Сибур Тобольскранее Тобольск-Нефтехим. Завод в тобольске сибур
Сибур Тобольск (ранее Тобольск-Нефтехим)
Компания
Сибур Тобольск входит в состав СИБУРа и является одним из крупнейших в мире предприятий по переработке углеводородного сырья.Собственники:Сибур, АКПроизводство
"СИБУР Тобольск" осуществляет прием и переработку широкой фракции легких углеводородов, которая поступает на предприятие по продуктопроводу с западносибирских газоперерабатывающих заводов СИБУРа. В дальнейшем на газофракционирующей установке сырье разделяется на отдельные фракции: пропан, бутан, изобутан и т. д. После этого сжиженные углеводородные газы и мономеры — бутадиен и изобутилен, поступают на нефтехимические предприятия СИБУРа. Изобутилен также используется «СИБУР Тобольском» для выработки метил-трет-бутилового эфира.
Бутадиен и изобутилен являются исходными мономерами для выработки синтетических каучуков, которые, в свою очередь, используются для производства резин. Метил-трет-бутиловый эфир служит в качестве кислородосодержащего, высокооктанового компонента при получении неэтилированных, экологически чистых бензинов.
История
2016: Переименование в "СИБУР Тобольск"
ООО "Тобольск-Нефтехим" переименовано в ООО "СИБУР Тобольск".
2014: Запуск крупнейших в мире газофракционирующих установок
4 июня 2014 г. вторая очередь газофракционирующей установки по переработке широкой фракции лёгких углеводородов (ШФЛУ) запущена в эксплуатацию. Одновременно был реализован проект по увеличению мощности действующей газофракционирующей установки с 3 млн тонн в год до 3,8 млн тонн в год. Таким образом, суммарная мощность газофракционирующих установок составила 6,6 млн тонн в год и является крупнейшей в мире.
2012: В.Анохин сменяет Л.Жернакова на посту гендиректора
В августе 2012 года генеральный директор компании Леонид Жернаков вышел на пенсию. Руководителем предприятия назначен Владимир Анохин, ранее занимавший должность первого заместителя генерального директора – главного инженера. В свою очередь, Геннадий Савин занял должность первого заместителя генерального директора – главного инженера.
2011
На 2011 год производственные мощности «Тобольск-Нефтехима» включают в себя центральную газофракционирующую установку мощностью 3 млн. т сжиженных газов в год, производство мономеров для выработки синтетических каучуков — бутадиена (197 тыс. т в год) и изобутилена 83 тыс. т в год), а также производство метил-трет-бутилового эфира - 120 тыс. т в год.
В корпоративной структуре СИБУРа «Тобольск-Нефтехим» входит в состав дирекции углеводородного сырья, которую возглавляет вице-президент Михаил Карисалов.
2010: Старт работ второй очереди по созданию установки по переработке (ШФЛУ)
В августе 2010 года инвестиционный комитет СИБУРа принял решение о начале проектных работ в рамках реализации проекта по строительству второй очереди газофракционирующей установки по переработке широкой фракции лёгких углеводородов (ШФЛУ) мощностью 2,8 млн т в год.
2001: Переименование в «Тобольск-Нефтехим»
Тобольский нефтехимический комбинат перерегистрирован как «Тобольск-Нефтехим».
1999: Вхождение в состав "Сибура"
В 1999 году состоялось вхождение Тобольского нефтехимического комбината в состав СИБУРа. Загрузка мощностей была восстановлена.
Началась разработка проекта строительства нового производства полипропилена и реконструкция продуктопровода протяженностью 1000 км. Параллельно было запущено строительство насосной станции, увеличивающей производительность продуктопровода.
В 1990–е годы с большими задержками были введены в эксплуатацию производства изобутилена и метил-требутилового эфира МТБЭ.
1990: Заморозка проекта по бутил- и галобутилкаучуков
Заморозка проекта по производству бутил- и галобутилкаучуков. Предприятие столкнулось с недопоставкой сырья, низкой загрузкой технологических установок, износом основных фондов на 70%.
1988: Начало строительства производства бутил- и галобутилкаучуков
Начало строительства производства бутил- и галобутилкаучуков мощностью 90 тыс. тонн в год.
1987: Запуск установки по производству бутадиена
В 1987 году на предприятии были введены в строй установки по производству бутадиена производительной мощностью 180 тыс. т в год.
