Платформа эффективности. Овчинников газпром
Цифровой двойник – Журнал «Сибирская нефть» — ПАО «Газпром нефть»
Одна из перспективных идей завтрашнего дня, касающаяся любого производства, — цифровое моделирование активов: создание виртуальных копий реальных объектов, которые выглядят и функционируют точно так же, как и их прототипы. В «Газпром нефти» «цифровыми двойниками» вплотную занимаются на перерабатывающих производствах компании, и многое из этой инновационной технологии уже удалось воплотить в жизнь
От рисунков до 3D-моделей
Немного истории. Чертежи и схемы нужны были людям всегда, с момента первых изобретений — колеса и рычага, чтобы передавать друг другу информацию об устройстве этих приспособлений и правилах их использования. Сначала это были примитивные рисунки, содержащие лишь самые простые сведения. Однако конструкции становились сложнее, а изображения и инструкции — детальнее. С тех пор технологии визуализации, документирования и хранения знаний о сооружениях и механизмах прошли большой путь. Тем не менее долгое время основным носителем для фиксации инженерной мысли оставалась бумага, а рабочим пространством — плоскость.
Во второй половине ХХ века стало ясно, что привычная армия чертежников, вооруженных кульманами, уже не способна успеть за стремительным ростом развития промышленного производства и сложностью инженерных разработок. Ускорение обработки объемной и сложной информации (например, технологическая установка атмосферной перегонки нефти содержит более 30 тысяч единиц оборудования) потребовало изменения технологии работы проектировщиков, конструкторов, строителей, технологов, специалистов по эксплуатации и техническому обслуживанию. Эволюция технических средств проектирования совершила очередной виток, и в начале 90-х годов прошлого века в нефтяную отрасль пришли системы автоматизированного проектирования — САПР. Сначала они использовали двухмерные чертежи, а затем, к концу 2000-х, пришли и в 3D.
Современные системы проектирования позволяют инженерам выполнить компоновку и проектирование промышленных объектов в объемном виде с учетом всех ограничений и требований производственного процесса, а также требований промышленной безопасности
Современные системы проектирования позволяют инженерам выполнить компоновку и проектирование промышленных объектов в объемном виде с учетом всех ограничений и требований производственного процесса, а также требований промышленной безопасности. С их помощью можно создавать проектную модель той или иной установки и правильно размещать на ней технологические и технические компоненты без противоречий и коллизий. Опыт показывает, что за счет использования подобных систем удается в 2–3 раза сократить количество ошибок и несостыковок при проектировании и эксплуатации различных установок. Цифра впечатляет, если учесть, что для крупномасштабного промышленного оборудования число ошибок, которые приходится исправлять в процессе проверки проекта, исчисляется тысячами.
С точки зрения проектировщиков и строителей, использование 3D-моделей дает возможность кардинально улучшить качество проектной документации и сократить время проектирования. Построенная информационная модель объекта оказывается полезной и на этапе эксплуатации. Это новый уровень владения промышленным объектом, на котором персонал может получить любую информацию, требующуюся для принятия решения или выполнения задачи в кратчайший срок, опираясь на имеющуюся модель. Более того: когда через какое-то время потребуется модернизация оборудования, будущим проектировщикам будет доступна вся актуальная информация, с историей ремонтов и обслуживаний.
Омский пилот
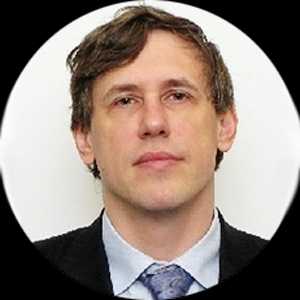
Сергей Овчинников,руководитель департамента систем управления «Газпром нефти»
Разработка и внедрение системы управления инженерными данными, без сомнения, важная часть инновационного развития блока логистики, переработки и сбыта. Функционал, заложенный в «СУпрИД», потенциал системы позволят блоку в частности и компании в целом стать лидерами в цифровом управлении инженерными данными в нефтепереработке. Более того, этот программный продукт является важной составляющей всей линейки связанных IT систем, представляющих собой фундамент создающегося сейчас Центра управления эффективностью БЛПС.
В 2014 году в «Газпром нефти» стартовал проект по созданию системы управления инженерными данными объектов нефтепереработки — «СУпрИД». В основе проекта лежит применение технологий 3D-моделирования для проектирования, строительства и обслуживания промышленных объектов. Благодаря их использованию сокращаются сроки создания и реконструкции нефтеперерабатывающих установок, повышается эффективность и безопасность их эксплуатации, снижается время простоя технологического оборудования завода. Внедрением современной системы управления инженерными данными на новейшей платформе Smart Plant for Owners/Operators (SPO) занимаются специалисты департамента систем управления блока логистики, переработки и сбыта, а также дочерней компании «ИТСК» и «Автоматика сервис».
За счет использования автоматизированных систем проектирования, создающих 3D-модели объектов, удается в 2–3 раза сократить количество ошибок и несостыковок при проектировании и эксплуатации различных установок.
