгорания за счет сжигания в сжатом воздухе жидкого топлива. Приобретая, таким образом, высокую температуру и давление, воздух (газ) поступает в область низкого давления (слева), попутно расширяясь и ускоряясь.
Далее, поток газа попадает на рабочие лопатки турбины, отдавая им часть своей энергии и передавая крутящий момент на вал. Вал приводит в работу компрессор для перекачки газа.
«Невский завод» не стоит на месте и постоянно развивается, внедряя новые разработки. Сейчас завод активно готовится к запуску в серийное производство новой стационарной газотурбинной установки Т16 мощностью 16 МВт (16-мегаваттные двигатели — самые распространенные в «Газпроме», ими оборудована треть всех ГПА). На фото — слесаря Сергей Гришин, Кирилл Ружицкий, диспетчер сборки Вячеслав Куш, начальник сборочного производства Олег Кириллов, бригадир Федор Обломов.
Как и в случае с «Ладогой» это также совместная разработка с GE Oil & Gas, но уже не просто освоение лицензии, а совместное проектирование. КПД — 37%.
Филипп принимает активное участие в проекте производства. «Преимущество такой машины состоит в том, что она хороша и для газоперекачки и для выработки электроэнергии — куда скажут, туда и поставим. Первый образец у нас идет в Москву для энергетиков», — сообщил Филипп. На фото — рама вспомогательных устройств для новой турбины.
Ключевое слово в этом проекте — стационарная. Конструктор турбины Т16 Артем Андропов объясняет, в чем главное отличие стационарной газовой турбины от авиационной. Авиационная турбина значительно меньше по размеру, считается удобной для прохождения техобслуживания, но имеет более ограниченный ресурс. Кроме того, самолетный двигатель необходимо приспосабливать для нужд газовой отрасли. Стационарная же турбина делается специально для промышленного потребителя и в большей степени отвечает требованиям надежности.
«Наиболее существенным преимуществом этой машины является очень большой ресурс работы. Полный жизненный цикл — 200 тысяч часов. Это более 20 лет», — объясняет Артем.
«Еще одним важным достоинством этой машины является ее высокая эффективность. Чтобы выработать энергию, нам нужно меньше подвести топлива. Машина отличается компактностью и удобством монтажа. Она представлена на одной опорной раме, и, благодаря этому, мы можем производить ее полную установку и запуск в течение 24 часов. То есть после доставки всего комплекта оборудования на объект, через 24 часа мы получим первую электроэнергию с клемм генератора», — обещает Артем Андропов.
Артему 25 лет, на заводе он работает уже почти 6 лет. Заканчивал Санкт-Петербургский государственный морской технический университет. «Я по специальности турбинист — мне эта тематика очень близка. Сразу хотел работать на постоянной основе и на четвертом курсе устроился сюда — уже инженером-конструктором, работал полных три дня в неделю. На специальность „газовые турбины“ я попал случайно. Изначально хотел пойти на более общее направление „Судовые автоматизированные установки“. Как назвать это — ошибкой, или счастливой случайностью, которая помогла мне найти свое дело? Но в течение пяти лет, чем дольше я учился, тем больше понимал, что это мое», — рассказывает создатель турбины.
Участок изготовления рамы под новую турбину. Преимущества этой рамы в том, что она имеет возможность боковой выкатки. По рельсам, которые приделаны к ней, можно будет выкатить полностью всю «сигару», либо только часть высокого давления или низкого, тем самым обслуживать или ремонтировать только тот узел, который необходим.
Мастер участка Антон Казанцев (слева) рассказал, что турбина будет защищена шумотеплоизолирующим кожухом (КШТ). «В верхней части кожуха будут находиться кран-балки. Поэтому какие-либо агрегаты, которые в процессе эксплуатации могут нуждаться в замене или в оперативном доступе, можно будет демонтировать непосредственно, не снимая крыши с КШТ, через специальные двери», — поясняет Антон.
