Способ деэтанизации нестабильного газового конденсата и установка для его осуществления. Минигулов рафаиль минигулович новатэк
УСТРОЙСТВО ПОДГОТОВКИ СМЕСИ ГАЗООБРАЗНЫХ УГЛЕВОДОРОДОВ ДЛЯ ТРАНСПОРТИРОВКИ
Изобретение относится к области нефте- и газодобывающей промышленности, а также к области переработки углеводородов и может быть использовано при подготовке газообразного углеводородного сырья для транспортировки, а также при утилизации нефтяного попутного газа.
Известно (Бекиров Т.М., Ланчаков Г.А. Технология обработки газа и конденсата. М., «Недра», 1999, стр.306-308) устройство подготовки смеси газообразных углеводородов для транспортировки. Устройство содержит первичный сепаратор, предназначенный для отделения от исходного газового потока механических примесей, воды и углеводородного (нестабильного) конденсата. Из первичного сепаратора газ последовательно проходит первый и второй теплообменники типа «газ-газ», где охлаждается обратным потоком газа, отводимым с верха низкотемпературного сепаратора концевой ступени. Между первым и вторым теплообменниками установлен промежуточный сепаратор, в котором отделяют образовавшуюся в результате охлаждения в первом теплообменнике жидкость. Затем газ дросселируют для охлаждения газа и уменьшения давления. Охлажденный газ поступает в указанный низкотемпературный сепаратор. Отбензиненный и осушенный газ из низкотемпературного сепаратора последовательно проводит через второй и первый теплообменники и после хозрасчетного замера поступает в газовый коллектор. Для осуществления безгидратного режима работы установки в поток газа между первым и вторым теплообменниками подают раствор метанола. Потоки конденсата (смесь конденсата, пластовой воды и метанола) из первичного сепаратора и промежуточного сепаратора объединяют и подают в первый разделитель, а из низкотемпературного сепаратора - во второй разделитель. После частичной дегазации потоки конденсата объединяют и отправляют на завод по переработке конденсата. Из первого и второго разделителей раствор метанола поступает на регенерацию.
Недостатком известной установки следует признать сложность ее применения в сложных природно-климатических условиях вдали от систем транспортирования газа и потребителей пропан-бутановой фракции из-за нерешенности проблемы, как утилизации, так и переработки пропан-бутановой фракции.
Технический результат, получаемый при реализации разработанной установки, состоит в подготовке смеси газообразных углеводородов к транспортировке, в том числе, и в условиях Крайнего Севера.
Для достижения указанного технического результата предложено использовать разработанную установку подготовки смеси газообразных углеводородов для транспортировки. Разработанная установка содержит установленные последовательно магистраль подачи исходного сырьевого потока, первый сепаратор для разделения газообразной фазы и жидкой фазы, разделитель жидкой фазы на отделенный газообразный компонент, скважинную воду, направляемую на утилизацию, и нестабильный конденсат, направляемый на дальнейшую переработку, второй сепаратор, предназначенный для разделения отделенного газообразного компонента на подготовленный газ и нестабильный конденсат, направляемый на дальнейшую переработку, первый рекуперативный теплообменник, на первый вход которого поступает объединенный нестабильный конденсат, при этом первый выход которого по нестабильному конденсату подключен к колонне деэтанизации, выполненной с возможностью подачи нестабильного конденсата как в среднюю, так и в верхнюю части, выход по газу колонны деэтанизации подключен через первый вход эжектора к входу второго сепаратора, выход по жидкой фазе колонны деэтанизации подключен к средней части колонны стабилизации, выход которой по пропан-бутановой фракции подключен через второй рекуперативный теплообменник к первому реактору ароматизации, выход первого реактора ароматизации подключен к входу второго реактора ароматизации, выход которого через указанный второй рекуперативный теплообменник подключен к первому и второму дополнительным сепараторам, первый из которых предназначен для отделения газа регенерации от воды, сбрасываемой на утилизацию, а второй дополнительный сепаратор через третий рекуперативный теплообменник подключен по жидкой фазе к средней части колонны ректификации, выход второго дополнительного сепаратора по газу подключен к указанному первому входу эжектора, выход колонны ректификации по концентрату ароматических углеводородов подключен к магистрали концентрата ароматических углеводородов склада, выход по газу колонны ректификации соединен с верхней частью колонны ректификации, а также с указанным первым входом эжектора, выход первого сепаратора по газовой фазе соединен через второй вход эжектора с входом второго сепаратора, выход колонны стабилизации по стабильному конденсату подключен к магистрали стабильного конденсата склада, между первым сепаратором и первым рекуперативным теплообменником выполнена врезка для подачи ингибитора гидратообразования.
В некоторых вариантах реализации между вторым сепаратором и первым рекуперативным теплообменником дополнительно может быть установлен разделитель, предназначенный для отделения ингибитора гидратообразования от нестабильного конденсата, причем выход ингибитора гидратообразования подключен к указанной врезке.
Колонны ароматизации могут иметь параллельное подключение двух аналогичных колонн, используемых при проведении регламентных работ на основных колоннах ароматизации.
Разработанное устройство в наиболее предпочтительном варианте реализации приведено на схеме, при этом использованы следующие обозначения: первый сепаратор 1, трехфазный разделитель 2, емкость выветривания 3, первый рекуперативный теплообменник 4, второй низкотемпературный сепаратор 5, эжектор 6, второй разделитель 7, колонна деэтанизации 8, теплообменник 9, колонна стабилизации 10, холодильник 11, емкость 12, второй рекуперативный теплообменник 13, первый реактор 14, снабженный катализатором и тепловыми трубами, второй реактор 15, снабженный катализатором и тепловыми трубами, первый воздушный холодильник 16, третий сепаратор 17, колонна 18, теплообменник 19, емкость 20, второй воздушный холодильник 21, третий воздушный холодильник 22, четвертый воздушный холодильник 23, четвертый сепаратор 24.
В предпочтительном варианте реализации разработанное устройство работает следующим образом.
Сырьевой поток (продукцию газоконденсатной скважины) направляют в первый сепаратор 1, из которого жидкую фазу отводят в трехфазный разделитель 2. Из указанного разделителя 2 пластовую воду отводят на утилизацию, а нестабильный конденсат отводят в емкость выветривания 3.
Углеводородный газ из первого сепаратора 1 последовательно охлаждают в рекуперативном теплообменнике 4 за счет контакта с охлажденным подготовленным газом, выходящим из второго низкотемпературный сепаратора 5, а также в эжекторе 6 за счет сброса давления на нем. После эжектора 6 в основной поток подготавливаемого газа вводят газ из трехфазного разделителя 2. Перед рекуперативном теплообменником 4 для предотвращения опасности выпадения кристаллогидратов в сырьевой газ для связывания выделяющейся при охлаждении воды впрыскивают ингибитор гидратообразования, в качестве которого используют предпочтительно 90% водный раствор метанола или 80% водный раствор этиленгликоля.
Охлажденную до температуры - 5÷-40°C газожидкостную смесь подают в низкотемпературный сепаратор 5, из которого подготовленный газ после подогрева в рекуперативном теплообменнике 4 поступает в транспортный газопровод. Жидкую фазу из низкотемпературного сепаратора 5 разделяют во втором разделителе 7 на насыщенный водой ингибитор кристаллообразования и нестабильный конденсат. Ингибитор после отделения излишней воды на установке регенерации рециркулируют в поток газа после первого сепаратора 1, а нестабильный конденсат подают в емкость выветривания 3 с нестабильным конденсатом из трехфазного разделителя 2.
Нестабильный конденсат из емкости выветривания 3 разделяют на два потока, один из которых используют для орошения колонны деэтанизации 8, а второй - как питание этой колонны деэтанизации 8 после нагрева в теплообменнике 9. Газ выветривания из емкости выветривания 3 и газ деэтанизации из колонны деэтанизации 8 утилизируют в эжекторе 6.
Деэтанизированный (освобожденный от метана и этана) конденсат от низа колонны деэтанизации 8 отводят на ректификацию в колонну стабилизации 10. Стабильный конденсат от низа колонны стабилизации 10 охлаждают в теплообменнике 9 и отводят на склад. Пары верха колонны стабилизации 10 конденсируют в холодильнике 11 и собирают в емкости 12, откуда насосом часть полученной пропан-бутановой фракции направляют в виде орошения на верх колонны стабилизации 10, а балансовую часть пропан-бутановой фракции направляют на переработку.
Для поддержания температурного режима низа колонн деэтанизации 8 и стабилизации 10 в их кубовые части подводят тепловую энергию - соответственно Q1 и Q2.
Пропан-бутановую фракцию после предварительного нагрева в теплообменнике 13 для осуществления процесса дегидроциклодимеризации вводят последовательно в два реактора ароматизации, снабженный катализатором и тепловыми трубами для поддержания адиабатического режима работы: сначала в 14 для преобразования бутана в соединения ароматического ряда при температуре от 470 до 500°C, а затем в 15 для превращения пропана в соединения ароматического ряда при температуре от 510 до 540°C.
Для поддержания соответствующего режима в реакторы 14 и 15 дополнительно подводят тепловую энергию - соответственно Q3 и Q4.
Полученные продукты реакции (катализат) охлаждают в теплообменнике 13 и первом воздушном холодильнике 1 6, после чего жидкую фазу отделяют от неконденсирующихся газов в третьем сепараторе 17. Газы отводят на утилизацию в эжектор 6, а жидкую фазу подают на ректификацию в колонну 18 после предварительного нагрева в теплообменнике 19. Температуру низа колонны 18 обеспечивают подачей дополнительной тепловой энергии Q5, а температуру верхней части колонны 18 регулируют подачей орошающей жидкой фазы из емкости 20 насосом. Жидкость для орошения получают путем конденсации во втором воздушном холодильнике 21 паров верха колонны 18 (в основном, непрореагировавшей части пропан-бутановой фракции). Избыток пропан-бутановой фракции возвращают в сырьевой поток перед реакторами. Готовый продукт - концентрат углеводородов ароматического ряда - после охлаждения в теплообменнике 19 и третьем воздушном холодильнике 22 направляют на склад.
Регенерацию катализатора в реакторах 14 и 15 осуществляют при температуре 500-550°C подачей азото-воздушной смеси после предварительного ее нагрева в теплообменнике 13 отработанными продуктами регенерации. Выходящие газы регенерации охлаждают в теплообменнике 13 и четвертом воздушном холодильнике 23, а затем разделяют в сепараторе 24, сконденсировавшуюся жидкость (в основном, воду) сбрасывают на утилизацию, а газовую фазу отводят на рассеивание в атмосфере.