В конце прошлого года успешно выполнен пилотный проект по разворачиванию функционала платформы и настройки бизнес-процессов для только что реконструированной установки первичной переработки нефти Омского НПЗ — АТ-9. В системе реализован функционал по хранению, управлению и актуализации информации об установке на всем ее жизненном цикле: от строительства до эксплуатации. Наряду с системой были разработаны нормативно-методическая документация, требования к проектировщику и стандарты по управлению инженерными данными. «СУпрИД» является хорошим помощником в работе, — отметил начальник установки АТ-9 Омского НПЗ Сергей Шмидт. — Система позволяет быстро получить доступ к инженерной информации о любом оборудовании, посмотреть его чертеж, уточнить технические параметры, локализовать местоположение и выполнить замеры на трехмерной модели, которая в точности воспроизводит реальную установку. Использование «СУпрИД» помогает, в том числе, обучать новых специалистов и стажеров».
Как это работает?
Задача системы «СУпрИД» — охватить все этапы жизненного цикла технологического объекта. Начать со сбора инженерной информации на фазе проектирования и затем актуализировать сведения на последующих стадиях — строительства, эксплуатации, реконструкции, отображая текущее состояние объекта.
Все начинается с информации от проектировщика, которая последовательно передается и загружается в систему. Исходные данные составляют: проектная документация, информация о функционально-технологической и строительно-монтажной структуре объекта, интеллектуальные технологические схемы. Именно эти сведения становятся базой информационной модели, позволяя мгновенно получать адресную информацию о строительных объектах и технологической схеме установки, давая возможность за несколько секунд найти нужную позицию технологического оборудования, оборудования КИПиА на технологической схеме, определить ее участие в технологическом процессе.
В свою очередь, с помощью загруженной в систему проектной 3D-модели объекта можно визуализировать его, увидеть конфигурацию блоков, пространственное расположение оборудования, окружение соседним оснащением, выполнить замеры расстояний между различными элементами установки. Завершается формирование эксплуатационной информационной модели привязкой исполнительной документации и 2D-, 3D-моделей «как построено», предоставляющих возможность получить детализированную информацию о свойствах и технических характеристиках любого оборудования или его элементов на стадии эксплуатации. Таким образом, система представляет собой структурированную и взаимосвязанную совокупность всех инженерных данных объекта и его оборудования.
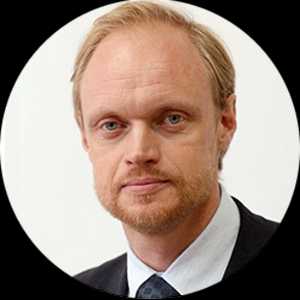
Платформа эффективности – Журнал «Сибирская нефть» — ПАО «Газпром нефть»
«Газпром нефть» одной из первых в мире делает попытку создать полноценное цифровое решение, которое объединило бы нефтепереработку, логистику и сбыт и позволило существенно повысить операционную эффективность компании. Ключевым агрегатором и катализатором проекта станет Центр управления эффективностью, открывшийся в мае в Санкт-Петербурге
Элементы цифровизации неуклонно входят в нашу жизнь. Но в случае с такой сложнейшей технологической отраслью, как нефтепереработка, говорить о комплексных цифровых решениях с использованием элементов Индустрии 4.0 пока не приходится. Причем это касается не только российских, но и мировых лидеров отрасли. Есть решения, которые позволяют оптимизировать технологические процессы; есть системы, следящие за надежностью или энергоэффективностью производства; есть разработки в области скользящего планирования деятельности; наконец, существуют и уже успешно используются алгоритмы для предиктивной аналитики. Но все эти системы, решения, программы не связаны между собой в рамках единой платформы. В мировой практике такой платформы нет не только для всей цепочки добавленной стоимости — от переработки до сбыта, но даже и в рамках одного завода.
Между тем именно здесь кроется существенный потенциал для повышения эффективности операционной деятельности, ведь эффективность отдельных технологических элементов и процессов сегодня уже близка к предельной. Для реализации этого потенциала в блоке логистики, переработки и сбыта (БЛПС) «Газпром нефти» и создается Центр управления эффективностью (ЦУЭ).
Философия интеграции
Несмотря на то что мировая потребность в продуктах нефтепереработки по-прежнему растет, их маржинальность для отдельно взятого завода — величина крайне капризная. Она зависит от мировых цен на нефть и текущего налогового режима, от глубины переработки на конкретном производстве и успешности альтернативной энергетики в регионах сбыта. В таких условиях прибыльность НПЗ постоянно находится под угрозой, а повышение эффективности производства, независимо от сиюминутной конъюнктуры, — не роскошь, а насущная задача.
Понимание этих отраслевых истин позволило «Газпром нефти», невзирая на благоприятную рыночную ситуацию, начать активную работу по модернизации и автоматизации активов БЛПС еще в 2008 году. Сегодня средствами автоматизированного мониторинга охвачены до 90% технологических параметров и материальных потоков по всей цепочке добавленной стоимости, более 150 000 контрольно-измерительных приборов будут передавать информацию в ЦУЭ.