Антон работает на заводе с 2011 года. До этого работал на другом предприятии «РЭП Холдинга» — заводе «ЭЛЕКТРОПУЛЬТЕ», о котором мы расскажем ниже. Учился в Санкт-Петербургском государственном морском техническом университете на факультете корабельной энергетики и автоматики.
«По большому счету это профильно, потому что газовые турбины относятся к энергетическим установкам. Мне здесь интересно, я всегда хотел работать на производстве. У нас на заводе сильная кадровая политика и достойные условия труда — это очень важно», — подчеркнул Антон Казанцев.
Мы поинтересовались у Антона, как удается преодолевать языковой барьер в общении с партнёрами — итальянцами. Антон Казанцев уверено отвечает: «Я в пределах университетского образования отлично владею английским языком, и с 5 лет учился в английской школе. Разговорный английский у меня на достойном уровне».
Пообщавшись с мастером участка, мы направились в цех сборки.
Здесь все составляющие части агрегата собираются в единую композицию.
Перед нами корпус турбины низкого давления, в него устанавливается выхлопной диффузор камеры сгорания турбины Т16. Через него проходят сгоревшие газы.
«С запуском серийного производства сборка этого узла будет осуществляться быстрее, но в случае с первым образцом мы более детально все перепроверяем», — делится секретами диспетчер сборочного участка Вячеслав Куж.
Вячеслав работает на «Невском заводе» уже 4 года. Начинал на сборке ГПА-32 «Ладога». Имеет высшее образование — окончил Санкт-Петербургский институт машиностроения.
Параллельно со сборкой новой установки на заводе идет отлаженный процесс выпуска компрессоров, нагнетателей, паровых турбин и другой продукции.
Главный конструктор управления центробежных компрессоров «РЭП Холдинга» Владимир Климентьевич Юн привел нас к станку, где обрабатывается корпус компрессора, который будет работать в составе газоперекачивающего агрегата ГПА- 25 на нефтегазоконденсатном месторождении.
Корпус компрессора — это кованая бесшовная труба с толщиной стенки около 100 мм. На фото корпус после предварительной обдирки (снятия окалины). Но корпус — это только одна из составных частей компрессора, для получения конечного продукта, рабочими завода будет проделана немалая работа: приварены лапы, установлены патрубки, сделана расточка внутренних полостей.
Этой работой занимаются настоящие профессионалы! На фото — электрогазосварщик Сергей Тюнин.
Бригадир Михаил Воронцов и слесарь-электромонтажник Максим Телегин.
Завершающим этапом создания каждой турбины является ее проверка на испытательном стенде. Он проектируется и строится индивидуально под каждую машину определенной мощности, так как каждая турбина в своем конструктиве уникальна.
Начальник стендового управления Владимир Болдырев поясняет: «Есть помещение, где подготавливается воздух, есть помещение, где готовится газ, сверху пультовая, электрическое хозяйство. Это целый комплекс сооружений — это не просто площадка».
Владимир Юрьевич работает на заводе уже 33 года. Из них 13 лет возглавляет участок испытаний.
Пройдя испытания, турбина будет готова к эксплуатации, но останется «последний штрих» — подключение к системе автоматического управления. На фото — машинист крана Наталья Городецкая и бригадир Сергей Богомолов.
И для того чтобы увидеть, как создают эти системы управления, мы направились на завод «ЭЛЕКТРОПУЛЬТ».
АО «Завод ЭЛЕКТРОПУЛЬТ» ведет отсчет своей истории с 1935 года. Первой продукцией завода были пульты для электростанций, именно они дали название заводу. В 2004 году предприятие вошло в состав «РЭП Холдинга».
Сегодня основная продукция завода — это автоматизированные системы управления, преобразовательная техника, средневольтное оборудование, комплектные распределительные устройства, комплектные трансформаторные подстанции, электроприводные газоперекачивающие агрегаты, контейнерные конструкции для электротехнического оборудования.
Например, шкафы — низковольтные комплектные устройства — изображенные на фото, изготовлены для объектов газопровода «Бованенково — Ухта».