Применение разработанного способа позволяет:
- отказаться от использования дорогостоящих и занимающих большую площадь товарных парков и устройств налива сжиженной пропан-бутановой фракции на давление 2,0 МПа за счет переработки ее в стабильную жидкость - концентрат ароматических углеводородов - и углеводородный газ;
- полученный углеводородный газ вернуть в основной поток газа.
Разработанный способ наиболее целесообразно использовать на отдаленных газоконденсатных и нефтегазовых месторождениях при сложных аспектах обустройства этих месторождений: суровых природно-климатических условиях, наличие вечной мерзлоты, полное отсутствие инфраструктуры, отдаленности от систем транспорта и потребителей пропан-бутановой фракции.
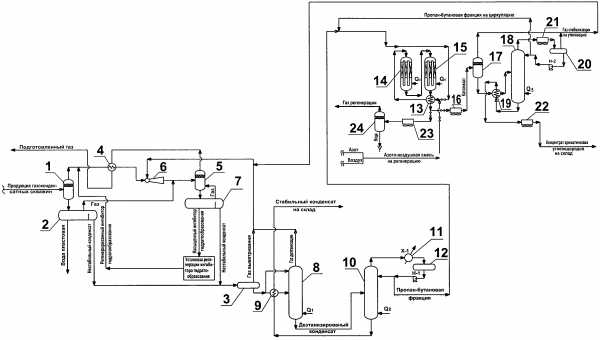
edrid.ru
Способ получения сжиженных углеводородных газов и установка для его осуществления
Изобретение относится к технике получения сжиженных углеводородных газов и их очистки от метанола и может быть использовано в газовой, нефтяной, нефтеперерабатывающей, нефтехимической и химической отраслях промышленности. Способ получения сжиженных углеводородных газов включает стабилизацию деэтанизированного газового конденсата путем выделения из него углеводородных газов, их охлаждение, смешивание сжиженных углеводородных газов (СУГ) с водой, отмывки метанола и фазовое разделение на СУГ и водометанольный раствор. При этом на стадии отмывки смесь СУГ с водой диспергируют в водной фазе, затем проводят коалесценцию мелкодиспергированных капель водометанольного раствора, после чего осуществляют фазовое разделение. Установка для получения сжиженных углеводородных газов содержит последовательно соединенные ректификационную колонну стабилизации газового конденсата, аппарат охлаждения, смесительное устройство, по меньшей мере, одну емкость отмывки метанола и разделительную емкость. При этом, по меньшей мере, одна емкость отмывки метанола и разделительная емкость выполнены в виде секций емкости-фильтра, разделенного двумя перегородками с размещенными в них коалесцирующими фильтр-патронами с образованием трех секций во внутренней полости упомянутого фильтра, причем две секции представляют собой емкости отмывки метанола, а третья секция - разделительную емкость. Использование изобретения позволит минимизировать капитальные и текущие затраты на установку за счет ее упрощения. 2 н. и 3 з.п. ф-лы, 3 ил.
Изобретение относится к технике и технологии получения сжиженных углеводородных газов, к которым относятся смесь пропана и бутана технических, пропан технический, бутан технический (далее СУГ), и их очистки от метанола и может быть использовано в газовой, нефтяной, нефтеперерабатывающей, нефтехимической и химической отраслях промышленности.
Основная доля получаемых отечественными компаниями СУГ производится из газового конденсата, выделяемого на установках комплексной подготовки газа (УКПГ), работающих по технологии низкотемпературной сепарации, где метанол используется в качестве ингибитора гидратообразования. Большая часть метанола отводится с УКПГ в виде водометанольной смеси после трехфазных разделителей «углеводороды - метанольная вода - газ выветривания». Однако в результате растворимости метанола в газовом конденсате остаточное содержание метанола в продуктах дальнейшей переработки газового конденсата может изменяться в достаточно широком диапазоне.
Данная проблема усугубляется тем, что в процессе переработки газового конденсата с получением стабильного конденсата (СК) и товарных сжиженных газов (смеси пропана и бутана технических) практически весь водометанольный раствор переходит в состав сжиженных газов. Это приводит к существенному повышению концентрации растворимого метанола в товарных сжиженных газах до 18000 ppm. Co временем значительная часть водометанольного раствора выделяется из СУГ в виде отдельной фазы. Частично отделение происходит на товарных складах производителей СУГ, где водометанольный раствор «подрезается» и отводится в дренажную систему. Однако значительная часть BMP выделяется уже после отгрузки СУГ потребителям. В этом случае потребители вполне обосновано предъявляют претензии производителям и требуют возмещения понесенных убытков.
В настоящее время большинство производителей СУГ пытаются решать данную проблему путем применения метода экстракции метанола водой.
Для выполнения данной задачи чаще всего используют огромные резервуары-отстойники, насосное оборудование подачи СУГ и воды. Эффективность данного способа очистки СУГ крайне низкая и, как правило, не приводит к желаемым результатам. Более того, в данном случае возникает необходимость в строительстве дополнительно узла подготовки химочищенной воды и утилизации большого количества сточных вод, что при отсутствии гарантий выполнения контрактных обязательств перед заказчиком накладывает негативный отпечаток на рентабельность производства в целом.
Известен способ (патент РФ №2286194) очистки жидких углеводородов от метанола, находящихся в виде эмульсии, включающий нагрев эмульсии, разделение путем сепарации нагретой эмульсии на жидкие углеводороды и водный раствор метанола и последующий их раздельный отвод.
Недостатками описанного способа являются большие энергетические затраты на нагрев эмульсии и низкая эффективность процесса сепарации из-за плохого осаждения водного раствора метанола в жидких углеводородах, легкие компоненты которых при нагреве испаряются и (или) кипят.
Наиболее близким является способ (RU 2289608, опубл. 20.12.2006) очистки жидких углеводородов от метанола, включающий стабилизацию жидкого углеводородного сырья путем выделения из него легкой фракции - сжиженных углеводородных газов (СУГ), экстракцию метанола из СУГ, сепарацию водного раствора метанола и СУГ и адсорбционную очистку СУГ.
Установка для реализации данного способа содержит ректификационную колонну для разделения жидкого углеводородного сырья, например нестабильного газового конденсата (НГК), на легкую фракцию - СУГ и тяжелую фракцию, например стабильный газовый конденсат (СГК), соединенную через охлаждающее устройство с экстракционной колонной для отмывки метанола от СУГ, соединенное с разделителем, из которого отделенный водометанольный раствор подается в емкость, а СУГ - в блок адсорбционной очистки.
Однако данный способ ввиду своей многостадийности является достаточно сложным и дорогостоящим, подходящим только для случаев, когда предъявляются очень жесткие требования по содержанию метанола в СУГ (не более 50 ppm).
Задачей предлагаемого изобретения является минимизация капитальных и текущих затрат на установку по получению СУГ с содержанием водометанольного раствора не более 6000 ppm за счет упрощения схемы установки путем исключения блока адсорбционной очистки и использования рефлюксной емкости вместо блока отмывки, включающего несколько аппаратов.
Поставленная задача решается способом получения сжиженных углеводородных газов, включающим стабилизацию деэтанизированного газового конденсата путем выделения из него углеводородных газов, их охлаждение, смешивание сжиженных углеводородных газов (СУГ) с водой, отмывку метанола и фазовое разделение на СУГ и водометанольный раствор, согласно которому на стадии отмывки смесь СУГ с водой диспергируют в водной фазе, затем проводят коалесценцию мелкодиспергированных капель водометанольного раствора, после чего осуществляют фазовое разделение.
При этом смешивание СУГ с водой осуществляют предпочтительно в вихревом режиме.
Задача также решается установкой для получения сжиженных углеводородных газов, содержащей последовательно соединенные ректификационную колонну стабилизации газового конденсата, аппарат охлаждения, смесительное устройство, по меньшей мере, одну емкость отмывки метанола и разделительную емкость, при этом, по меньшей мере, одна емкость отмывки метанола и разделительная емкость выполнены в виде секций емкости-фильтра, разделенного двумя перегородками с размещенными в них коалесцирующими фильтр-патронами с образованием трех секций во внутренней полости упомянутого фильтра, причем две секции представляют собой емкости отмывки метанола, а третья секция - разделительную емкость.
Кроме того, смесительное устройство предпочтительно представляет собой устройство вихревого типа.
При этом каждый коалесцирующий фильтр-патрон выполнен из гидрофильного стекловолокна.
На фиг.1 приведена технологическая схема установки для получения СУГ.
На фиг.2 приведена схема емкости-фильтра.
На фиг.3 - сечение А-А на фиг.2.
Установка для получения сжиженных углеводородных газов включает ректификационную колонну 1 стабилизации газового конденсата и емкость-фильтр 2 для отмывки метанола и фазового разделения водной и углеводородной фаз. Выход колонны 1 для легких фракций соединен с аппаратом 3 воздушного охлаждения, который в свою очередь соединен с смесительным устройством 4 вихревого типа, в который подводится вода и который соединен со входами емкости-фильтра 2. Выход емкости-фильтра 2 для СУГ соединен посредством насоса 5 с входом орошения колонны 1 и с линией отбора готового продукта. Кубовая часть колонны 1 соединена через насос 6 с огневым подогревателем 7, соединенным с нижней частью колонны 1.
Сырье - деэтанизированный газовый конденсат (ДЭК) - поступает в колонну 1 стабилизации. В колонне 1 поддерживаются следующие рабочие параметры: давление 1,2-1,7 МПа; температура в кубе колонны 140-160°C; температура вверху колонны 50-60°C. Подвод тепла в колонну 1 осуществляется путем циркуляции с помощью технологического насоса 6 кубового продукта (стабильного газового конденсата - СГК) колонны 1 через змеевики огневого подогревателя 7. Балансовое количество стабильного газового конденсата отводится с куба колонны 1 в товарно-сырьевой склад.
Сжиженные углеводородные газы с верха колонны 1 стабилизации поступают в блок аппаратов 3 воздушного охлаждения с частотным регулированием (АВО). Далее сконденсировавшиеся СУГ с температурой 30-40°C поступают в смесительное устройство 4, куда также поступает технологическая вода, предназначенная для отмывки метанола. Затем смесь воды и СУГ поступает в емкость-фильтр 2, одновременно выполняющую функции и рефлюксной емкости (фиг.2).
Емкость-фильтр 2 (рефлюксная емкость) разделена двумя перегородками 8 на три секции: первые две (по краям) образуют емкости 9, 10 для отмывки метанола; средняя - емкость 11 для фазового разделения СУГ и водометанольного раствора. Смесь СУГ и воды в емкости-фильтре 2 находится в двухфазном состоянии во всех трех секциях.