Более половины технологических установок на НПЗ компании оснащены автоматизированными системами управления
Тем временем компания столкнулась с характерной для больших производств проблемой — дальнейшая линейная автоматизация ведет к многократному увеличению получаемых данных, обработать которые привычными вычислительными средствами и тем более человеческими ресурсами просто невозможно. К тому же разрозненные системы позволяют улучшать тот или иной процесс, но не дают комплексного эффекта. Достаточно привести в пример производительность технологических установок — современные системы управления позволяют вести технологический процесс в оптимальных с точки зрения производительности режимах. Но если эти системы не учитывают, что есть еще такие факторы, как энергоэффективность и надежность оборудования, то повышенные затраты энергоресурсов или быстрый износ оборудования могут свести на нет весь экономический эффект от максимальной производительности. «Этот пример можно распространить и на всю цепочку добавленной стоимости, которая в случае с нефтепереработкой вертикально-интегрированной компании включает в себя, помимо НПЗ, логистические и сбытовые активы, — говорит руководитель Центра управления эффективностью Ирина Мартынова. — Так, казалось бы, выгодное компании повышение выпуска продукции, в случае несогласованных действий, легко может привести к невозможности ее своевременной отгрузки на нефтебазы и финансовым потерям последних».
Философия цифровизации, или Индустрии 4.0, говорит о том, что дальнейшее значительное повышение эффективности производственных процессов возможно только благодаря использованию принципиально новых инструментов, таких как Big Data, нейросети, масштабное применение интеллектуальных систем, роботизация. Но стержнем всей концепции остается идея интеграции различных систем и свободного обмена данными между ними. «Холистический подход к управлению производством как единым целым — вот задача, которую будут пытаться решить в Центре управления эффективностью «Газпром нефти», — констатирует Ирина Мартынова.
Цифровой актив
К эре цифровизации нефтепереработка «Газпром нефти» подошла с солидным багажом решений в области автоматизации. Именно они лягут в основу рабочей платформы для ЦУЭ. Задача Центра на ближайшее время — объединить все активы, входящие в цепочку добавленной стоимости, с помощью 60-дневного скользящего планирования с учетом данных за прошедший день и предиктивной аналитики спроса на нефтепродукты, надежности оборудования, качества нефти. Помимо этого важным инструментом операционной деятельности Центра станет система «Нефтеконтроль», создание которой в компании началось еще в 2013 году. Программа позволяет мониторить материальные потоки, начиная с того момента, когда нефть поступает на НПЗ, и заканчивая отгрузкой нефтепродуктов конечному потребителю. Благодаря анализу данных контрольно-измерительных приборов (КИП) программа отслеживает качество и количество флюидов на каждом этапе перемещения потока. С ее помощью можно определять источники отклонений и в конечном итоге выявлять их причины.
«Цифровые двойники» технологических установок дают возможность получать полную информацию о производственных процессах, моделировать и управлять ими, прогнозировать и предотвращать отказы оборудования, подбирать оптимальные режимы работы с учетом большого числа параметров
Работа со всевозможными отклонениями и происшествиями станет еще одной задачей Центра. Причем специалисты будут не просто отрабатывать последствия отклонений, но находить причины сбоев в тех или иных процессах и вырабатывать рекомендации по их устранению. Таким образом удастся вывести работу с отклонениями в рутинные операции, минимизировав их количество и наносимый ущерб.
Особенностью работы Центра, также отражающей идею цифровизации как максимального исключения человеческого участия из процесса обработки данных, станет использование впервые возникших данных в режиме реального времени. То есть практика сбора и дальнейшей обработки отчетов, составленных сотрудниками на местах, уйдет в прошлое. В ЦУЭ для обработки будут поступать данные с датчиков либо внесенные в журналы непосредственными исполнителями. Благодаря такому подходу любые искажения сведений будут сведены к минимуму.