Собираются эти шкафы из профиля и по универсальному техническому решению германских фирм Siemens и Rittal, которые являются владельцами базовых на мировом рынке технологий производства шкафов Sivacon (конструктив фирмы Siemens) и Rittal. На фотографии запечатлены каркасы будущих шкафов.
Профиль Rittal делают из нержавеющей стали. Уголок такого профиля имеет 16 граней — очень сложная конструкция.
Но завод «ЭЛЕКТРОПУЛЬТ» разработал и свой вариант конструктива электрошкафов под названием «Сфера». Устройство предназначено для приема и распределения электроэнергии трехфазного переменного тока, а также для управления оборудованием и его защиты от коротких замыканий и перегрузок. Создан он в 2015 году командой завода. Таким образом, заводчане внесли свой собственный вклад в большое дело импортозамещения.
А руководил созданием нового образца начальник отдела комплектных трансформаторных подстанций Андрей Гогулин.
«Этот шкаф призван стать нашей полноценной альтернативой зарубежным конструктивным решениям. И если в шкафы по иностранным технологиям монтируется исключительно оборудование определенных изготовителей, кстати, тоже иностранных, то в конструктив „Сфера“ можно смонтировать оборудование абсолютно любого поставщика», — рассказывает создатель новинки.
Андрей показывает нам уже готовый шкаф «Сфера Н». Буква «Н» обозначает низкий класс напряжения. В дальнейшем завод планирует сделать такой конструктив по всем трем классам напряжения (низкое, среднее, высокое).
Происхождение названия «Сфера» незамысловатое, оно идет от самого коллектива завода. «Сфера деятельности „ЭЛЕКТРОПУЛЬТА“ — это производство электрооборудования и электрошкафов в частности», — пояснил Андрей Гогулин.
А коллективом своим завод гордится. Здесь, как и на «Невском заводе», работают настоящие профессионалы своего дела — такие как Сергей Чикин и Виктор Круглов.
Александр Виданов.
Юрий Кондратов и Алексей Галанкин.
Владимир Новосельцев.
Но железо — это только железо. За то, чтобы электрошкаф приобрел свою «душу» и неповторимую функциональную индивидуальность отвечает начальник участка изготовления жгутов монтажного производства Ольга Иванова.
Ольга Владимировна рассказала нам, что каждый электрический шкаф уникален: «Мы получаем документацию — сборочные чертежи. И на макете рисуем место нахождения приборов и по трассировке делаем жгут. Потом готовое изделие готовим к монтажу, штырюем, паяем разъемы, одеваем маркировочные трубочки и готовое изделие устанавливаем в шкаф».
Цех, где изготавливают жгуты, похож на оазис.
Теперь электрошкаф полностью готов. Его установят в блок-контейнере, который на месторождении служит домом для людей и техники.
А строят эти дома следующим образом. На переднем плане снимка основание строения. Оно выполнено единой сварной конструкцией, что обеспечивает необходимую жесткость и прочность.
А это стены и потолок. Легкий и прочный несущий каркас выполнен из стали, обшивается по стенам и потолку утеплителем в виде сэндвич-панелей, которые позволяют эксплуатировать блок-контейнер при температуре окружающей среды от —60 до +40°С.
Блок-контейнеры удобно перевозить автомобильным и железнодорожным транспортом, перемещать подъемно-транспортными средствами.
Внутри устанавливается энергетическое оборудование для газоперекачивающего агрегата. Напоминает кухонный гарнитур, нашпигованный встроенной техникой.
Блок-контейнеры оборудованы системами освещения, вентиляции, обогрева, пожарно-охранной сигнализацией.
«Квартирный вопрос полностью решается», — шутят заводчане. Конструкция блок-контейнера позволяет изготавливать его с отдельными помещениями, тамбурами, рабочими зонами, зонами отдыха.
Этот блок-контейнер — знакомого фирменного газпромовского цвета Pantone-300. Значит заказ «Газпрома».
Он отправится работать на компрессорную станцию «Усинская» газопровода «Бованенково — Ухта». Пожелаем ему хорошей дороги и долгой службы.