Смесь СУГ и технологической воды поступает в водную фазу крайних секций - емкостей 9 и 10. Подача СУГ осуществляется через специальные насадки, позволяющие обеспечить наиболее эффективное смешение воды и СУГ, в результате чего из последних отмывается большая часть метанола. Затем и водометанольный раствор, и СУГ поступают через коалесцирующие фильтр-патроны 12, установленные в перегородках 8, в среднюю секцию - емкость 11 для фазового разделения.
Коалесцирующие фильтр-патроны 12 представляют собой металлические каркасы, покрытые стекловолокном, обладающим гидрофильными свойствами. Мелкодиспергированные капли воды, попадая на стекловолокно и скапливаясь, смачивают его поверхность, и уже укрупненные вымываются общим потоком в среднюю секцию емкости-фильтра 2.
В средней секции емкости-фильтра 2 при температуре 30-40°C и давлении 1,1-1,6 МПа происходит четкое разделение поступающей из боковых секций смеси на водную и углеводородную фазы.
Водная фаза, включающая технологическую воду и водометанольный раствор, поступает в сборник 13, из которого отводится в специализированные складские емкости, откуда дозировано отводится на установку выделения.
Углеводородная фаза (СУГ) из средней (по высоте) части емкости-фильтра 2 отводится на прием технологического насоса 5, с нагнетания которого частично возвращается обратно в колонну 1 стабилизации в качестве орошения, а балансовое количество отводится в товарно-сырьевой склад.
Преимущества данной схемы заключаются в ее простоте, обеспечивающей минимизацию капитальных затрат на процесс отмывки водометанольного раствора. Простота технических решений данной схемы позволяет осуществлять их внедрение с использованием существующих аппаратов (рефлюксных емкостей) установок по выделению СУГ.
1. Содержание водометанольного раствора в СУГ без использования блоков экстракционной отмывки и адсорбции гарантировано снижается с 18000 до 5000-6000 ppm.
2. Благодаря совмещению процессов стабилизации газового конденсата и отмывки водометанольного раствора в одном блоке достигается сокращение расхода материалов и снижение капитальные и эксплуатационные затраты.
3. В настоящее время подобные блоки отмывки метанола производительностью по 280 тыс. и 420 тыс. тонн в год расположены на Пуровском ЗПК дочернего общества ОАО «НОВАТЭК».
1. Способ получения сжиженных углеводородных газов, включающий стабилизацию деэтанизированного газового конденсата путем выделения из него углеводородных газов, их охлаждение, смешивание сжиженных углеводородных газов (СУГ) с водой, отмывку метанола и фазовое разделение на СУГ и водометанольный раствор, отличающийся тем, что на стадии отмывки смесь СУГ с водой диспергируют в водной фазе, затем проводят коалесценцию мелкодиспергированных капель водометанольного раствора, после чего осуществляют фазовое разделение.
2. Способ по п.1, отличающийся тем, что смешивание СУГ с водой осуществляют в вихревом режиме.
3. Установка для получения сжиженных углеводородных газов, содержащая последовательно соединенные ректификационную колонну стабилизации газового конденсата, аппарат охлаждения, смесительное устройство, по меньшей мере, одну емкость отмывки метанола и разделительную емкость, отличающееся тем, что по меньшей мере одна емкость отмывки метанола и разделительная емкость выполнены в виде секций емкости-фильтра, разделенного двумя перегородками с размещенными в них коалесцирующими фильтр-патронами с образованием трех секций во внутренней полости упомянутого фильтра, причем две секции представляют собой емкости отмывки метанола, а третья секция - разделительную емкость.
4. Установка по п.3, отличающаяся тем, что смесительное устройство представляет собой устройство вихревого типа.
5. Установка по п.3, отличающаяся тем, что каждый коалесцирующий фильтр-патрон выполнен из гидрофильного стекловолокна.
www.findpatent.ru
Способ деэтанизации нестабильного газового конденсата и установка для его осуществления
Изобретение относится к области газовой промышленности и является усовершенствованным способом промысловой подготовки продукции газоконденсатных залежей. Нестабильный газовый конденсат (НГК), выделенный из газа газоконденсатных месторождений, разделяют на два потока в соотношении 1:3. Первую часть НГК направляют в трехфазный разделитель 2. Из трехфазного разделителя 2 первый поток НГК в качестве орошения подается на верхнюю тарелку колонны деэтанизации 1. Второй поток сначала подается в теплообменник 4, подогревается и поступает в трехфазный разделитель 3. Из трехфазного разделителя 3 второй поток подается в теплообменник 5 и далее поступает в качестве питания в колонну 1. В колонне 1 осуществляется деэтанизация НГК. Кубовая часть колонны деэтанизации 1 последовательно соединена с первым 5 и вторым 4 теплообменниками для нагрева НГК горячим деэтанизированным газовым конденсатом. Основной поток деэтанизированного газового конденсата циркулирует посредством насоса 6 через огневой преградитель 7, обеспечивая необходимый температурный режим в колоне 1. Изобретение позволяет повысить производительность колонн деэтанизации при значительном изменении состава сырья и снизить интенсивность отложения осадка механических примесей и асфальтенов в колонном и теплообменном оборудовании, что увеличивает срок межремонтного пробега оборудования. 2 н. и 1 з.п. ф-лы, 1 ил.
Изобретение относится к области газовой промышленности и является усовершенствованным способом промысловой подготовки продукции газоконденсатных залежей.
Эксплуатация газоконденсатных месторождений (ГКМ) сопровождается увеличением содержания сжиженных углеводородных газов в газовом конденсате. В дальнейшем это становится серьезной проблемой при деэтанизации газового конденсата, так как является причиной перегрузки колонн деэтанизации по паровой фазе.
Еще одной проблемой, возникающей при эксплуатации ГКМ, является наличие в добываемом «сыром» газе, а в последствии и в газовом конденсате, механических примесей и асфальтеновых углеводородов, которые совместно образуют отложения на поверхности теплообменного и колонного оборудования установок деэтанизации газового конденсата, значительно затрудняя его работу. Отложения механических примесей и асфальтенов являются довольно стабильными и могут быть удалены только с использованием целого комплекса мероприятий, включающих предварительную пропарку и последующую механическую чистку. В любом случае для удаления указанных отложений требуется остановка и вскрытие оборудования.
В настоящее время известна установка для подготовки газа (Сбор и промысловая подготовка газа на северных месторождениях России. А.И.Гриценко, В.А.Истомин и др., М.: Недра, 1999 г., стр.372-373), включающая сепараторы, теплообменник и трехфазный разделитель.
Известна также установка для подготовки газа (там же, стр.378-379), включающая входной сепаратор, рекуперативный теплообменник, эжектор, низкотемпературный сепаратор, трехфазные разделители первой и второй ступени и дегазатор.
Известна установка подготовки и переработки углеводородного сырья газоконденсатных месторождений в соответствии с RU 2182035. Установка включает входной сепаратор, рекуперативный газовый теплообменник, эжектор, низкотемпературный сепаратор, трехфазные разделители первой и второй ступеней, дегазатор. Установка дополнительно снабжена последовательно соединенными рекуперативным теплообменником, колонной деэтанизации конденсата, компрессором, аппаратом воздушного охлаждения и рекуперативным газожидкостным теплообменником, вход рекуперативного теплообменника соединен с выходом конденсата из дегазатора, вход в верхнюю часть колонны деэтанизации соединен с выходом конденсата из дегазатора, выход рекуперативного газожидкостного теплообменника соединен с входом низкотемпературного сепаратора. Установка дополнительно снабжена блоком стабилизации деэтанизированного конденсата, блоком первичной переработки стабильного конденсата, блоком каталитической переработки бензиновой фракции, блоком сжижения осушенного газа, блоком каталитической переработки осушенного газа. Установка позволяет повысить качество отделения газообразных углеводородов (метана и этана) от сжижаемых и жидких углеводородов (пропан+высшие).
Наиболее близкими к предложенным являются описанные в патенте RU 2243815 способ промысловой подготовки газоконденсатного флюида и деэтанизации конденсата и установка для его осуществления. Способ включает сепарацию газа с входной и низкотемпературной ступенью сепарации, фазовое разделение конденсата входной и низкотемпературной ступеней сепарации, дегазацию конденсата и деэтанизацию конденсата в отпарной ректификационной колонне. Весь конденсат входной ступени сепарации после предварительной дегазации и подогрева в рекуперативном теплообменнике подают в среднюю часть отпарной ректификационной колонны в качестве питания, конденсат низкотемпературной ступени сепарации разделяют на два потока. Первый подают в верхнюю часть отпарной ректификационной колонны в качестве орошения, второй - в дегазатор. Регулировку технологического режима и состава продуктов деэтанизации в зависимости от выходов и составов конденсата входной и низкотемпературной ступеней сепарации осуществляют изменением объемов потоков. Способ и установка обеспечивают максимальный отбор деэтанизированного конденсата при минимальных потерях с осушенным газом.
Общим недостатком всех вышеприведенных технических решений является снижение производительности колон деэтанизации при значительном изменении состава сырья и отсутствие механизма снижения интенсивности отложения осадка механических примесей и асфальтенов в колонном и теплообменном оборудовании.
Задачей изобретения является устранение указанных недостатков, присущих известным техническим решениям.
Поставленная задача решается способом деэтанизации нестабильного газового конденсата, включающим предварительный нагрев нестабильного газового конденсата (НГК), выделенного из газа газоконденсатных месторождений, разделение НГК на три фазы путем отделения от него водометанольного раствора с механическими примесями и предварительной отдувки газов деэтанизации, разделение потока НГК на две части, подачу одной части НГК на орошение на стадию деэтанизации, нагрев второй части НГК до требуемой температуры перед подачей на питание на стадию деэтанизации и последующую деэтанизацию НГК, в котором согласно изобретению разделение потока НГК на две части осуществляют перед разделением его на три фазы и подогревают вторую часть НГК с обеспечением выделения метана и этана при указанном разделении на три фазы.
При этом подогрев второй части НГК осуществляют с использованием тепла потока деэтанизированного газового конденсата.
Задача также решается установкой для деэтанизации нестабильного газового конденсата, содержащей колонну деэтанизации, два трехфазных разделителя, один из которых соединен с входом питания колонны деэтанизации через первый теплообменник для нагрева НГК, отличающейся тем, что она снабжена вторым теплообменником для нагрева НГК, установленным на входе трехфазного разделителя, соединенного с входом питания колонны, а другой трехфазный разделитель соединен с входом орошения колонны деэтанизации, при этом кубовая часть колонны деэтанизации последовательно соединена с первым и вторым теплообменниками для нагрева НГК горячим деэтанизированным газовым конденсатом.