Деятельность Центра управления эффективностью охватывает всю цепочку добавленной стоимости
Входит в планы Центра управления эффективностью и активное участие в процессе создания полноценного «цифрового производства» на нефтеперерабатывающих заводах компании. Идея «цифрового двойника» — еще одно детище новой философии — сегодня уже воплощается в жизнь на НПЗ «Газпром нефти». К настоящему времени оцифрованы две установки — гидроочистки бензинов каталитического крекинга на МНПЗ и установка первичной переработки нефти АТ-9 в Омске. Это пилотный проект, задача которого, помимо непосредственного практического применения, — изучить все возможности, особенности, сложности исполнения «цифрового двойника», найти оптимальные пути его создания, чтобы в будущем тиражировать решение с отдельных технологических установок на технологические цепочки и на все производство в целом. При создании этих «двойников» впервые в компании были применены алгоритмы на основе нейросетей — математических моделей, способных самообучаться с помощью анализа больших массивов данных, находить взаимосвязи между отдельными параметрами и в дальнейшем использовать эти связи для прогнозирования развития ситуации при изменении того или иного параметра. «Сейчас мы заложили основу для создания полноценного «цифрового завода» в будущем, — объясняет начальник департамента систем управления БЛПС «Газпром нефти» Сергей Овчинников. — Пока наши модели могут лишь с определенной точностью рассчитывать различные параметры в любой точке технологической установки. И возможность такого расчета уже дает ощутимые результаты. Но мы надеемся, что в дальнейшем с помощью «цифровых двойников» сможем получать полную информацию о производственных процессах, управлять ими, прогнозировать и предиктивно предотвращать отказы оборудования, подбирать оптимальные режимы
www.gazprom-neft.ru
Заоблачные дали – Журнал «Сибирская нефть» — ПАО «Газпром нефть»
Четвертая промышленная революция, в основе которой лежит глобальная «интернетизация» оборудования, еще несколько лет назад была излюбленной темой футуристов. Сегодня Industry 4.0 стремительно приобретает реальные очертания. На практике это означает, что уже через 10–15 лет промышленные компании, не сумевшие освоить новые технологии, вынуждены будут уходить с рынка
Industry 4.0 — характерный пример того, как количество переходит в качество. Развитие вычислительных мощностей и интернета повлекло за собой лавинообразное увеличение объемов используемой информации. В свою очередь, big data открыли новые возможности для управления, прогнозирования и аналитики. Понимание преимуществ, которые дает работа с информацией, привело к поискам более эффективных технологий получения, передачи, хранения и обработки данных. В результате сегодня уже четко видны основные тренды приближающейся промышленной революции: это облачные решения и максимальное использование интернета вещей. В то же время эксперты единодушно отмечают, что именно эти технологии несут в себе и определенные риски. Причем их масштаб компании, стремящиеся к лидерству любой ценой, зачастую недооценивают.
Нефтепереработка — отрасль достаточно консервативная, основные технологические процессы здесь разработаны сто лет назад. Новых значительных научных открытий в области физики переработки нефти в ближайшее время не предвидится. С точки зрения химии можно ждать прорыва в вопросах катализа, но произойдет ли он завтра или через 20 лет — неизвестно. Поэтому основной способ увеличения маржинальности продукции для любого НПЗ — поиск оптимальных режимов технологических процессов, повышение производительности труда и эффективности управления, энергоэффективность, быстрая реакция на рыночную конъюнктуру. Именно эти задачи способны решать информационные технологии, на которые делается ставка в индустрии будущего. И первые шаги по пути создания новой цепочки добавленной стоимости — за счет автоматизации, а не непосредственного труда рабочих, — лидеры мировой нефтянки уже делают.
Архитектурные сложности
На Западе серьезная автоматизация нефтеперерабатывающих производств с внедрением АСУТП (автоматизированных систем управления технологическими процессами) и переводом части функционала в автопилот запустилась в начале 1990-х. За это время появилась масса систем автоматизации самого разного уровня — от управления технологическим процессом, мониторинга и диагностики оборудования до управления цепочками поставок, календарного планирования, аналитических систем и так далее. Самые продвинутые заводы сегодня — безлюдные, удаленно управляемые, со сроком межремонтного пробега около 10 лет. Их уже можно было бы считать заводами будущего, если бы не одно но: на практике инвестиции в каждый новый виток автоматизации требуют все больше средств и становятся все менее эффективными. Причина кроется в существующей архитектуре промышленных систем автоматизации.
Сегодня рынок промышленной автоматизации — рынок поставщиков. Каждый из них предлагает клиентам свои программные продукты с закрытой архитектурой. В то же время системы разных вендоров плохо интегрируются друг с другом, многие системы, даже одного вендора, несовместимы друг с другом и работают параллельно. Сложности с интеграцией приводят к тому, что компании приходится «подсаживаться» на решения одного производителя и, соответственно, оказываться в ситуации сниженной конкуренции и высоких цен.
«Несовместимость некоторых современных систем автоматизации ведет к разрыву в обработке данных, — объясняет начальник управления промышленной автоматизации „Газпром нефти“ Юрий Новик. — Например, система способна обеспечить оптимальный режим установки на пределе возможностей, но не совмещается с другой системой, которая отвечает за диагностику и безопасную работу этой установки. В итоге мы получаем ситуацию, когда оптимизация не учитывает важные параметры, от которых будет зависеть не сиюминутная эффективность, а общая работоспособность оборудования. И таких разрывов много».
В обычной жизни каждый из нас ежедневно сталкивается с теми широчайшими возможностями, которые дает открытая архитектура программного обеспечения или отдельного аппарата: мы можем без труда воткнуть в компьютер любое периферийное устройство с USB-портом или скачать на телефон очередное приложение. Открытая архитектура промышленных систем автоматизации даст примерно те же преимущества — легкую интеграцию новых компонентов, их взаимозаменяемость (а значит, здоровую конкуренцию и более низкую цену), возможность модернизировать отдельные модули с минимальным ущербом для всего технологического процесса. Мало того, наличие мультивендорной платформы для систем автоматизации полностью перевернет рынок, превратив его в рынок потребителя.