А нам пора отправляться домой, сегодня был насыщенный и емкий день. Мы побывали на двух заводах Санкт-Петербурга, тесно связанных с газовой отраслью. Увидели своими глазами, как работает отечественная промышленность, выпуская высококачественную и конкурентоспособную продукцию — газоперекачивающие агрегаты — сердце газотранспортной системы.
Редакция сайта ПАО «Газпром»
Фотографии большого размера вы можете найти в фотоальбоме.
www.gazprom.ru
Турбины как судьба
Обеспечивать безаварийность тысяч объектов добычи, транспорта, переработки и хранения газа — стратегический приоритет холдинга ООО «Газпром центрремонт», и задача эта становится еще более актуальной в свете курса на импортозамещение, объявленного на государственном уровне и реализуемого сегодня в холдинге. Dыполнять задачи подобного масштаба могут только высококвалифицированные профессионалы своего дела, среди которых — начальник инженерно-технического управления по ТОиР Сергей Ланговой.
НАЧАЛО НАЧАЛ
Я родился в городе Ленинграде. Там же прожил практически всю сознательную жизнь за исключением последних примерно 10-ти лет.
Образование у меня самое что ни на есть «турбинистское». Правда, изначально я стремился в авиацию, но подвело зрение, поэтому я поступил в Ленинградский политехнический институт, на кафедре турбиностроения как раз была специализация «Авиационные двигатели».
В 1973 году я впервые познакомился с будущим Газпромом, работая в студенческом стройотряде недалеко от поселка Вуктыл на строительстве газосборного пункта. После окончания института меня распределили на завод имени В.Я. Климова, где занимались разработкой и созданием практически всех отечественных газотурбинных двигателей для вертолётов, а также для танка Т-80 и для истребителя МиГ-29. Работая на испытательной станции инженером-испытателем, я получил неоценимый практический опыт, но всё же решил продолжить своё образование в области турбиностроения и поступил в аспирантуру Ленинградского кораблестроительного института на кафедру судовых турбин и турбинных установок, после окончания которой защитил кандидатскую диссертацию.
Как раз в то время промышленность и прикладная наука СССР готовили ответ на эмбарго «Рейгана», касавшееся поставки газотурбинного оборудования для отечественных магистральных газопроводов. Меня пригласили научным сотрудником в ЛПИ на кафедру турбиностроения в специально созданную научную группу, где мы с коллегами совместно со специалистами Невского завода создавали новую отечественную газотурбинную установку для газопроводов — ГТН-25/76.
В процессе этой работы я впервые столкнулся с газотурбинным двигателем, используемым в газоперекачивающем агрегате.
КОГДА ПРАКТИКА ПРЕДПОЧТИТЕЛЬНЕЕ ТЕОРИИ
Наряду с научной деятельностью я начал преподавать и через некоторое время получил звание доцента. Вообще, преподавательская и научная деятельность в ЛПИ продлилась почти 15 лет, и на моем счету порядка полусотни научных статей и изобретений, часть из которых была успешно внедрена. При этом мне довелось работать не только с отечественными предприятиями, но даже участвовать в научно-экспериментальной работе, выполненной по заказу фирмы Siemens. Правда, в конечном счете, я принял решение уйти с научной стези. У меня уже была в разработке докторская диссертация, но я почувствовал, что теряю интерес к теоретической науке. Тогда, в переломные девяностые, я начал вплотную заниматься большими энергетическими газотурбинными установками, которые эксплуатируются на электростанциях, и был приглашен на работу в инженерный центр «Энергомашкорпорации», которая объединяла на тот период крупнейшие российские энергомашиностроительные предприятия — «Ленинградский металлический завод», «Электросилу» и «Завод турбинных лопаток». Наш инженерный центр и перечисленные предприятия через некоторое время оказались в объединении «Силовые машины», но я продолжал заниматься внедрением на электростанциях парогазовых установок на базе большой ГТУ ГТЭ-160 (V94.2), которая выпускалась на совместном предприятии «Силовых машин» и фирмы Siemens.