На фиг.1 приведена схема предлагаемой установки. На схеме обозначены потоки: I - нестабильный газовый конденсат (НГК), II - деэтанизированный газовый конденсат, III - газы деэтанизации, IV - низкоконцетрированный водометанольный раствор (BMP).
Установка для деэтанизации нестабильного газового конденсата (НГК), поступающего с установок сепарации «сырого» газа газоконденсатных месторождений, содержит колонну 1 деэтанизации, вход орошения которой соединен с выходом трехфазного разделителя 2 по НГК. Вход трехфазного разделителя 3 соединен с теплообменником 4, а выход через теплообменник 5 соединен с входом питания колонны 1 деэтанизации. Кубовая часть колонны 1 деэтанизации последовательно соединена с теплообменниками 5 и 4 для подачи в них горячего деэтанизированного газового конденсата. К кубовой части колонны 1 подсоединен циркуляционный контур, включающий насос 6 и подогреватель 7, в частности, огневой подогреватель.
Способ деэтанизации НГК осуществляется следующим образом.
Сырье, нестабильный газовый конденсат с установок сепарации «сырого» газа газоконденсатных месторождений, поступает в цех деэтанизации конденсата с давлением 2,5-3,5 МПа и температурой «минус» 3 - «минус» 6°С. На входе в цех поток нестабильного газового конденсата разделяется на два потока в соотношении 1:3.
Первый поток с меньшим расходом направляется в трехфазный разделитель 2 - буферную емкость орошения колонны 1 деэтанизации, в которой из него извлекается незначительное количество низкоконцентрированного водометанольного раствора (BMP) с механическими примесями и газов деэтанизации. BMP и примеси направляются для утилизации на горизонтальную факельную установку (ГФУ) (не показана). Газы деэтанизации после компримирования возвращаются на установку сепарации «сырого» газа. Из трехфазного разделителя 2 первый поток НГК в качестве орошения подается на верхнюю тарелку колонны 1 деэтанизации.
Второй поток сначала подается в кожухотрубный или пластинчатый теплообменник 4, подогревается и поступает в трехфазный разделитель 3 - буферную емкость питания колоны 1 деэтанизации. В трехфазном разделителе 3 при давлении 2,3-3,3 МПа и температуре 20-30°С происходит отделение большей части низкоконцентрированного BMP с механическими примесями и газов деэтанизации, которые, как и в случае трехфазного разделителя 2, направляются на ГФУ и установку сепарации «сырого» газа соответственно. Количество сдувок из разделителя 3 регулируется клапаном на линии сдувок и обеспечивается поддержанием необходимой температуры после теплообменника 4. Из трехфазного разделителя 3 второй поток частично деэтанизированного газового конденсата подается для нагрева до температуры 60-70°С в теплообменник 5 и далее поступает в качестве питания в колонну деэтанизации.
В колонне 1 деэтанизации от НГК отгоняется весь оставшийся газ деэтанизации, который смешивается с соответствующими потоками из разделителей 2 и 3 и после компримирования подается на установку сепарации «сырого» газа.
Основной поток кубового продукта (деэтанизированный газовый конденсат) циркулирует посредством технологического насоса 6 через огневой подогреватель 7, тем самым обеспечивая необходимый температурный режим в колонне 1 деэтанизации.
Балансовое количество деэтанизированного газового конденсата из куба колонны 1 направляется в теплообменники 4 и 5, где охлаждается потоком НГК и далее отводится с установки на дальнейшую переработку.
Данная схема благодаря дополнительному подогреву основного потока НГК в теплообменнике 4 позволяет:
1) выделять значительное количество газов деэтанизации из потока НГК в трехфазном разделителе 3; таким образом, снижается паровая нагрузка на колонну 1 деэтанизации, а следовательно, уменьшается негативное влияние на технологический режим в колонне 1 в результате изменения (облегчения) состава исходного сырья;
2) благодаря снижению вязкости подогретого НГК извлекать значительное количество механических примесей, растворенных в BMP, из НГК в разделителе 3, что снижает прочность асфальтеновых отложений; в результате, как минимум в два раза увеличивается срок межремонтного пробега колонного и теплообменного оборудования.
1. Способ деэтанизации нестабильного газового конденсата, включающий предварительный нагрев нестабильного газового конденсата (НГК), выделенного из газа газоконденсатных месторождений, разделение НГК на три фазы путем отделения от него водометанольного раствора с механическими примесями и предварительной отдувки газов деэтанизации, разделение потока НГК на две части, подачу одной части НГК на орошение на стадию деэтанизации, нагрев второй части НГК до требуемой температуры перед подачей на питание на стадию деэтанизации и последующую деэтанизацию НГК, отличающийся тем, что разделение потока НГК на две части осуществляют перед разделением его на три фазы и подогревают вторую часть НГК с обеспечением выделения метана и этана при указанном разделении на три фазы.
2. Способ по п.1, отличающийся тем, что подогрев второй части НГК осуществляют с использованием тепла потока деэтанизированного газового конденсата.
3. Установка для деэтанизации нестабильного газового конденсата, содержащая колонну деэтанизации, два трехфазных разделителя, один из которых соединен с входом питания колонны деэтанизации через первый теплообменник для нагрева НГК, отличающаяся тем, что снабжена вторым теплообменником для нагрева НГК, установленным на входе трехфазного разделителя, соединенного с входом питания колонны, а другой трехфазный разделитель соединен со входом орошения колонны деэтанизации, при этом кубовая часть колонны деэтанизации последовательно соединена с первым и вторым теплообменниками для нагрева НГК горячим деэтанизированным газовым конденсатом.
www.findpatent.ru
способ получения сжиженных углеводородных газов и установка для его осуществления - патент РФ 2463534
Изобретение относится к технике получения сжиженных углеводородных газов и их очистки от метанола и может быть использовано в газовой, нефтяной, нефтеперерабатывающей, нефтехимической и химической отраслях промышленности. Способ получения сжиженных углеводородных газов включает стабилизацию деэтанизированного газового конденсата путем выделения из него углеводородных газов, их охлаждение, смешивание сжиженных углеводородных газов (СУГ) с водой, отмывки метанола и фазовое разделение на СУГ и водометанольный раствор. При этом на стадии отмывки смесь СУГ с водой диспергируют в водной фазе, затем проводят коалесценцию мелкодиспергированных капель водометанольного раствора, после чего осуществляют фазовое разделение. Установка для получения сжиженных углеводородных газов содержит последовательно соединенные ректификационную колонну стабилизации газового конденсата, аппарат охлаждения, смесительное устройство, по меньшей мере, одну емкость отмывки метанола и разделительную емкость. При этом, по меньшей мере, одна емкость отмывки метанола и разделительная емкость выполнены в виде секций емкости-фильтра, разделенного двумя перегородками с размещенными в них коалесцирующими фильтр-патронами с образованием трех секций во внутренней полости упомянутого фильтра, причем две секции представляют собой емкости отмывки метанола, а третья секция - разделительную емкость. Использование изобретения позволит минимизировать капитальные и текущие затраты на установку за счет ее упрощения. 2 н. и 3 з.п. ф-лы, 3 ил.
Рисунки к патенту РФ 2463534
Изобретение относится к технике и технологии получения сжиженных углеводородных газов, к которым относятся смесь пропана и бутана технических, пропан технический, бутан технический (далее СУГ), и их очистки от метанола и может быть использовано в газовой, нефтяной, нефтеперерабатывающей, нефтехимической и химической отраслях промышленности.
Основная доля получаемых отечественными компаниями СУГ производится из газового конденсата, выделяемого на установках комплексной подготовки газа (УКПГ), работающих по технологии низкотемпературной сепарации, где метанол используется в качестве ингибитора гидратообразования. Большая часть метанола отводится с УКПГ в виде водометанольной смеси после трехфазных разделителей «углеводороды - метанольная вода - газ выветривания». Однако в результате растворимости метанола в газовом конденсате остаточное содержание метанола в продуктах дальнейшей переработки газового конденсата может изменяться в достаточно широком диапазоне.
Данная проблема усугубляется тем, что в процессе переработки газового конденсата с получением стабильного конденсата (СК) и товарных сжиженных газов (смеси пропана и бутана технических) практически весь водометанольный раствор переходит в состав сжиженных газов. Это приводит к существенному повышению концентрации растворимого метанола в товарных сжиженных газах до 18000 ppm. Co временем значительная часть водометанольного раствора выделяется из СУГ в виде отдельной фазы. Частично отделение происходит на товарных складах производителей СУГ, где водометанольный раствор «подрезается» и отводится в дренажную систему. Однако значительная часть BMP выделяется уже после отгрузки СУГ потребителям. В этом случае потребители вполне обосновано предъявляют претензии производителям и требуют возмещения понесенных убытков.
В настоящее время большинство производителей СУГ пытаются решать данную проблему путем применения метода экстракции метанола водой.
Для выполнения данной задачи чаще всего используют огромные резервуары-отстойники, насосное оборудование подачи СУГ и воды. Эффективность данного способа очистки СУГ крайне низкая и, как правило, не приводит к желаемым результатам. Более того, в данном случае возникает необходимость в строительстве дополнительно узла подготовки химочищенной воды и утилизации большого количества сточных вод, что при отсутствии гарантий выполнения контрактных обязательств перед заказчиком накладывает негативный отпечаток на рентабельность производства в целом.
Известен способ (патент РФ № 2286194) очистки жидких углеводородов от метанола, находящихся в виде эмульсии, включающий нагрев эмульсии, разделение путем сепарации нагретой эмульсии на жидкие углеводороды и водный раствор метанола и последующий их раздельный отвод.
Недостатками описанного способа являются большие энергетические затраты на нагрев эмульсии и низкая эффективность процесса сепарации из-за плохого осаждения водного раствора метанола в жидких углеводородах, легкие компоненты которых при нагреве испаряются и (или) кипят.
Наиболее близким является способ (RU 2289608, опубл. 20.12.2006) очистки жидких углеводородов от метанола, включающий стабилизацию жидкого углеводородного сырья путем выделения из него легкой фракции - сжиженных углеводородных газов (СУГ), экстракцию метанола из СУГ, сепарацию водного раствора метанола и СУГ и адсорбционную очистку СУГ.
Установка для реализации данного способа содержит ректификационную колонну для разделения жидкого углеводородного сырья, например нестабильного газового конденсата (НГК), на легкую фракцию - СУГ и тяжелую фракцию, например стабильный газовый конденсат (СГК), соединенную через охлаждающее устройство с экстракционной колонной для отмывки метанола от СУГ, соединенное с разделителем, из которого отделенный водометанольный раствор подается в емкость, а СУГ - в блок адсорбционной очистки.
Однако данный способ ввиду своей многостадийности является достаточно сложным и дорогостоящим, подходящим только для случаев, когда предъявляются очень жесткие требования по содержанию метанола в СУГ (не более 50 ppm).