Первой работу над созданием новой архитектуры систем промышленной автоматики начала компания Exxon Mobil. Остальным представителям отрасли остается либо ждать появления готового решения, либо заняться разработкой собственного. «Российские предприятия сегодня значительно отстают от зарубежных по степени автоматизации, — констатирует Юрий Новик. — Поэтому для нас создание собственной мультивендорной платформы — это реальная возможность сделать существенный скачок и выйти на уровень лучших из лучших. В противном случае мы всегда будем в роли догоняющих». Работа в этом направлении на национальном уровне важна еще и тем, что любые новые разработки в парадигме Industry 4.0 тесно связаны с использованием интернета вещей и облачных решений. А здесь уже остро встает вопрос не только коммерческого успеха, но и безопасности бизнеса.
Центр управления эффективностью операций
Одна из тенденций, характерных для цифрового производства или производства будущего, — возможность совместной работы специалистов разного профиля для выработки оптимального решения сложных задач. В «Газпром нефти» уже реализовано несколько проектов, объединяющих разные функции. В частности, в Научно-техническом центре компании работает Центр сопровождения бурения, обеспечивающий всестороннюю экспертизу при строительстве высокотехнологичных скважин.
В свою очередь в блоке логистики, переработки и сбыта создается Центр управления эффективностью операций — программа, задача которой — интегрировать информацию из различных систем, работающих на НПЗ, от видеокамер до системы KPI, и затем предоставлять эту информацию пользователю в удобном для него виде. Помимо информационной функции, Центр управления позволяет одновременно задействовать большое количество людей для обсуждения происходящего на отдельной установке или производстве в целом.
Всегда на связи
Основная движущая сила четвертой промышленной революции — активное использование возможностей интернета вещей. В общем случае это означает построение сети, которая объединяет физические предметы, оснащенные встроенными технологиями для взаимодействия друг с другом или с внешней средой. В промышленности этот принцип уже давно используется при построении АСУТП, но постоянно развивающиеся возможности для передачи, хранения и обработки данных выводят промышленный интернет вещей на глобально другой уровень.
Можно выделить два направления, в которых сетевые технологии, по мнению экспертов, уже через несколько лет станут ключевым элементом. Во-первых, сервисное обслуживание оборудования. Уже сегодня при покупке сложной техники, например такой, как автомобиль, важным преимуществом становится простота управления и обслуживания. За услугу удаленного управления или диагностики потребитель готов платить, и стоимость подобного сервиса в общей цене постоянно возрастает.
«В будущем любой завод, в том числе и НПЗ, будет похож на лего, — считает Юрий Новик. — Оборудование будет приходить в виде коробки, включающей в себя как железо, так и необходимое ПО для его диагностики и обслуживания. Причем оборудование, к которому не приложены подобные системы, окажется никому не нужным». В этой схеме покупатель будет платить не столько за саму технику, сколько за ее дальнейшее обслуживание. В то же время производитель будет заинтересован в снижении собственных затрат на ремонт. Минимизировать их можно только за счет тщательной и своевременной диагностики. Здесь-то на первый план и выходит промышленный интернет, обеспечивающий постоянную передачу информации о состоянии оборудования и условиях его эксплуатации в сервисный центр.
www.gazprom-neft.ru
ОГРН | 1026600000459 |
ИНН | 6670001804 |
КПП | 667001001 |
Организационно-правовая форма (ОПФ) | Общественные организации |
Полное наименование юридического лица | ОБЪЕДИНЕННАЯ ПЕРВИЧНАЯ ПРОФСОЮЗНАЯ ОРГАНИЗАЦИЯ "ГАЗПРОМ ТРАНСГАЗ ЕКАТЕРИНБУРГ ПРОФСОЮЗ" |
Сокращенное наименование юридического лица | ОППО "ГАЗПРОМ ТРАНСГАЗ ЕКАТЕРИНБУРГ ПРОФСОЮЗ" |
Регион | Свердловская область |
Юридический адрес | 620000, Свердловская область, город Екатеринбург, улица Клары Цеткин, д. 14 |
Регистратор | |
Наименование | Инспекция Федеральной налоговой службы по Верх-Исетскому району г.Екатеринбурга, №6658 |
Адрес | 620014, Екатеринбург г, Хомякова ул, 4 |
Дата регистрации | 11.07.2001 |
Дата присвоения ОГРН | 28.08.2002 |
Учёт в ФНС | |
Дата постановки на учёт | 17.07.2001 |
Налоговый орган | Инспекция Федеральной налоговой службы по Кировскому району г.Екатеринбурга, №6670 |
Сведения о регистрации в ПФР | |
Регистрационный номер | 075030026121 |
Дата регистрации | 20.08.2001 |
Наименование территориального органа | Управление Пенсионного фонда Российской Федерации по Кировскому району г.Екатеринбурга, №075030 |
Сведения о регистрации в ФСС | |
Регистрационный номер | 660861820266131 |
Дата регистрации | 24.12.2017 |
Наименование исполнительного органа | Филиал №13 Государственного учреждения - Свердловского регионального отделения Фонда социального страхования Российской Федерации, №6613 |
egrinf.com
Ставка на опережение – Журнал «Сибирская нефть» — ПАО «Газпром нефть»
Будущее мировой нефтепереработки — максимально возможная интеллектуализация и автоматизация технологических и управленческих процессов. В «Газпром нефти» для отбора лучших и создания новых решений в этой области создан технопарк промышленной автоматизации
Управление современным нефтеперерабатывающим заводом невозможно без средств автоматизации. Контрольно-измерительные приборы отслеживают параметры (температуру, давление и т.д.) на отдельных участках установок. АСУТП (автоматизированные системы управления технологическим процессом) управляют сложнейшими технологическими процессами и обеспечивают безопасность производства, АСУП (автоматизированные системы управления предприятием) аккумулируют производственную, финансовую, управленческую информацию, помогая принимать решения на самом высоком уровне. Степень автоматизации производства и эффективность используемых систем сегодня становятся одним из определяющих конкурентных преимуществ для любого НПЗ. Заводы «Газпром нефти» — лидеры в этом направлении в России.