1984: Запуск центральной газофракционирующей установки
Запуск центральной газофракционирующей установки на Тобольском нефтехимическом комбинате состоялся в 1984 году. Новое производство требовало привлечения целого ряда квалифицированных специалистов, которые стали приезжать на комбинат со всей страны. Буквально за несколько лет население Тобольска выросло более чем в два раза — с 46 тыс. до 110 тыс. человек. Тобольский нефтехимический комбинат приобрел статус градообразующего предприятия.
1975: Начало строительства комбината
История «СИБУР Тобольска» началась в 1970-е годы. В то время государство решило реализовать проект по строительству крупнейшего в стране предприятия по комплексной глубокой переработке углеводородного сырья с месторождений Западной Сибири. Проект был масштабным: помимо производства мономеров, на территории Тюменской области предполагалось строительство мощностей по выпуску синтетических каучуков, крупного нефтеперерабатывающего завода, завода по производству пластмасс и товаров народного потребления.
В 1974 году в 6 км от Тобольска была выбрана площадка под строительство комбината, и с 1975 года 60 проектных институтов приступили к разработке проектной документации. Одновременно с возведением ряда нефтехимических производств строилась и вся окружающая инфраструктура. Она создавалась по новейшим технологиям, подчас не имеющим аналогов в стране.
www.tadviser.ru
ОАО «Тобольский нефтехимический комбинат» - особенности и отзывы
«Гигант на Иртыше» - так называли Тобольский нефтехимический завод в период его строительства. Объект считался всесоюзной стройкой, на которой применяли передовые разработки ведущих научных институтов страны. Более шестидесяти НИИ принимали участие в возведении цехов, разработке технологических линий и отладке процессов производства. На сегодняшний день завод усилил свои позиции на рынке, запустив новые производственные мощности.
История
Разработку проекта Тобольского нефтехимического комбината начали в 1974 году. Завод строили с целью обеспечения внутреннего рынка синтетическим каучуком, товарами народного потребления, пластмассами и другими необходимыми продуктами химического производства. Площадку для размещения предприятия выбрали в шести километрах от старинного города Тобольск. Вместе с производственным комплексом возводили и окружающую инфраструктуру. В 1984 году состоялся запуск центральной газофракционирующей установки, что повлекло приток квалифицированных специалистов.
Рабочие и инженеры ехали работать на Тобольский нефтехимический завод семьями со всего Советского Союза. Население тихого Тобольска за несколько лет существенно увеличилось, а предприятие получило статус градообразующего объекта. На конец 80-х годов пришелся пик наращивания мощностей. В 1987 году были сданы в эксплуатацию установки синтеза бутадиена, их мощность составила 180 тысяч тонн в год.
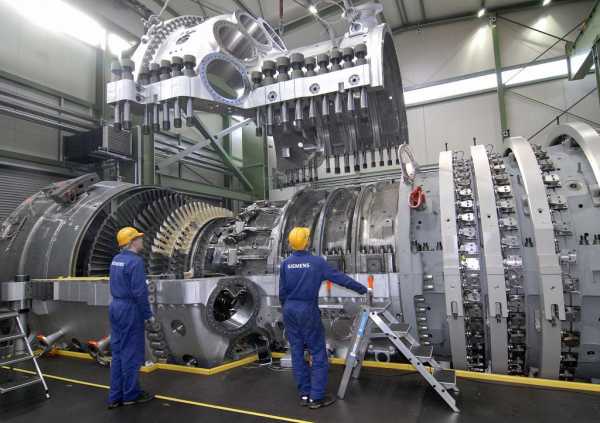
В 1988 году начался первый этап реализации совместного советско-итальянского проекта по строительству линий производства бутилкаучуков и галобутилкаучуков, проектная мощность линий была запланирована на уровне 90 тысяч тонн готовой продукции в год. На выбранную площадку завезли оборудование, началось строительство цехов и закладка коммуникаций. Финансирование осуществлялось за счет кредитных линий иностранных банков. Развал Советского Союза привел к остановке финансирования и заморозке проекта.
Кризисные девяностые
Смена экономического и социального строя в стране, разрыв производственных связей поставили Тобольский нефтехимический комбинат на грань выживания. В этот период существенно сократились поставки сырья, износ производственных фондов в некоторых местах составил около 70 %, заработную плату выплачивали редко – в таком положении завод находился до конца 90-х годов. Фактически предприятие было банкротом. В 1999 году «Тобольск-Нефтехим» перешел в управление компании СИБУР, получив статус открытого акционерного общества. В компании разделили сферы влияния, оставив за производственным комплексом только рабочие функции.