В последнее время работы в инженерном центре я был техническим руководителем проекта ПГУ-230, строительство которой предполагалось в Венгрии. К сожалению, по финансовым причинам этот проект так и не был реализован до конца, хотя всё основное оборудование для ПГУ было изготовлено и поставлено Заказчику. Угасающий интерес к данному проекту заставил меня искать новую интересную работу, связанную с газовыми турбинами, и тут я узнал о проекте создания в «Газпроме» единого ремонтного холдинга. Впоследствии меня пригласили на работу в компанию «Центрэнергогаз».
СТАРТ БОЛЬШИХ ДЕЛ
Деятельность в «Центрэнергогазе» я начинал в качестве советника генерального директора. Тогда в рамках работы по реструктуризации производственной деятельности «Газпром» поставил перед нашим предприятием задачу организации ремонтного холдинга на базе разрозненных ремонтных подразделений своих дочерних Обществ. За сравнительно короткий период совместными усилиями немногочисленному на тот период коллективу «Центрэнергогаза» удалось проделать большую работу по выводу ремонтных подразделений из состава дочерних Обществ «Газпрома» и переводу их в «Центрэнергогаз». С этой целью было создано несколько рабочих групп, курирующих те или иные предприятия. Я попал в группу, работающую с ООО «Самаратрансгаз» (ныне — ООО «Газпром трансгаз Самара»).
После успешного решения задачи организации единого ремонтного предприятия руководство нашей компании приняло решение о необходимости наличия своего собственного машиностроительного подразделения, отвечающего за производство запасных частей и, прежде всего, лопаток газовых турбин. Отсутствие оперативной поставки комплектующих увеличивало сроки ремонта ГПА. Кроме того, качество поставляемых запасных частей зачастую сказывалось на качестве ремонтов агрегатов. В связи с этим были приняты решения о создании ремонтного холдинга ООО «Газпром центрремонт» и о вхождении в его состав заводов ОАО «Газэнергосервис». Параллельно шло развитие инженерных подразделений самого холдинга.
Как показало время, эти решения оказались очень своевременными. Когда на рубеже 2008–2009 годов возникли проблемы с комплектацией старых ГПА производства Невского завода, наличие собственных заводов и развитой инженерной службы позволило оперативно решить задачу не только производства необходимых комплектующих, но и в короткие сроки организовать на заводах «Газэнергосервиса» заводской ремонт турбоблоков ГТК-10-4.
Позднее, в сжатые сроки была аналогично решена задача освоения производства комплектующих, необходимых для организации ремонта ГПА производства Уральского турбинного завода. Эта проблема возникла из-за повышения заводом цен на производимые комплектующие.
В 2009 году руководство холдинга «Газпром центрремонт» приняло решение о целесообразности расширения машиностроительного комплекса холдинга. С этой целью была создана рабочая группа, в составе которой мне также довелось поработать, для выбора потенциальных машиностроительных заводов для дальнейшего расширения Холдинга. После анализа ряда предприятий и оценки их возможностей было принято решение о целесообразности вхождения в состав холдинга предприятия «Тюменские машиностроители». Это было обусловлено целым рядом причин и, прежде всего, тем, что это предприятие специализировалось на ремонте конвертированных судовых газотурбинных двигателей, парк которых в «Газпроме» составлял почти 1000 единиц. Это открывало новые возможности по загрузке заводов в составе холдинга в части производства различных комплектующих и лопаток турбин.
НЕТ ХУДА БЕЗ ДОБРА
В последнее время приоритетным направлением в работе инженерно-технического управления по ТОиР ООО «Газпром центрремонт», которое я возглавляю, является вопрос импортозамещения. Одновременно перед нами поставлена задача максимальной загрузки производственных предприятий холдинга.