В 2015 году в Омске на базе дочернего предприятия «Автоматика-сервис» был создан технопарк промышленной автоматизации. Изначально его основной задачей были поиск и испытание новых решений в области автоматизации. Отдельное внимание в условиях санкционных войн уделялось отечественным разработкам. Сегодня в технопарке ставятся цели на порядок сложнее — перейти от импортозамещения и отбора лучших мировых практик к инновационному импортоопережению. Принять участие в разработке решений, не имеющих мировых аналогов и способных закрыть самые слабые места в автоматизации различных процессов на НПЗ.
Кроме того, технопарк стал не просто испытательным полигоном, но и научно-образовательной площадкой нового типа. Здесь повышают квалификацию сотрудники корпоративного центра «Газпром нефти», «Автоматики-сервис», персонал технологических установок Омского НПЗ и других дочерних обществ. В технопарке регулярно занимаются бакалавры и магистры базовой кафедры «Газпром нефти» Омского государственного технического университета, обучающиеся по направлениям автоматизации.
Менее чем за два года работы технопарка на рассмотрение специалистов было подано 152 заявки с описанием различных проектов, 88 заявок было утверждено и принято в работу.
Сергей Овчинников, начальник департамента систем управления БЛПС «Газпром нефти»:
Технопарк создавался в контексте лучших мировых практик. Этот центр одновременно стал и эффективной средой для испытания перспективных решений, и современной научно-образовательной базой для целого комплекса прикладных исследований. Удалось апробировать системы управления производством следующего поколения, которые еще мало где внедрены. Благодаря созданию технопарка специалисты «Газпром нефти» увидели реальные возможности инновационных систем от ведущих мировых производителей, сделан серьезный шаг в части использования отечественных технологий и оборудования.
На следующем этапе из испытательного полигона технопарк должен быть трансформирован в центр разработки перспективных решений, тесно интегрированный с научно-исследовательской средой крупных профильных вузов России, таких как СПбГПУ, ОмГТУ, ТюмГНГУ, РГУ им. Губкина и других. Комплексная работа по развитию технопарка уже сегодня направлена на возрождение инновационного подхода в сфере промышленной автоматизации в России. Уверен, что в перспективе мы способны предложить собственные решения по КИПиА и АСУТП, превосходящие лучшие практики по соотношению цена-качество.
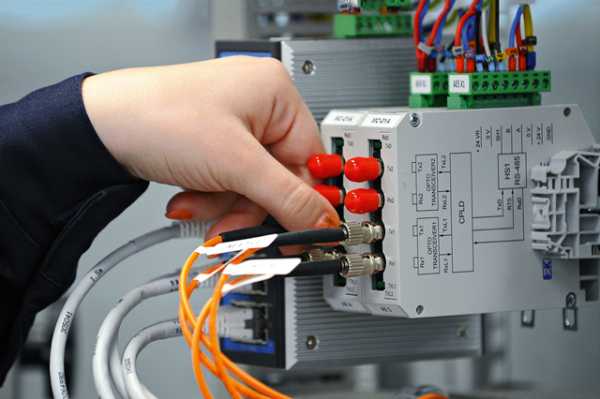
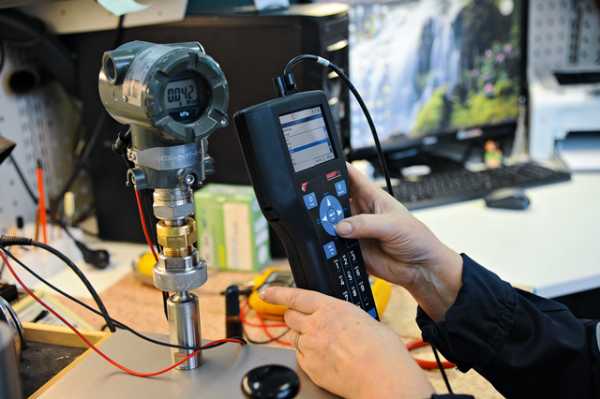
На этапе контроля
Контрольно-измерительные приборы лежат в основании так называемой пирамиды автоматизации любого производства. Именно с них поступает основной объем данных на системы управления, и от точности их показаний получаемая на заводе прибыль порой зависит не меньше, чем от ситуации на рынке. До последнего времени нефтеперерабатывающие производства «Газпром нефти» закупали большую часть КИПиА (контрольно-измерительные приборы и автоматика) за рубежом — на импорт приходилось порядка 90% такого оборудования. Изменившаяся экономическая ситуация заставила по-новому взглянуть на возможности отечественных производителей. В результате в деле импортозамещения КИПиА в рамках работы технопарка удалось добиться существенных успехов. В 2015–2016 гг. по многим позициям были найдены альтернативы зарубежным аналогам и проведены испытания российских датчиков давления, уровня, расхода и т.д.