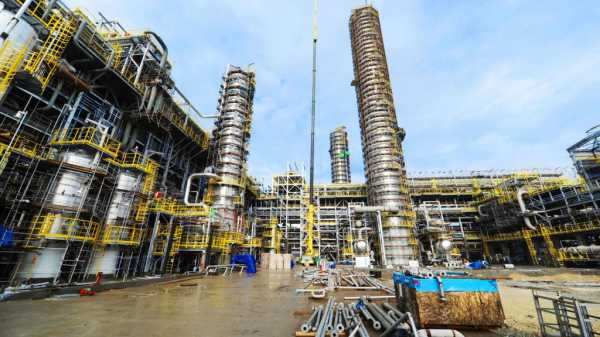
С 2000-х годов ОАО «Тобольский нефтехимический комбинат» начал восстановление своего потенциала. Довольно быстро были налажены бесперебойные поставки сырья в необходимом объеме, найдены рынки сбыта готовой продукции, производственные мощности получили полную загрузку, фонд заработной платы был полностью восстановлен, а долги перед трудовым коллективом погашены.
Современность
Нефтехимический комплекс Тобольска вошел в структуру СИБУРа как филиал АО «Сибур-Тюмень», с 2001 года юридический статус комбината был изменен и теперь компания является ООО «Тобольск-Нефтехим». На сегодняшний день предприятие – один из крупнейших нефтехимических производственных комплексов. Мощности комбината включают центральную газофракционирующую установку, вырабатывающую до 3 миллионов тонн газов в год, производственные мощности по изготовлению мономеров, являющихся основным сырьем в производстве синтетических каучуков, вырабатывают в год 180 тыс. т бутадиена и 86 тыс. т изобутилена.
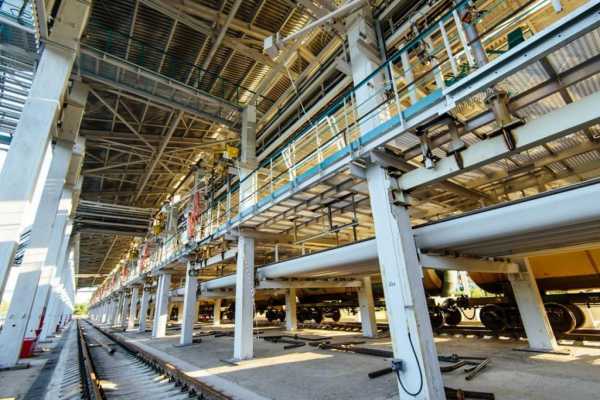
Кроме основной продукции, Тобольский нефтехимический комбинат производит экологически чистые присадки к бензину (эфир метилтретбутиловый), применение которых значительно увеличивает октановое число горючего. На базе производственного комплекса реализуются масштабные инвестиционные проекты. В 2010 году была смонтирована еще одна газофракционирующая установка для работы с легкими фракциями углеводородов, мощность оборудования составляет 2,8 млн тонн в год готового продукта.
Существующая и много лет работающая газофракционирующая установка, подверглась модернизации. Теперь ее производительность около 3,8 миллионов тонн продукции в год (было – 3 млн). После реализации двух проектов ОАО ТНХК «Тобольск» стал крупнейшим мировым производителем широкой фракции углеводородов.
Комбинат выпускает следующую продукцию:
- Сжиженные газы (н-бутан, пропан, изобутан).
- Полипропилен.
- Мономеры (бутадиен, изобутилен).
- Эфир метил-трет-бутиловый.
- Жидкости легковоспламеняющиеся (гексан, изопентан, н-пентан).
Положительные отзывы
ОАО «Тобольский нефтехимический комбинат» отзывы с положительными рецензиями получил от многих сотрудников. Они написали, что, несмотря не жесткий отбор кадров, они согласились бы пройти этот этап еще раз. Результатом тщательного отбора персонала стала команда отличных профессионалов, с которыми быстро удается найти общий язык. Отмечено, что большинство специалистов легко справляется с поставленными перед ними задачами, видит цели и достигает их.
На предприятии созданы хорошие условия работы на каждом уровне, это отмечают рабочие и топ-менеджеры. Выплачиваемая заработная плата достаточна для того, чтобы не чувствовать себя ущемленным, высокие ставки и премии позволяют не задумываться о поиске дополнительных источников дохода. Некоторые написали, что получив предложение переехать в Тобольск для работы на нефтехимическом комбинате, были приятно удивлены условиями.