Задачей предлагаемого изобретения является минимизация капитальных и текущих затрат на установку по получению СУГ с содержанием водометанольного раствора не более 6000 ppm за счет упрощения схемы установки путем исключения блока адсорбционной очистки и использования рефлюксной емкости вместо блока отмывки, включающего несколько аппаратов.
Поставленная задача решается способом получения сжиженных углеводородных газов, включающим стабилизацию деэтанизированного газового конденсата путем выделения из него углеводородных газов, их охлаждение, смешивание сжиженных углеводородных газов (СУГ) с водой, отмывку метанола и фазовое разделение на СУГ и водометанольный раствор, согласно которому на стадии отмывки смесь СУГ с водой диспергируют в водной фазе, затем проводят коалесценцию мелкодиспергированных капель водометанольного раствора, после чего осуществляют фазовое разделение.
При этом смешивание СУГ с водой осуществляют предпочтительно в вихревом режиме.
Задача также решается установкой для получения сжиженных углеводородных газов, содержащей последовательно соединенные ректификационную колонну стабилизации газового конденсата, аппарат охлаждения, смесительное устройство, по меньшей мере, одну емкость отмывки метанола и разделительную емкость, при этом, по меньшей мере, одна емкость отмывки метанола и разделительная емкость выполнены в виде секций емкости-фильтра, разделенного двумя перегородками с размещенными в них коалесцирующими фильтр-патронами с образованием трех секций во внутренней полости упомянутого фильтра, причем две секции представляют собой емкости отмывки метанола, а третья секция - разделительную емкость.
Кроме того, смесительное устройство предпочтительно представляет собой устройство вихревого типа.
При этом каждый коалесцирующий фильтр-патрон выполнен из гидрофильного стекловолокна.
На фиг.1 приведена технологическая схема установки для получения СУГ.
На фиг.2 приведена схема емкости-фильтра.
На фиг.3 - сечение А-А на фиг.2.
Установка для получения сжиженных углеводородных газов включает ректификационную колонну 1 стабилизации газового конденсата и емкость-фильтр 2 для отмывки метанола и фазового разделения водной и углеводородной фаз. Выход колонны 1 для легких фракций соединен с аппаратом 3 воздушного охлаждения, который в свою очередь соединен с смесительным устройством 4 вихревого типа, в который подводится вода и который соединен со входами емкости-фильтра 2. Выход емкости-фильтра 2 для СУГ соединен посредством насоса 5 с входом орошения колонны 1 и с линией отбора готового продукта. Кубовая часть колонны 1 соединена через насос 6 с огневым подогревателем 7, соединенным с нижней частью колонны 1.
Сырье - деэтанизированный газовый конденсат (ДЭК) - поступает в колонну 1 стабилизации. В колонне 1 поддерживаются следующие рабочие параметры: давление 1,2-1,7 МПа; температура в кубе колонны 140-160°C; температура вверху колонны 50-60°C. Подвод тепла в колонну 1 осуществляется путем циркуляции с помощью технологического насоса 6 кубового продукта (стабильного газового конденсата - СГК) колонны 1 через змеевики огневого подогревателя 7. Балансовое количество стабильного газового конденсата отводится с куба колонны 1 в товарно-сырьевой склад.
Сжиженные углеводородные газы с верха колонны 1 стабилизации поступают в блок аппаратов 3 воздушного охлаждения с частотным регулированием (АВО). Далее сконденсировавшиеся СУГ с температурой 30-40°C поступают в смесительное устройство 4, куда также поступает технологическая вода, предназначенная для отмывки метанола. Затем смесь воды и СУГ поступает в емкость-фильтр 2, одновременно выполняющую функции и рефлюксной емкости (фиг.2).
Емкость-фильтр 2 (рефлюксная емкость) разделена двумя перегородками 8 на три секции: первые две (по краям) образуют емкости 9, 10 для отмывки метанола; средняя - емкость 11 для фазового разделения СУГ и водометанольного раствора. Смесь СУГ и воды в емкости-фильтре 2 находится в двухфазном состоянии во всех трех секциях.
Смесь СУГ и технологической воды поступает в водную фазу крайних секций - емкостей 9 и 10. Подача СУГ осуществляется через специальные насадки, позволяющие обеспечить наиболее эффективное смешение воды и СУГ, в результате чего из последних отмывается большая часть метанола. Затем и водометанольный раствор, и СУГ поступают через коалесцирующие фильтр-патроны 12, установленные в перегородках 8, в среднюю секцию - емкость 11 для фазового разделения.
Коалесцирующие фильтр-патроны 12 представляют собой металлические каркасы, покрытые стекловолокном, обладающим гидрофильными свойствами. Мелкодиспергированные капли воды, попадая на стекловолокно и скапливаясь, смачивают его поверхность, и уже укрупненные вымываются общим потоком в среднюю секцию емкости-фильтра 2.
В средней секции емкости-фильтра 2 при температуре 30-40°C и давлении 1,1-1,6 МПа происходит четкое разделение поступающей из боковых секций смеси на водную и углеводородную фазы.
Водная фаза, включающая технологическую воду и водометанольный раствор, поступает в сборник 13, из которого отводится в специализированные складские емкости, откуда дозировано отводится на установку выделения.
Углеводородная фаза (СУГ) из средней (по высоте) части емкости-фильтра 2 отводится на прием технологического насоса 5, с нагнетания которого частично возвращается обратно в колонну 1 стабилизации в качестве орошения, а балансовое количество отводится в товарно-сырьевой склад.
Преимущества данной схемы заключаются в ее простоте, обеспечивающей минимизацию капитальных затрат на процесс отмывки водометанольного раствора. Простота технических решений данной схемы позволяет осуществлять их внедрение с использованием существующих аппаратов (рефлюксных емкостей) установок по выделению СУГ.
1. Содержание водометанольного раствора в СУГ без использования блоков экстракционной отмывки и адсорбции гарантировано снижается с 18000 до 5000-6000 ppm.
2. Благодаря совмещению процессов стабилизации газового конденсата и отмывки водометанольного раствора в одном блоке достигается сокращение расхода материалов и снижение капитальные и эксплуатационные затраты.
3. В настоящее время подобные блоки отмывки метанола производительностью по 280 тыс. и 420 тыс. тонн в год расположены на Пуровском ЗПК дочернего общества ОАО «НОВАТЭК».
ФОРМУЛА ИЗОБРЕТЕНИЯ
1. Способ получения сжиженных углеводородных газов, включающий стабилизацию деэтанизированного газового конденсата путем выделения из него углеводородных газов, их охлаждение, смешивание сжиженных углеводородных газов (СУГ) с водой, отмывку метанола и фазовое разделение на СУГ и водометанольный раствор, отличающийся тем, что на стадии отмывки смесь СУГ с водой диспергируют в водной фазе, затем проводят коалесценцию мелкодиспергированных капель водометанольного раствора, после чего осуществляют фазовое разделение.
2. Способ по п.1, отличающийся тем, что смешивание СУГ с водой осуществляют в вихревом режиме.
3. Установка для получения сжиженных углеводородных газов, содержащая последовательно соединенные ректификационную колонну стабилизации газового конденсата, аппарат охлаждения, смесительное устройство, по меньшей мере, одну емкость отмывки метанола и разделительную емкость, отличающееся тем, что по меньшей мере одна емкость отмывки метанола и разделительная емкость выполнены в виде секций емкости-фильтра, разделенного двумя перегородками с размещенными в них коалесцирующими фильтр-патронами с образованием трех секций во внутренней полости упомянутого фильтра, причем две секции представляют собой емкости отмывки метанола, а третья секция - разделительную емкость.
4. Установка по п.3, отличающаяся тем, что смесительное устройство представляет собой устройство вихревого типа.
5. Установка по п.3, отличающаяся тем, что каждый коалесцирующий фильтр-патрон выполнен из гидрофильного стекловолокна.
www.freepatent.ru
Двухвальный газокомпрессорный агрегат для дожимных компрессорных станций
Изобретение относится к отрасли нефтяного и газового машиностроения, в частности к газокомпрессорным агрегатам, применяемым на дожимных компрессорных станциях для компримирования углеводородных газов. Газокомпрессорный агрегат содержит газотурбинный двигатель, связанный с ним мультипликатор, имеющий два вала отбора мощности, и две ступени сжатия в виде соединенных технологическим контуром компрессора низкого давления и компрессора высокого давления, каждый из которых связан с соответствующим валом отбора мощности. Техническим результатом изобретения является улучшение вибрационных характеристик и повышение эффективности работы агрегата, упрощение технологической схемы и исключение необходимости применения дополнительного оборудования, обеспечение симметричного распределения нагрузки на мультипликатор. 2 з.п. ф-лы, 1 ил.
Изобретение относится к отрасли нефтяного и газового машиностроения, в частности к газокомпрессорным агрегатам, применяемым на дожимных компрессорных станциях для компримирования углеводородных газов для дальнейшей транспортировки по магистральным трубопроводам или использования в технологических процессах подготовки и переработки газа.
На дожимных компрессорных станциях для достижения высоких степеней сжатия (более 4,0) применяется двухступенчатое компримирование с промежуточным охлаждением газа. Существующие технологические схемы дожимных компрессорных станций предполагают следующие варианты компоновки газоперекачивающих агрегатов с центробежными компрессорами:
- две автономных дожимных компрессорных станции первой и второй ступеней сжатия с газокомпрессорными агрегатами, в состав которых входят одноступенчатые однокорпусные центробежные компрессоры с прямым приводом от газотурбинного двигателя;
- дожимная компрессорная станция, в состав которой входят газокомпрессорные агрегаты с двухступенчатыми двухкорпусными компрессорами с промежуточным охлаждением, расположенными на одном валу, привод которых осуществляется от приводного газотурбинного двигателя через промежуточный повышающий редуктор (мультипликатор), имеющий один вал отбора мощности;
- дожимная компрессорная станция, в состав которой входят газокомпрессорные агрегаты с двухсекционными однокорпусными центробежными компрессорами с промежуточным охлаждением, привод которых осуществляется от приводного газотурбинного двигателя через промежуточный повышающий редуктор (мультипликатор), имеющий один вал отбора мощности.
Наиболее близким решением к предложенному изобретению является блочно-комплектная турбокомпрессорная установка для транспортировки углеводородного газа, состоящая из двухкорпусного центробежного компрессора с расположением корпусов компрессоров низкого и высокого давления на одном валу, газотурбинного привода с мультипликатором, технологического контура, оснащенного запорной и регулирующей арматурой, а также датчиками системы автоматизированного управления установкой, притом технологический контур имеет линейную компоновку, а ступени сжатия двухкорпусного центробежного компрессора оснащены аппаратами воздушного охлаждения и сепараторами (см. Патент RU №2464448, опубликован 20.10.2012).