Выполняя поручения «Газпрома», мы проводим совместную работу с Брянским инженерным центром ООО «Газпром центрремонт» и с дочерними машиностроительными предприятиями для выработки решений технических задач и вопросов по организации производства комплектующих на заводах Холдинга. С этой целью разрабатываются программы по освоению производства на наших заводах новой номенклатуры изделий, проводятся научно-исследовательские и опытно-конструкторские работы, связанные, в числе прочего, с импортозамещением и продлением ресурса судовых двигателей.
Так, например, в 2013 году была поставлена задача расширения номенклатуры судовых газотурбинных двигателей, ремонтируемых и комплектуемых предприятиями холдинга. Кстати сказать, эта задача оказалась своевременной, ведь ее решение позволило подготовиться к проблемам, возникшим позднее, связанным с ремонтами судовых двигателей и поставкой комплектующих предприятиями, расположенными на Украине. С цель реализации данной программы производственные предприятия холдинга были оснащены новым необходимым оборудованием. Большую роль в подборе нового оборудования играли специалисты нашего инженерно-технического управления. Параллельно с этим на заводе «Тюменские моторостроители» был построен и введён в эксплуатацию новый стенд для испытаний двигателей, мощностью до 30 МВт. Таким образом, сегодня на предприятиях холдинга освоен ремонт всех типов двигателей, украинского производства, а также освоено производство всех необходимых видов комплектующих.
О ВЕРНОСТИ ДЕЛУ
Если бы мне предложили сейчас сменить сферу деятельности, я бы точно отказался. Накоплен богатый опыт, к тому же, круг «турбинистов» в России достаточно узок: многих знаешь, со многими общаешься, везде встречаешь коллег, с которыми где-то когда-то пересекался. Это очень помогает в работе.
centrremont.gazprom.ru
Siemens поставил турбины для строящейся Грозненской ТЭС Газпром энергохолдинга // Оборудование, услуги, материалы // Новости
Грозный, 5 июл - ИА Neftegaz.RU. Завершилась доставка 2го комплекта газотурбинного оборудования (газовая турбина и генератор) производства Siemens на строительную площадку Грозненской ТЭС. 1й комплект прибыл в г Грозный ранее, уже осуществляются работы по его монтажу.
Об этом Газпром энергохолдинг сообщил 5 июля 2018 г.
В торжественных мероприятиях, прошедших на площадке строительства Грозненской ТЭС, приняли участие гендиректор Газпром энергохолдинг Д. Федоров, Президент Siemens в России Д. Мёллер и 1й замруководителя администрации главы и правительства Чечни Г. Таймасханов.
Энергетическое оборудование производства Siemens поставлено в рамках контракта, подписанного в начале 2018 г.
Комплекты были отправлены в Чечню из г Санкт-Петербурга на барже до порта г Махачкалы, затем перевезены автомобильным транспортом в г Грозный.
Газовые турбины будут введены в эксплуатацию специалистами Siemens.
Кроме того, для Грозненской ТЭС воронежский завод Siemens трансформаторы разработал и поставил 5 силовых трансформаторов мощностью от 16 до 250 МВА.
Строительство Грозненской ТЭС вступает в завершающую стадию.
Своевременная доставка оборудования укрепляет оптимизм относительно сроков ввода объекта в эксплуатацию.
Ранее срок был перенесен с 2018 г на 2019 г.
Надежная современная электростанция необходима Чечне.
Регион в последние годы показывает стабильный рост потребления электроэнергии.
Грозненская ТЭС будет способствовать как развитию экономики республики, так и стабильности энергосистемы Юга страны.
На Грозненской ТЭС будут установлены не только газовые турбины, но и генераторные модули и трансформаторы.
Д. Мёллер. выразил уверенность в том, что использование современного оборудования с высокой долей локализации его производства в России обеспечит надежность, безопасность и высокую эффективность новой электростанции и других электростанций в стране.
Газпром и Siemens договорились о поставках турбин в марте 2018 г.
17 мая 2018 г Siemens начал поставки турбин.
Газпром энергохолдинг реализует проект строительства Грозненской ТЭС в рамках системы договоров о предоставлении мощности (ДПМ).