Работнику компенсировали затраты на переезд всей семьи, предоставляли комфортную квартиру в новом жилом фонде с возможностью последующего выкупа, причем с 50 % скидкой. При этом сотрудник получал подъемные выплаты, заявленные заработные платы и премии полностью соответствовали указанным суммам в трудовом договоре.
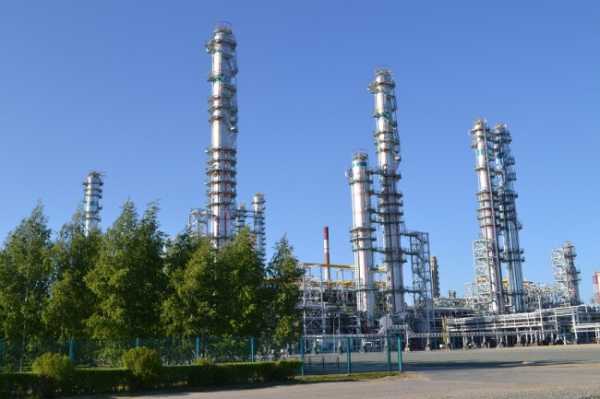
Специалисты ИТР указали, что кроме интересного поля деятельности с нестандартными задачами, каждый из них имеет возможность повышать уровень квалификации на научных семинарах, симпозиумах, встречах с зарубежными и отечественными учеными, профессионалами смежных областей. Большая часть сотрудников рекомендуют устраиваться на работу в СИБУР Тобольска, хотя для этого придется приложить немало усилий, но оно того стоит – это обязательно принесет колоссальный опыт, отличные условия труда, реальные перспективы карьерного роста.
Отрицательные отзывы
Небольшая часть отрицательных рецензий рассказывает о том, что специалисты отдела кадров не всегда ответственно относятся к своей работе – могут забыть о претенденте на последнем этапе его тестирования. То есть пообещать дать ответ и в итоге не сделать этого. Также нередки затягивания процессов. Многие желают устроиться на работу в Тобольский нефтехимический комбинат и готовы ожидать, когда отдел кадров полностью подберет персонал из претендентов, получивших положительное решение. Иногда процесс занимает 3-4 месяца, за это время соискатели получают предложения из других компаний и отказываются от них, но в результате выясняется, что кандидат по каким-либо незаявленным причинам не подошел компании СИБУР. В итоге работник оказывается без нескольких отличных перспектив, связаться с отделом кадров почти невозможно.
Часть рабочего персонала написали в отзывах, что обещанные премии они редко получают, а также считают, что класс вредности предприятия не объективен и урон здоровью наносится весьма ощутимый. Они же отмечают, что компания регулярно отправляет сотрудников на медицинскую комиссию, все расходы по ее оплате лежат на предприятии, а необходимое лечение сотрудник получает бесплатно по полисам ДМС.
Общее впечатление
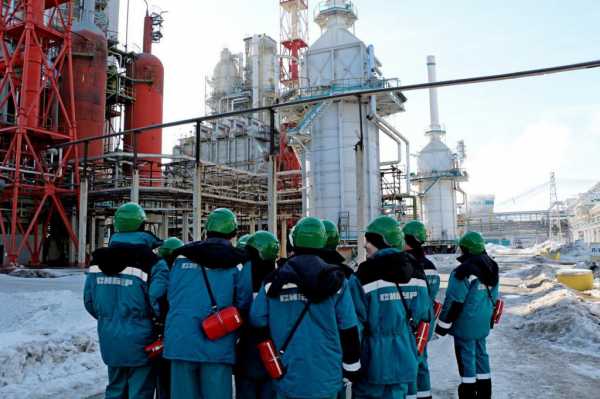
Компания создает не только необходимый для страны продукт, но и вкладывает средства в охрану окружающей среды, создает качественные условия труда для всех сотрудников, выплачивает достойное вознаграждение за труд и занимается обучением персонала.