Недостатками вышеуказанных схем и наиболее близкого решения являются:
- сложная технологическая схема;
- длинная линия вала центробежного компрессора;
- невозможность применения высокотехнологичного вертикального разъема корпуса для компрессора первой ступени компримирования;
- невысокая эффективность агрегата, вызванная невозможностью применения компрессоров первой и второй ступеней сжатия с различными номинальными оборотами;
- сложность проведения технического обслуживания в процессе эксплуатации и во время проведения капитального ремонта;
- наличие взаимного механического и газодинамического влияния роторов компрессоров первой и второй ступеней компримирования;
- технологические ограничения по линейным размерам и напорным характеристикам в случае применения однокорпусных компрессоров;
- сложность унификации газокомпрессорных агрегатов первой и второй ступеней компримирования;
- низкая вибрационная устойчивость.
Техническим результатом изобретения является улучшение вибрационных характеристик и повышение эффективности работы агрегата за счет возможности применения компрессоров первой и второй ступеней сжатия с различными номинальными оборотами при одновременном исключении взаимного влияния роторов компрессоров, упрощение технологической схемы, обеспечение симметричного распределения нагрузки на мультипликатор.
Технический результат изобретения достигается за счет того, что газокомпрессорный агрегат содержит газотурбинный двигатель, связанный с ним мультипликатор, имеющий два вала отбора мощности, и две ступени сжатия в виде соединенных технологическим контуром компрессора низкого давления и компрессора высокого давления, каждый из которых связан с соответствующим валом отбора мощности.
Кроме того, валы отбора мощности мультипликатора расположены параллельно друг другу.
Кроме того, каждый из указанных компрессоров имеет корпус с вертикальным разъемом.
Изобретение поясняется чертежом, на котором схематично изображен двухвальный газокомпрессорный агрегат.
Двухвальный газокомпрессорный агрегат для дожимных компрессорных станций представляет собой газотурбинную установку, которая содержит приводной газотурбинный двигатель 1, с которым связан мультипликатор 2 (повышающий редуктор), имеющий два параллельно расположенных друг к другу вала отбора мощности 3 и 4. Установка также содержит двухкорпусной центробежный компрессор, включающий две ступени сжатия в виде компрессора 5 низкого давления и компрессора 6 высокого давления, соединенных технологическим контуром 9. Центробежный компрессор имеет аппарат 7 промежуточного воздушного охлаждения, расположенный в составе технологического контура 9 между двумя ступенями сжатия. Центробежные компрессоры 5 и 6 имеют корпусы с высокотехнологичным вертикальным разъемом типа «баррель» (не показаны) и расположены на силовой раме (не показана) параллельно друг другу. Компрессор 5 низкого давления связан с ведомым валом 3 мультипликатора 2, а компрессор 6 высокого давления связан с ведомым валом 4 мультипликатора 2, таким образом, компрессоры 5, 6 имеют независимые друг от друга приводы, каждый из которых имеет свои обороты в процессе эксплуатации.
В состав газокомпрессорного агрегата также входит технологическое укрытие 8 с технологическим контуром 9 (с инженерными системами обеспечения), оснащенным трубопроводами, запорной и регулирующей арматурой, а также датчиками контроля.
Конструкция корпусов центробежного компрессора предусматривает возможность установки сменных проточных частей на большее отношение давлений, что позволяет обеспечить работу газокомпрессорного агрегата в широком диапазоне производительности и входных давлений.
Для передачи крутящего момента от вала силовой турбины приводного газотурбинного двигателя 1 к валам 3, 4 компрессоров низкого и высокого давлений 5, 6 служит мультипликатор 2 с параллельным расположением двух валов отбора мощности 3, 4. Силовая турбина (выходной вал) приводного газотурбинного двигателя 1 соединена с ведущим валом мультипликатора 2 посредством упругой «сухой» муфты (не показана), позволяющей компенсировать неточность монтажа соединяемых валов, а также тепловые перемещения за счет упругих элементов. Ведомые валы 3, 4 мультипликатора 2 соединены через муфту (не показана) с валами роторов компрессоров низкого и высокого давления 5, 6.
Компримируемый газ поступает на вход компрессора 5 низкого давления, далее после охлаждения в промежуточном газоохладителе 7 на вход компрессора 6 высокого давления, после чего подается в нагнетательный трубопровод.
В случае применения газокомпрессорного агрегата в технологической схеме с промежуточной низкотемпературной сепарацией, компрессор 5 низкого давления используется для компримирования попутного нефтяного газа, а компрессор 6 высокого давления - сухого отбензиненного газа.
Таким образом, благодаря вышеописанному выполнению газокомпрессорного агрегата с двумя валами отбора мощности обеспечивается возможность использования в качестве ступеней низкого и высокого давления компрессоров с различными номинальными оборотами; уменьшается длина вала компрессора вдвое; улучшаются вибрационные характеристики как компрессоров, так и всего агрегата в целом; обеспечивается симметричное распределение нагрузки на ведущую шестерню мультипликатора за счет наличия двух параллельных валов отбора мощности; исключается взаимное влияние роторов компрессоров низкого и высокого давления, особенно в диапазоне нештатных режимов; в случае применения в составе двухступенчатой дожимной компрессорной станции с промежуточным циклом низкотемпературной сепарации, обеспечивается возможность унификации агрегатов первой и второй ступеней путем использования одного приводного газотурбинного двигателя как для привода компрессора низкого давления (первой ступени) для сжатия попутного нефтяного газа, так и компрессора высокого давления (второй ступени) - для сжатия сухого отбензиненного газа; благодаря наличию высокотехнологичного корпуса с вертикальным разъемом значительно упрощается как его техническое обслуживание в процессе эксплуатации, так и проведение капитального ремонта компрессоров.
При необходимости достижения высоких степеней сжатия агрегат позволяет применять на обеих ступенях компримирования однокорпусные двухсекционные центробежные компрессоры с промежуточным охлаждением.
1. Газокомпрессорный агрегат, содержащий газотурбинный двигатель, связанный с ним мультипликатор, имеющий два вала отбора мощности, и две ступени сжатия в виде соединенных технологическим контуром компрессора низкого давления и компрессора высокого давления, каждый из которых связан с соответствующим валом отбора мощности.
2. Агрегат по п. 1, отличающийся тем, что валы отбора мощности мультипликатора расположены параллельно друг другу.
3. Агрегат по п. 1, отличающийся тем, что каждый из указанных компрессоров имеет корпус с вертикальным разъемом.
www.findpatent.ru
Способ переработки углеводородных газов нефтяных или газоконденсатных месторождений и установка для его осуществления
Изобретение относится к нефтяной и газовой промышленности, а именно к технологии переработки сжиженных углеводородных газов (СУГ) в смесь ароматических углеводородов (ароматический концентрат) путем ее интеграции в объекты нефтяного или газоконденсатного месторождения. Технический результат изобретения заключается в обеспечении возможности переработки СУГ в процессе промысловой подготовки попутных нефтяных газов (ПНГ) и «сырого газа». Способ переработки углеводородных газов нефтяных и газоконденсатных месторождений включает промысловую подготовку попутного нефтяного газа (ПНГ) или «сырого газа» с получением товарного осушенного газа и газового конденсата, подачу конденсата на стадию стабилизации с выделением из упомянутого газового конденсата сжиженных углеводородных газов (СУГ), а также дополнительно очистку СУГ, реакционное превращение СУГ в смесь ароматических углеводородов на стадии платформинга, разделение продуктов реакции платформинга на водород, углеводородный газ и жидкие продукты реакции, после чего подают углеводородный газ в поток ПНГ или «сырого газа», поступающего на промысловую подготовку, а из жидких продуктов реакции выделяют ароматические углеводороды, по меньшей мере часть которых подают в магистральный нефтепровод в составе товарной нефти. Описана установка для осуществления способа. 2 н. и 7 з.п. ф-лы, 1 ил.
Изобретение относится к нефтяной и газовой промышленности, а именно к технологии переработки сжиженных углеводородных газов (СУГ) в смесь ароматических углеводородов (ароматический концентрат) путем ее интеграции в объекты нефтяного или газоконденсатного месторождения.
В среднесрочной перспективе добыча природного газа будет сопровождаться увеличением доли добываемого газового конденсата. В первую очередь это связано с переходом к разработке более глубоких валанжинских и ачимовских горизонтов, содержащих преимущественно газ, насыщенный конденсатом.
Первый этап переработки газового конденсата - его стабилизация сопровождается получением сжиженных углеводородных газов (СУГ), выход которых в среднем составляет около 30 мас.%, от первоначального объема газового конденсата. Таким образом, рост добываемых объемов газового конденсата приведет к увеличению производства СУГ.
При этом значительные проблемы возникнут у производителей СУГ, производственные мощности которых расположены в районах Крайнего Севера, с неразвитой транспортной инфраструктурой. В данном случае потребуется строительство трубопроводов, складов и перевалочных комплексов для транспортировки СУГ. Сооружение подобных трубопроводов и комплексов потребует огромных прямых капитальных вложений и косвенных расходов, связанных с реализацией мероприятий по защите окружающей среды, предотвращению и минимизации возможного воздействия на экосистему. Если к этому добавить транспортные расходы на найм танкеров ледового класса либо на оплату услуг железной дороги, то говорить о какой-либо окупаемости проекта просто не приходится. В таком случае наиболее предпочтительным оказывается вариант переработки СУГ непосредственно на промысле.
Известен способ промысловой подготовки газоконденсатного флюида и деэтанизации конденсата, включающий газ со входной и низкотемпературной ступенью сепарации, фазовое разделение конденсата входной и низкотемпературной ступеней сепарации, дегазацию конденсата и деэтанизацию конденсата в отпарной ректификационной колонне. Весь конденсат входной ступени сепарации после предварительной дегазации и подогрева в рекуперативном теплообменнике подают в среднюю часть отпарной ректификационной колонны в качестве питания, конденсат низкотемпературной ступени сепарации разделяют на два потока. Первый подают в верхнюю часть отпарной ректификационной колонны в качестве орошения, второй - в дегазатор. Установка для реализации способа содержит входную ступень сепарации, рекуперативный газовый теплообменник, эжектор, низкотемпературную ступень сепарации, трехфазный разделитель конденсата входной ступени сепарации, трехфазный разделитель конденсата низкотемпературной ступени сепарации, дегазатор, рекуперативный теплообменник, отпарную ректификационную колонну для деэтанизации конденсата, компрессор газа деэтанизации, аппарат воздушного охлаждения и рекуперативный газожидкостной теплообменник (RU 2243815 С1, опубликовано 10.01.2005). Полученный деэтанизированный конденсат (СУГ) отводят с установки в качестве товарного продукта для последующей переработки. Известные способ и установка не предусматривают переработку СУГ непосредственно на промысле.