Строительство Грозненской ТЭС осуществляется в Заводском районе г Грозного.
Новая ТЭС будет работать в составе Единой энергетической системы России и станет 1й действующей электростанцией чеченской энергосистемы.
Напомним, что в период боевых действий 1994-1996 гг Грозненские ТЭЦ были разрушены.
Новая электростанция будет состоять из 2х газотурбинных установок (ГТУ) общей установленной электрической мощностью порядка 360 МВт.
Основное топливо станции самый экологически чистый вид топлива - природный газ.
В соответствии с правилами ДПМ, ввод Грозненской ТЭС в эксплуатацию должен состояться в 2019 г.
Договоренность о строительстве когенерационной газопоршневой электростанцией (ГПЭС) в г Грозном была достигнута в октябре 2013 г во время встречи Р. Кадырова с главой Газпрома А. Миллером.
В апреле 2014 г Р. Кадыров заложил капсулу с посланием к потомкам в основание будущей ТЭС.
Обсудить на Форуме
neftegaz.ru
Минэнерго не согласно с предложением Газпром энергохолдинга о 100%-ой локализации газовых турбин в России // Энергетика // Новости
Санкт-Петербург, 25 апр - ИА Neftegaz.RU. Газпром энергохолдинг на фоне неудач с разработкой российских больших газовых турбин для электростанций предложил локализовать на 100% в России производство турбин Siemens.
С таким предложением 25 апреля 2018 г выступил в ходе Российского международного энергетического форума гендиректор Газпром энергохолдинга Д. Федоров.
По словам Д. Федорова, можно или провести конкурс, или предложить какой-либо компании на условии стратегического сотрудничества.
По его мнению потратить 7-8 лет на производство турбины, которую производят с 70х гг, при условии, что не понятно, будет она работать или нет - неправильно.
Технический блок ГЭХа заранее предвидел проблемы с турбиной ГТЭ 110 (производит ОДК-Сатурн).
Он подчеркнул, что при этом не против российских турбин, но они должны работать.
Д. Федоров предложил сделать 100%-ную локализацию производства турбин Siemens в России, отметив, что компания к этому готова и этот вопрос обсуждался.
По его словам, для этого надо обеспечить спрос в объеме 4-5 турбин в год на протяжении 4-5 лет.
Однако замминистра энергетики РФ А. Черезов поставил под сомнение такую возможность.
Он отметил, что нужна турбина, которая будет максимально локализована на территории РФ, но говорить о 100%-ной локализации - невозможно.
Проблема с большими газовыми турбинами в России стоит уже давно, поскольку именно такие агрегаты являются основными на теплоэлектростанциях с парогазовым циклом.
Их приходится покупать у немецкого концерна Siemens, что и послужило причиной скандала с установкой таких турбин на крымских ТЭС.
Несколько лет назад Ростех разработал газовую турбину мощностью 110 МВт, и 7 таких агрегатов установили для тестирования на 2 электростанции, принадлежащие Газпром энергохолдингу и Интер РАО.
Однако наладить их стабильную работу так и не удалось, несмотря на многочисленные доработки.
По словам Д. Федорова, за 7 лет турбины не проработали и 5-6 месяцев.
18 апреля 2018 г стало известно, что испытания 1й российской газовой турбины большой мощности ГТД-110М остановлены из-за поломки во время испытаний.
ОДК-Сатурн, дочка Ростеха, сразу же заявила, что несмотря на то, что из-за поломки сроки завершения работ будут сдвинуты, это не фатально и работа продолжится.
В Роснано также заявили, что продолжают принимать акционерное участие в проекте, он востребован и будет реализован любыми силами.
В связи с неудачными испытаниями Ростех предложил участие в проекте Силовым машинам.
Там объяснили предложение тем, что компания является мощным игроком на рынке энергетического машиностроения, у нее есть необходимые компетенции и незагруженные мощности для крупноузловой и финальной сборки машин данного класса.