Тестируемые приборы в течение полугода проверялись в реальных производственных условиях Омского НПЗ. Шесть месяцев на проверку определены не случайно. За этот срок в условиях резко континентального климата Западной Сибири удается проверить чувствительность приборов к перепадам температур в межсезонье и в течение суток, тем самым выявить их слабые места для дальнейшей доработки, и в целом — совместимость заявленных характеристик и технологических потребностей предприятия.
Рустем Муфтеев, генеральный директор «Автоматики-сервис»:
В достаточно сложных для России экономических условиях санкций, волатильности курсов валют и низкой стоимости углеводородов вопросы повышения эффективности производства становятся еще более актуальными. И автоматизация производства — один из наиболее эффективных инструментов, способных при относительно небольших вложениях и в короткие сроки успешно решать данную задачу. Таким инструментом и стал технопарк — фактически площадка для активного взаимодействия разработчиков и производителей с конечными потребителями продуктов и решений. Почти два года работы технопарка полностью подтвердили его эффективность. Сегодня успешно решается задача обеспечения устойчивой работы действующих на НПЗ «Газпром нефти» систем автоматизации производства — даже в случае усиления санкционного давления. В рамках НИОКР специалистами «Автоматики-сервис» разработаны собственные решения, направленные на обеспечение безопасного функционирования технологических установок и повышение эффективности работы контуров управления. И это только начало.
Одно из основных условий для сотрудничества технопарка с отечественными производителями — готовность последних к изменениям в соответствии с требованиями заказчика. Такой подход позволяет быстро находить оптимальные решения. Как отмечает руководитель технопарка Владимир Клевакин, специалисты центра координируют работу по адаптации оборудования к особенностям технологических процессов «Газпром нефти». И, по мнению экспертов технопарка, в большинстве случаев у отечественных производителей получается оперативно и грамотно совершенствовать свои приборы и становиться потенциальными поставщиками «Газпром нефти».
Например, одно из современных требований к датчикам — наличие различных цифровых протоколов передачи данных с вытекающей отсюда функцией самодиагностики приборов — было успешно реализовано на отечественном оборудовании, что сделало его вполне конкурентоспособным по сравнению с зарубежными аналогами.
С момента открытия технопарка доля российских производителей контрольно-измерительных приборов среди потенциальных поставщиков «Газпром нефти» значительно выросла. Впрочем, проблема импортозамещения еще только начинает решаться. В частности, с контрольно-измерительными приборами более высокого уровня, например, поточными анализаторами качества или расходо-массовыми приборами, ситуация сложнее. Здесь пока выигрывают зарубежные производители, а специалистам технопарка остается искать лучшие предложения от компаний, не обремененных санкционными рисками.
Потенциал управления
Создание автоматизированных систем управления для таких крупных и сложных производств, как НПЗ, до сих пор оставалось привилегией нескольких компаний — признанных мировых лидеров. Тем не менее, по словам экспертов технопарка, результаты поиска и тестирования альтернативных автоматизированных систем управления технологическим процессом оказались лучше, чем ожидалось.
Доминирование на мировом рынке известных разработчиков и производителей АСУТП не останавливает другие компании, в том числе — в России. Вместе с поиском отечественных систем специалисты технопарка сделали обзор продуктов производителей стран БРИКС — так в технопарке появились бразильские и сингапурские фирмы, демонстрирующие неплохие результаты относительно действующих лидеров.
Работа с АСУТП наиболее ярко проявила достоинства формата технопарка, так как, в отличие от КИПиА, АСУТП нельзя установить и протестировать на действующем производстве. Поэтому в Омске были разработаны специальные методики испытаний автоматизированных систем управления. К настоящему времени протестировано более десятка АСУТП различного уровня и функционального назначения, включая системы противоаварийной защиты и распределенные системы управления технологическими процессами. В результате были выделены системы, которые можно уже сейчас использовать для вспомогательных производств, и еще несколько систем после небольших доработок могут быть применимы на более сложных процессах. Над созданием систем противоаварийной защиты, отвечающих самым высоким стандартам надежности, российским разработчикам еще придется потрудиться.