fb.ru
«Тобольск-Нефтехим» и «Тобольск-Полимер» - гордость нефтехимии Сибири - ZAVODFOTO.RU
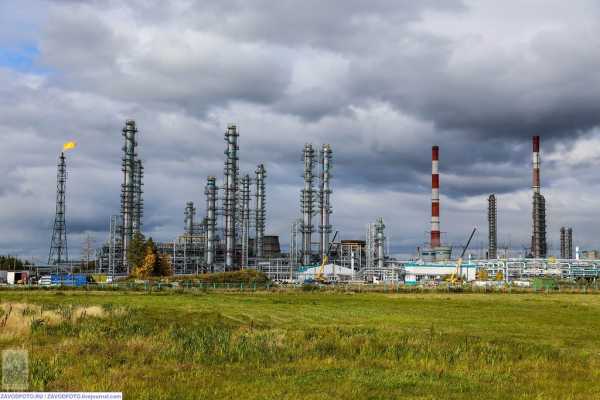
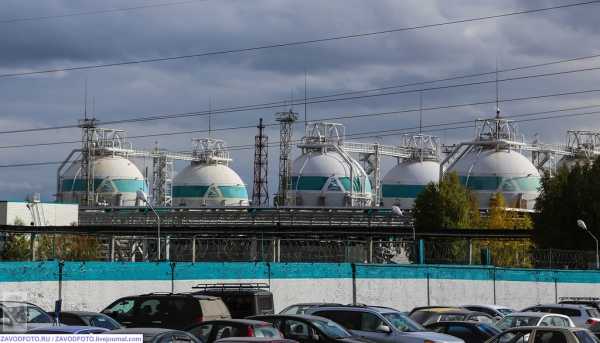
ООО «Тобольск-Нефтехим» сейчас специализируется на приёме и дальнейшей переработке широкой фракции легких углеводородов, которые по продуктопроводу (Южный Балык - Тобольск-Нефтехим и Пуровский ЗПК - Тобольск-Нефтехим») сюда поступают с западносибирских газоперерабатывающих заводов СИБУРа. В итоге на выходе получаются сжиженные газы (пропан, изобутан, н-бутан), легковоспламеняющиеся жидкости (изопентан, н-пентан, гексан), мономеры (бутадиен и изобутилен), которые в свою очередь служат сырьём для производства каучука и пластиков, автомобильных шин, моющих средств и т.д., а также метил-трет-бутиловый эфир, используемый как высокооктановая добавка к бензинам.
3.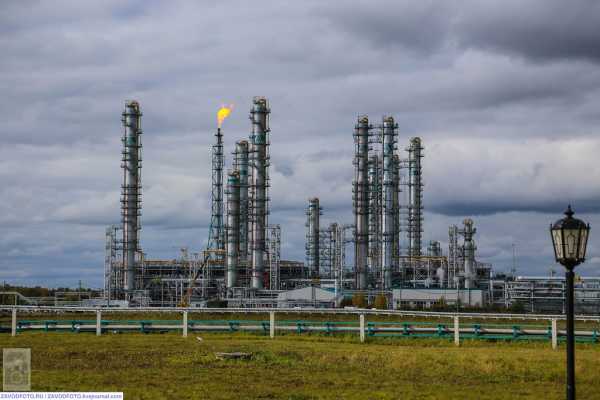
Производственные мощности завода, расположенные на площади 1 176 гектар, включают в себя центральную газофракционирующую установку мощностью 3,8 млн. тонн сжиженных газов в год, 4 июня 2014 года была запущена в эксплуатацию вторая очередь газофракционирующей установки мощностью 2,8 млн т в год, тем самым суммарная мощность достигла 6,6 млн тонн в год и поэтому показателю наш завод является крупнейшим в мире. Плюс есть производство мономеров для выработки синтетических каучуков - бутадиена и изобутилена, а также производство метил-трет-бутилового эфира.
4.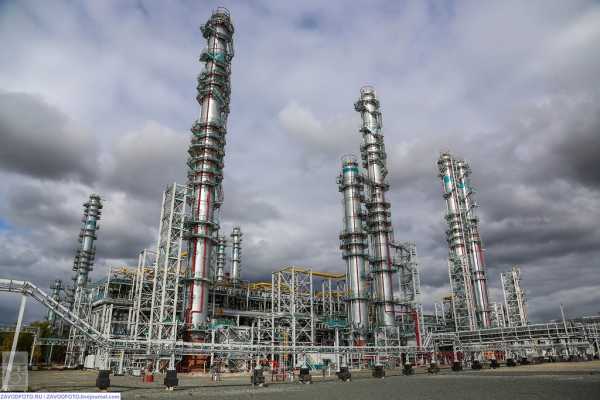
5. Центральная газофракционирующая установка «Тобольск-Нефтехим»
6.