Задачей изобретения является создание способа и установки для совместной переработки СУГ и промысловой подготовки продукции нефтяных или газоконденсатных месторождений с получением продуктов, транспортируемых совместно с товарной нефтью и товарным газом.
Технический результат изобретения заключается в обеспечении возможности переработки СУГ в процессе промысловой подготовки попутных нефтяных газов (ПНГ) и «сырого» газа.
Технический результат достигается способом переработки углеводородных газов нефтяных и газоконденсатных месторождений, включающим промысловую подготовку попутного нефтяного газа (ПНГ) или «сырого газа» с получением товарного осушенного газа и газового конденсата, подачу конденсата на стадию стабилизации с выделением из упомянутого газового конденсата сжиженных углеводородных газов (СУГ), а также дополнительно очистку СУГ, реакционное превращение СУГ в смесь ароматических углеводородов на стадии платформинга, разделение продуктов реакции платформинга на водород, углеводородный газ и жидкие продукты реакции, после чего подают углеводородный газ в поток ПНГ или «сырого газа», поступающего на промысловую подготовку, а из жидких продуктов реакции выделяют ароматические углеводороды, по меньшей мере часть которых подают в магистральный нефтепровод в составе товарной нефти.
Выделение из жидких продуктов реакции ароматических углеводородов может быть осуществлено путем разделения жидких продуктов реакции на непрореагировавшие СУГ, которые подают на вход стадии платформинга, и смесь ароматических углеводородов, по меньшей мере часть которой подают в магистральный нефтепровод в составе товарной нефти.
Также выделение из жидких продуктов реакции ароматических углеводородов может быть осуществлено путем подачи жидких продуктов реакции на вход стадии стабилизации для отделения непрореагировавших СУГ, а выходящую из него смесь С5+ и ароматических углеводородов, по меньшей мере часть которой подают в магистральный нефтепровод в составе товарной нефти.
Для достижения технического результата после разделения продуктов реакции водород целесообразно подать на стадию платформинга.
Кроме того, целесообразно на стадии стабилизации использовать блок колонны стабилизации газового конденсата установки промысловой подготовки ПНГ или «сырого газа».
Кроме того, очистку СУГ осуществляют путем экстракционной отмывки и последующей адсорбционной осушки, а образующийся газ деэтанизации подают в поток ПНГ или «сырого газа», поступающего на промысловую подготовку.
Технический результат также достигается тем, что установка для переработки углеводородных газов нефтяных и газоконденсатных месторождений содержит трубопровод подачи попутного нефтяного газа (ПНГ) или «сырого» газа и связанные с ним и между собой системой трубопроводов аппараты установки промысловой подготовки ПНГ и «сырого» газа компрессорную станцию, а именно установку низкотемпературной сепарации, блок адсорбционной очистки, выход которого соединен с трубопроводом отвода товарного осушенного газа, блок колонны стабилизации газового конденсата и установку очистки сжиженных углеводородных газов (СУГ), а также соединенный с выходом СУГ установки очистки реакторный блок платформинга и соединенный с выходом реакторного блока блок разделения продуктов реакции, выход жидких продуктов которого соединен со входом блока колонны стабилизации, а выход углеводородного газа которого соединен с трубопроводом подачи ПНГ или «сырого» газа, а второй выход блока колонны стабилизации соединен с трубопроводом отвода смеси углеводородов С5+ и ароматических углеводородов в магистральный нефтепровод.
Возможно выполнение блока разделения с возможностью разделения жидких продуктов реакции на непрореагировавшие СУГ и смесь ароматических углеводородов, при этом его указанный выход жидких продуктов, соединенный с входом блока колонны стабилизации, является выходом непрореагировавших СУГ, а его выход смеси ароматических углеводородов соединен с трубопроводом отвода смеси углеводородов С5+ и ароматических углеводородов в магистральный нефтепровод.
Выход водорода блока разделения соединен с входом реакторного блока платформинга.
Для достижения технического результата одним из самых предпочтительных процессов является платформинг, который позволяет за один проход получить:
- концентрат ароматических углеводородов (бензол, толуол и ксилолы) - выход 60 мас.%, направляемый в товарную нефть или газовый конденсат;
- легкие газы (метан и этан) - выход 33 мас.%, которые можно направить в сеть магистральных газопроводов.
Изобретение позволяет создать комплексную безотходную промысловую подготовку и переработку продукции газоконденсатных залежей.
Принципиальная схема предложенной установки представлена на фиг.1.
Установка для переработки углеводородных газов нефтяных и газоконденсатных месторождений содержит трубопровод подачи попутного нефтяного газа (ПНГ) или «сырого» газа и связанные с ним и между собой системой трубопроводов аппараты установки промысловой подготовки ПНГ и «сырого» газа, а именно дожимную компрессорную станцию 1, установку 2 низкотемпературной сепарации (УНТС), блок 3 адсорбционной очистки, выход которого соединен с трубопроводом отвода товарного осушенного газа, блок 4 колонны стабилизации газового конденсата и установку 5 очистки сжиженных углеводородных газов (СУГ).
С выходом СУГ установки 5 очистки соединен реакторный блок 6 платформинга, с выходом которого соединен блок 7 разделения продуктов реакции, выход углеводородного газа которого соединен с трубопроводом подачи ПНГ или «сырого» газа.
Выход жидких продуктов реакции блока 7 разделения соединен со входом в блок 4 колонны стабилизации, второй выход которого соединен с трубопроводом отвода смеси углеводородов С5+ и ароматических углеводородов в магистральный нефтепровод, а выход водорода блока 7 разделения соединен с входом реакторного блока 6 платформинга.
Возможен другой вариант соединения выходов блока 7 разделения, не показанный на схеме. Блок 7 может осуществлять функцию разделения жидких продуктов реакции на непрореагировавшие СУГ и смесь ароматических водородов. Тогда выход СУГ блока 7 соединен с входом блока 4 колонны стабилизации, выход смеси ароматических углеводородов - с трубопроводом отвода ароматических углеводородов в магистральный нефтепровод. При этом выход углеводородов С5+ блока 4 колонны стабилизации также соединен с трубопроводом отвода в магистральный нефтепровод.
Установка 5 очистки сжиженных углеводородных газов включает блок экстракционной отмывки и адсорбционной осушки.
Блок 7 разделения продуктов реакции платформинга состоит из нескольких сепараторов и мембранной установки.
Способ переработки углеводородных газов нефтяных и газоконденсатных месторождений осуществляется следующим образом.
ПНГ или «сырой» газ дожимается на компрессорной станции 1 и направляется на УНТС 2, где из него выделяется осушенный газ, состоящий в основном из метана.
Далее осушенный газ, в случае необходимости, поступает в блок 3 абсорбционной очистки для удаления вредных примесей, а затем уже в качестве товарного газа направляется в сеть магистральных газопроводов.
Конденсат с УНТС 2 поступает в блок 4 колонны стабилизации, где разделяется на СУГ (пропан-бутановая фракция) и фракцию С5 и выше. СУГ вначале подаются на установку 5 очистки, включающую блок экстракционной отмывки и адсорбционной осушки, с целью удаления вредных для катализатора примесей (вода, метанол, соли), а затем направляются в реакторный блок 6 платформинга с непрерывной регенерацией катализатора. Газы деэтанизации отводятся на прием дожимной компрессорной станции 1 и далее на УНТС 2, где из них выделяется товарный осушенный газ, конденсат направляется в блок 4 колонны стабилизации. Продукты реакции из реакторного блока 6 подаются в блок 7 разделения (блок сепараторов и мембранную установку), где делятся на углеводородный газ, водород (возвращается в реакторный блок 6) и жидкие продукты.
Жидкие продукты реакции - смесь ароматических углеводородов с остатками не прореагировавших СУГ - смешиваются с конденсатом УНТС 2 и подаются в блок 4 колонны стабилизации, где пропан-бутановая фракция выделяется из смеси ароматических углеводородов и фракции C5 и выше, а затем в качестве сырья направляется в реакторный блок 6 платформинга. Смесь ароматических углеводородов и фракции С5 и выше может быть частично использована как компонент автомобильного бензина, но в основном направляется в состав товарной нефти.
Также возможен вариант, когда в блоке 7 жидкие продукты реакции разделяются на непрореагировавшие СУГ, которые подаются на вход реакторного блока 6 платформинга, и смесь ароматических углеводородов, по меньшей мере часть которой подаются в магистральный нефтепровод в составе товарной нефти.
Попадая в состав товарной нефти, смесь ароматических углеводородов не оказывает негативного влияния на ее качественные характеристики. Соотношение потоков товарной нефти и смеси ароматических углеводородов ничтожно мало (в среднем 100:1), чтобы говорить о каком-либо заметном влиянии, хотя и оно оказывается положительным:
Во-первых - высокая вязкость довольно часто становится причиной проблем, связанных со сдачей товарной нефти в сеть трубопроводов. Добавление смеси ароматических углеводородов позволит снизить вязкость товарной нефти.
Во-вторых - при фракционировании нефти на нефте-перерабатывающих заводах ароматические углеводороды (бензол, толуол и ксилолы) попадают в основном в состав тяжелой нафты, которая, как правило, направляется на каталитический риформинг, в основе которого лежат те же процессы ароматизации.
Следует отметить, что технологии платформинга СУГ известны и отработаны. В 1990 году в г.Грейнджмауте (Шотландия) в опытно-промышленную эксплуатацию была запущена (в настоящее время демонтирована) установка получения ароматического концентрата из пропан-бутановой фракции производительностью 400 тыс. тонн в год. В настоящее время в промышленной эксплуатации находится одна подобная установка. Эта установка производительностью 800 тыс. тон в год. входит в состав нефтехимического комплекса компании «САБИК», расположенной в г.Ямбу, Саудовская Аравия. Разработчиком технологии этих установок и патентообладателем является компания UOP.
Отсутствие широкого промышленного применения установок платформинга СУГ в составе нефтехимических комплексов объясняется тем, что в качестве товарного продукта получается смесь ароматических углеводородов, реализация которой в качестве товарной продукции не представляется возможным ввиду ее низкой стоимости. Получить приемлемую стоимость продуктов платформинга возможно только путем их разделения на индивидуальные углеводороды, что является многоступенчатым и очень дорогостоящим процессом, делающим экономические показатели платформинга значительно хуже, чем у других конкурирующих процессов. В случае нефтяных и газоконденсатных промыслов, вопрос о переработке СУГ не рассматривался вообще.