Создание производственных моделей — одно из ключевых направлений технологического развития
«Успешное тестирование и адаптация отечественных решений под требования и нужды „Газпром нефти“ не обеспечивают автоматическое внедрение оборудования на объектах компании, — отметил руководитель технопарка „Газпром нефти“ Владимир Клевакин. — Все партнеры технопарка проходят тендерные процедуры „Газпром нефти“ на общих основаниях. Но, как показала наша практика, российские КИПиА при аналогичном качестве с импортными оказываются несколько дешевле. Отечественные АСУТП получаются примерно на треть дешевле аналогов. То есть шансы стать реальным поставщиком „Газпром нефти“ у резидентов технопарка есть».
Приятной неожиданностью для экспертов стали отечественные разработки следующего уровня — автоматизированные системы управления предприятием. Так, в 2016 году в технопарке прошла тестирование российская система баз данных реального времени. Она оказалась близкой к лучшим мировым практикам.
Работа на опережение
«На самом деле импортозамещение только первый этап в работе технопарка, — считает Владимир Клевакин. — Сегодня нас интересует следующий шаг развития — работа на импортоопережение. Мы знаем „болевые точки“ автоматизации компании и пытаемся оценить возможные решения. Изучаем, привлекаем и тестируем лучшие мировые практики на применимость к нашим реалиям. Но мы понимаем, что у нас есть особенные „точки“, для которых сейчас в мире нет готовых решений. Например, существует проблема — как преобразовать объемный календарный план в действующую модель производства, то есть расписать производственный план на заданный период по конкретной установке, вплоть до режимов отдельных колонн и секций. В этой сфере мы поэтапно переходим к разработке совместных и собственных решений, координируя работу над компонентами импортоопережающих разработок».
Для развития таких проектов технопарк налаживает связь с научно-образовательными и инновационными центрами России, в том числе Омским государственным техническим университетом, фондом «Сколково» и Национальной ассоциацией участников рынка промышленного интернета (НАПИ). Так, в рамках НИОКР специалисты Омского государственного технического университета ведут разработку беспилотного летающего робота-сканера для контроля над строительством объектов НПЗ. Комплекс состоит из квадрокоптера, оснащенного видеокамерой, и соответствующего программного обеспечения, позволяющего аккумулировать и анализировать собранную летательным аппаратом информацию и в автоматическом режиме формировать отчет. Этот тандем будет способен в режиме реального времени вести мониторинг всех этапов строительства на технологических установках нефтеперерабатывающих заводов «Газпром нефти». Комплекс сможет не только показать общую картину, но и выявить отклонения в строительном процессе объекта от проектных характеристик. Аналогов подобного комплекса в мире пока не существует.
Предупрежден — значит, защищен
Одна из ключевых тенденций в управлении НПЗ сегодня — переход от планово-предупредительного обслуживания оборудования к обслуживанию «по текущему состоянию». Такой подход позволяет значительно сократить риск возникновения аварийных ситуаций, но, в свою очередь, требует внедрения и развития систем диагностики. Поэтому еще одним важным проектом технопарка стало создание прототипа центра мониторинга и диагностики.
Задача подобного центра — постоянное отслеживание работоспособности средств автоматизации, а именно — технологических сигнализаций, контрольно-измерительных приборов, систем автоматического регулирования, противоаварийной защиты и т.д. По специальному набору параметров система мониторинга позволяет спрогнозировать дальнейшее поведение «наблюдаемого объекта» и сработать на упреждение.
Центр мониторинга и диагностики создается на Омском НПЗ специалистами «Автоматики-сервис», а отдельные решения, применяемые в нем, тестируются в технопарке. Сегодня на ОНПЗ уже начался плавный переход от планово-предупредительного ремонта оборудования к проактивному сервису — техническому обслуживанию оборудования «по состоянию». В итоге через настройки и профилактическое техническое обслуживание оборудования и систем специалисты ставят амбициозную цель — довести количество технических отказов до нуля, что позволит достичь значительного роста производственной эффективности.
Сотрудники «Автоматики-сервис» Елена Гурьева (учится на базовой кафедре «Газпром нефти» Омского государственного технического университета) и Руслан Меркулов заняли призовое место на научно-технической конференции молодых специалистов блока логистики, переработки и сбыта «Газпром нефти», прошедшей в Санкт-Петербурге. Специалисты представили работу на тему «Автоматизированная система определения истинной температуры кипения (ИТК) нефти», которая сегодня проходит апробацию в технопарке.
Сегодня на отечественных установках атмосферной и вакуумной перегонки нефти (АВТ) наблюдается неполнота разделения нефти. Отсутствие оперативной информации о фактических значениях состава сырья приводит к потерям в отборах целевых продуктов, которые составляют от 0,1 до 0,5% масс. Разработанная молодыми сотрудниками система нацелена на снижение этих потерь. Также ее можно применять в режиме «советчика» для формирования ключевых показателей эффективности при извлечении светлых нефтепродуктов на установках АВТ. Кроме того, она позволит предоставлять информацию об ИТК нефти в систему усовершенствованного управления технологией производства (СУУТП) для корректировки режима работы АВТ и увеличения отбора целевых продуктов.
www.gazprom-neft.ru