Ранее председатель совета директоров Силовых машин А. Мордашов заявил, что концерн готов помочь Ростеху разработать технологию производства газовых турбин на условиях государственно-частного партнерства, чтобы заменить поставляемую германской Siemens продукцию.
Знаменитая история по газовым турбинам, поставленным в Крым, еще раз подчеркивает, что России необходима своя технология газовых турбин.
И Силовые машины готовы взять на себя обязательство сделать такую технологию, но для этого компания просит о государственно-частном партнерстве.
А. Мордашов отметил, что Силовые машины готовы взять на себя половину расходов, но без поддержки государства в финансировании НИОКРов и испытательной базы концерн просто напросто не потянет данный проект.
Он напомнил о сотнях миллионов евро, которые немецкое правительство выдает Siemens на освоение прогрессивных видов оборудования.
Обсудить на Форуме
neftegaz.ru
Минэнерго и "Газпром энергохолдинг" поспорили из-за газовых турбин
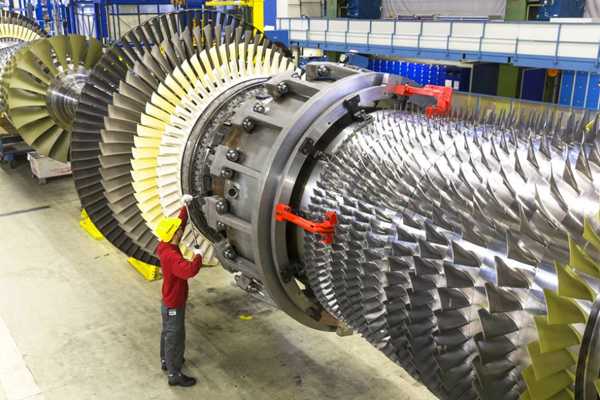
Фото: pronedra.ru
Поскольку в России пока не удается построить газовую турбину большой мощности, необходимо создать 100-процентно российское производство турбин Siemens. С таким предложением выступил в ходе Российского международного энергетического форума генеральный директор “Газпром энергохолдинга” Денис Федоров.
“Есть же турбины Siemens. Давайте сделаем 100-процентную локализацию их производства здесь. Компания к этому в принципе готова, с Siemens мы это проговаривали” – пояснил Федоров. По его словам, чтобы локализация была экономически оправдана, необходимо обеспечить спрос в объеме четыре-пять турбин в год на протяжении четырех-пяти лет.
Однако заместитель министра энергетики РФ Андрей Черезов с Федоровым не согласился: “Нужна турбина, которая будет максимально локализована на территории Российской Федерации. … Но говорить о 100-процентной локализации – это невозможно”.
Проблема с большими газовыми турбинами в России стоит уже давно, поскольку именно такие агрегаты являются основными на теплоэлектростанциях с парогазовым циклом. Их приходится покупать у немецкого концерна Siemens, что и послужило причиной скандала с установкой таких турбин на крымских ТЭС.
Несколько лет назад “Ростех” разработал газовую турбину мощностью 110 МВт, и семь таких агрегатов установили для тестирования на две электростанции, принадлежащие “Газпром энергохолдингу” и “Интер РАО”. Однако наладить их стабильную работу так и не удалось, несмотря на многочисленные доработки. По словам Федорова, за семь лет турбины не проработали и пяти-шести месяцев.
В этой связи в начале апреля председатель совета директоров и владелец “Силовых машин” Алексей Мордашов заявил, что его компания готова сделать то, что не удается «Ростеху»: “Знаменитая история по газовым турбинам еще раз, на мой взгляд, подчеркивает, что России необходима своя технология газовых турбин. И мы, “Силовые машины”, готовы взять на себя обязательства сделать такую технологию, но для этого мы попросили о государственно-частном партнерстве в освоении газовых турбин”.
Правда, «Силовым машинам» понадобится помощь правительства, отметил Мордашев: «Мы готовы, например, взять на себя половину расходов, но без поддержки государства в финансировании НИОКР, в финансировании испытательной базы нам просто не потянуть этот проект». :///
teknoblog.ru