Предложенное изобретение позволяет эффективно применить технологию платформинга СУГ, встроив ее в процесс промысловой подготовки продукции нефтяных и газоконденсатных месторождений.
1. Способ переработки углеводородных газов нефтяных и газоконденсатных месторождений, включающий промысловую подготовку попутного нефтяного газа (ПНГ) или «сырого газа» с получением товарного осушенного газа и газового конденсата, подачу конденсата на стадию стабилизации с выделением из упомянутого газового конденсата сжиженных углеводородных газов (СУГ), очистку СУГ, реакционное превращение СУГ в смесь ароматических углеводородов на стадии платформинга, разделение продуктов реакции платформинга на водород, углеводородный газ и жидкие продукты реакции, после чего подают углеводородный газ в поток ПНГ или «сырого газа», поступающего на промысловую подготовку, а из жидких продуктов реакции выделяют ароматические углеводороды, по меньшей мере часть которых подают в магистральный нефтепровод в составе товарной нефти.
2. Способ по п.1, отличающийся тем, что выделение из жидких продуктов реакции ароматических углеводородов осуществляют путем разделения жидких продуктов реакции на непрореагировавшие СУГ, которые подают на вход стадии платформинга, и смесь ароматических углеводородов, по меньшей мере часть которой подают в магистральный нефтепровод в составе товарной нефти.
3. Способ по п.1, отличающийся тем, что выделение из жидких продуктов реакции ароматических углеводородов осуществляют путем подачи жидких продуктов реакции на вход стадии стабилизации для отделения непрореагировавших СУГ, а выходящую из него смесь С5+ и ароматических углеводородов, по меньшей мере часть которой подают в магистральный нефтепровод в составе товарной нефти.
4. Способ по п.1, отличающийся тем, что после разделения продуктов реакции водород подают на стадию платформинга.
5. Способ по п.1 или 3, отличающийся тем, что на стадии стабилизации используют блок колонны стабилизации газового конденсата установки промысловой подготовки ПНГ или «сырого газа».
6. Способ по п.1, отличающийся тем, что очистку СУГ осуществляют путем экстракционной отмывки и последующей адсорбционной осушки, а образующийся газ деэтанизации подают в поток ПНГ или «сырого газа», поступающего на промысловую подготовку.
7. Установка для переработки углеводородных газов нефтяных и газоконденсатных месторождений, содержащая трубопровод подачи попутного нефтяного газа (ПНГ) или «сырого» газа и связанные с ним и между собой системой трубопроводов аппараты установки промысловой подготовки ПНГ и «сырого» газа компрессорную станцию, а именно установку низкотемпературной сепарации, блок адсорбционной очистки, выход которого соединен с трубопроводом отвода товарного осушенного газа, блок колонны стабилизации газового конденсата и установку очистки сжиженных углеводородных газов (СУГ), а также соединенный с выходом СУГ установки очистки реакторный блок платформинга и соединенный с выходом реакторного блока блок разделения продуктов реакции, выход жидких продуктов которого соединен со входом блока колонны стабилизации, а выход углеводородного газа которого соединен с трубопроводом подачи ПНГ или «сырого» газа, а второй выход блока колонны стабилизации соединен с трубопроводом отвода смеси углеводородов С5+ и ароматических углеводородов в магистральный нефтепровод.
8. Установка по п.7, отличающаяся тем, что блок разделения выполнен с возможностью разделения жидких продуктов реакции на непрореагировавшие СУГ и смесь ароматических углеводородов, при этом его указанный выход жидких продуктов, соединенный с входом блока колонны стабилизации, является выходом непрореагировавших СУГ, а его выход смеси ароматических углеводородов соединен с трубопроводом отвода смеси углеводородов С5+ и ароматических углеводородов в магистральный нефтепровод.
9. Установка по п.7, отличающаяся тем, что выход водорода блока разделения соединен с входом реакторного блока платформинга.
www.findpatent.ru
Сведения об авторах. Аболенцев Игорь Сергеевич
Тел.: +7(498)
267 Сведения об авторах Авдиенко Игорь Николаевич Алипов Андрей Васильевич Бочков Александр Владимирович Бурутин Олег Викторович Васкань Игорь Ярославович Власова Лада Владимировна Волохина Алла Тагировна
ПодробнееПРОГРАММА Конференции
Национальная палата инженеров ПРОГРАММА Конференции Тема: Пожарная безопасность: особенности проектирования, техническое регулирование 11 февраля 2016 года РЕГЛАМЕНТ РАБОТЫ КРУГЛОГО СТОЛА 11 февраля 2016
ПодробнееА.И. Ларюхин, Л.Н. Еремина, Р.А. Митницкий
106 Научно-технический сборник ВЕСТИ ГАЗОВОЙ НАУКИ УДК 622.276+661 А.И. Ларюхин, Л.Н. Еремина, Р.А. Митницкий Мониторинг физико-химических характеристик углеводородов для контроля и совершенствования добычи,
ПодробнееАННОТАЦИИ РАБОЧИХ ПРОГРАММ ДИСЦИПЛИН
ПРИЛОЖЕНИЕ АННОТАЦИИ РАБОЧИХ ПРОГРАММ ДИСЦИПЛИН 2 Министерство образования и науки Российской Федерации Российский государственный университет нефти и газа имени И.М. Губкина АННОТАЦИЯ РАБОЧАЯ ПРОГРАММА
ПодробнееОтчѐт Совета Партнерства
1 Отчѐт Совета Партнерства Некоммерческого партнерства «Объединение организаций выполняющих инженерные изыскания в газовой и нефтяной отрасли «Инженер-Изыскатель» (НП «Инженер-Изыскатель») за 2009 год
Подробнеекэио N / от
кэио N2 11-22491/16-0-0 от 02.12.2016 ПРАВИТЕЛЬСТВО САШТ-ПЕТЕРБУРГА КОМИТЕТ ПО ЭНЕРГЕТИКЕ И ИНЖЕНЕРНОМУ ОБЕСПЕЧЕНИЮ РАСПОРЯЖЕНИЕ О внесении изменений в распоряжение Комитета по энергетике и инженерному
Подробнееотзыв 1. Актуальность темы
отзыв официального оппонента на диссертационную работу Заночуева Сергея Анатольевича «Фазовые переходы и массообмен в призабойной зоне газоконденсатных скважин», представляемой на соискание ученой степени
ПодробнееУТВЕРЖДЕНО. г. Владимир. Прохоров В. А.
УТВЕРЖДЕНО Заместитель председателя Территориальной экзаменационной комиссии по проверке и оценке необходимых знаний водителей автотранспортных средств, перевозящих опасные грузы в Владимирской (г. Владимир)
ПодробнееУтвержден приказом Президента АК «АЛРОСА» (ПАО) от 11.06.2015 г. А01/158-П Состав Экспертного совета по инновациям при Президенте АК «АЛРОСА» Председатель Экспертного совета Чаадаев Александр Сергеевич
ПодробнееОТ ПРОЕКТА ДО РЕАЛИЗАЦИИ
ОТ ПРОЕКТА ДО РЕАЛИЗАЦИИ НПО «ИНГАЗПЕРЕРАБОТКА» Научно-Производственное Объединение «Институт Переработки Газа и Газового Конденсата» - объединяет проектные офисы и конструкторские бюро в Москве, Новомосковске
ПодробнееПОЯСНИТЕЛЬНАЯ ЗАПИСКА
Открытое Акционерное Общество «Газпром» ОБЩЕСТВО С ОГРАНИЧЕННОЙ ОТВЕТСТВЕННОСТЬЮ «НАУЧНО-ИССЛЕДОВАТЕЛЬСКИЙ ИНСТИТУТ ПРИРОДНЫХ ГАЗОВ И ГАЗОВЫХ ТЕХНОЛОГИЙ ГАЗПРОМ ВНИИГАЗ» (ООО «Газпром ВНИИГАЗ») ПОЯСНИТЕЛЬНАЯ
ПодробнееАВТОРЫ СБОРНИКА «ФЕДЕРАЛЬНЫЙ СПРАВОЧНИК.
АВТОРЫ СБОРНИКА «ФЕДЕРАЛЬНЫЙ СПРАВОЧНИК. Заместитель Председателя Правительства Министр обороны председатель Комитета Государственной Думы по обороне Дмитрий Олегович Рогозин Анатолий Эдуардович Сердюков
ПодробнееНАУЧНО-ТЕХНИЧЕСКИЙ СОВЕТ ПАО «РОССЕТИ»
НАУЧНО-ТЕХНИЧЕСКИЙ СОВЕТ ПАО «РОССЕТИ» СЕКЦИЯ «УПРАВЛЕНИЕ РЕЖИМАМИ, АВТОМАТИЗАЦИЯ И ПРИМЕНЕНИЕ АВТОМАТИЧЕСКОГО УПРАВЛЕНИЯ В ЭЛЕКТРИЧЕСКИХ СЕТЯХ» УТВЕРЖДАЮ Руководитель секции НТС Г.С. Нудельман «19» мая
ПодробнееФакультет техники разведки и разработки
Факультет техники разведки и разработки РГГРУ Декан факультета техники разведки и разработки Н.Н.Клочков Факультет техники разведки и разработки Началом истории факультета можно считать 1-е июля 1930 года,
ПодробнееГУБЕРНАТОР МАГАДАНСКОЙ ОБЛАСТИ
ГУБЕРНАТОР МАГАДАНСКОЙ ОБЛАСТИ П О С Т А Н О В Л Е Н И Е от «17» августа 2015 г. 152-п г. Магадан О внесении изменений в постановление губернатора от 11 июня 2013 г. 85-п П о с т а н о в л я ю: 1. Внести
ПодробнееЩеколдин Дмитрий Александрович
Щеколдин Дмитрий Александрович Дата рождения: 30 апреля 1982 г. Гражданство: Российская Федерация Место жительства: Архангельск, Российская Федерация Телефон: +7 911 557 75 74 E-mail: [email protected]
ПодробнееЭКСПЛУАТАЦИЯ НЕФТЯНЫХ И ГАЗОВЫХ СКВАЖИН
ФЕДЕРАЛЬНОЕ ГОСУДАРСТВЕННОЕ БЮДЖЕТНОЕ ОБРАЗОВАТЕЛЬНОЕ УЧРЕЖДЕНИЕ ВЫСШЕГО ОБРАЗОВАНИЯ «САХАЛИНСКИЙ ГОСУДАРСТВЕННЫЙ УНИВЕРСИТЕТ» Аннотация рабочей программы дисциплины ЭКСПЛУАТАЦИЯ НЕФТЯНЫХ И ГАЗОВЫХ СКВАЖИН
Подробнееdocplayer.ru