7. Технологический факел, самая высокая вершина предприятия, его высота около 130 м.
8.
9.
10.
11. Центральный диспетчерский пункт. Тут настолько всё серьезно и автоматизировано, что если надо, всего одной кнопкой можно остановить всё предприятие.
12.
13.
14.
15.
20 апреля 2006 года на базе Тобольской производственной площадки СИБУРа было зарегистрировано ООО «Тобольск-Полимер». В 2007 году были подписаны ряд соглашений, которые позволили начать реализацию столь масштабного проекта современности и в апреле этого же года была утверждена мощность будущего производства полипропилена - 500 тыс. тонн в год. За дегидрирование отвечала американская компания UOP, а за полипропилен - Ineos (Великобритания). Всего же было задействовано более 320 компаний из 23 стран. Осенью 2010 на стройплощадку были доставлены первые единицы крупногабаритного оборудования, в частности, одна из двух продувочных колонн длиной 39,5 метра, диаметром 4,6 метра и весом 60 тонн, изготовленная в Корее. А всего в Тобольск прибыло 23 единицы такого нестандартного груза, в том числе колонны установки дегидрирования пропана. Диаметр одной из них составляет 10 метров, длина - около 100 метров, а вес - 1096 тонн. Чтоб весь этот груз доставить были задействованы 18 судов, 992 железнодорожных вагонов, 1 957 автотрейлеров.
16.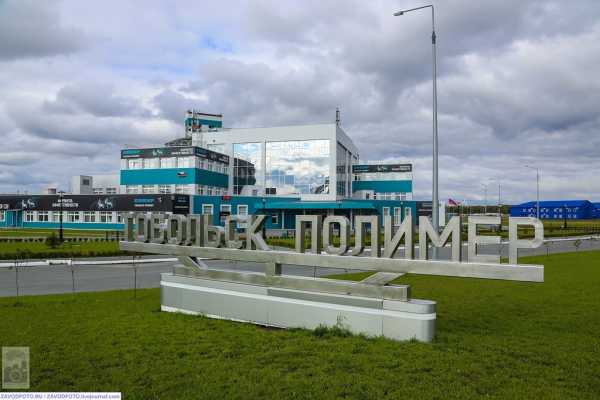
15 октября 2013 года в присутствии президента РФ Владимира Путина состоялась торжественная церемония открытия и запуска комплекса. Вся стройка обошлась почти в 2 млрд $. Эх, хорошо, что успели до всех этих санкций. Благодаря запуску этого завода, производство полипропилена в России увеличилось примерно на 40%, и мы из импортера перешли в ранг экспортёров. Вот оно импортзамещение на лицо. Во всех бы отраслях такой прогресс.
17.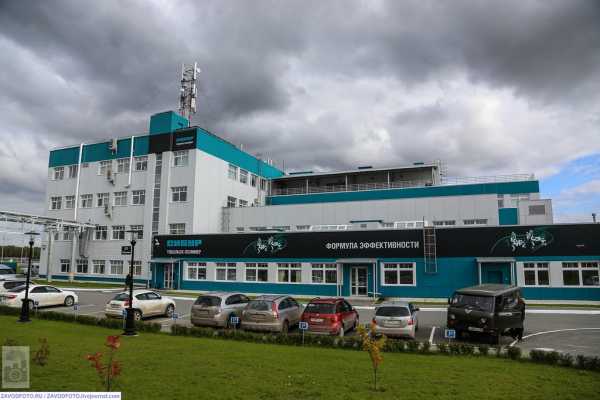
Сам производственный комплекс «Тобольск-Полимер» состоит из производства пропилена мощностью 510 тысяч тонн в год и производства полипропилена мощностью 1 500 тысяч тонн в год, и по этим показателям завод входит в тройку мировых лидеров в этом сегменте. Опять есть повод гордиться за наших! Для понимания сколько это в граммах :). Например, из 500 тыс. тонн полипропилена можно получить 50 млн автомобильных бамперов или 1 млн 350 тыс. км водопроводных труб диаметром 50 мм (этого хватит, чтобы обогнуть Землю по экватору 34 раза) или 243 млрд пластиковых стаканчиков или для изготовления 2 млрд тазиков, а этого количества легко хватит, чтобы обеспечить каждую вторую семью в мире.
18. Склад хранения и отгрузки готовой продукции «Тобольск-Полимера»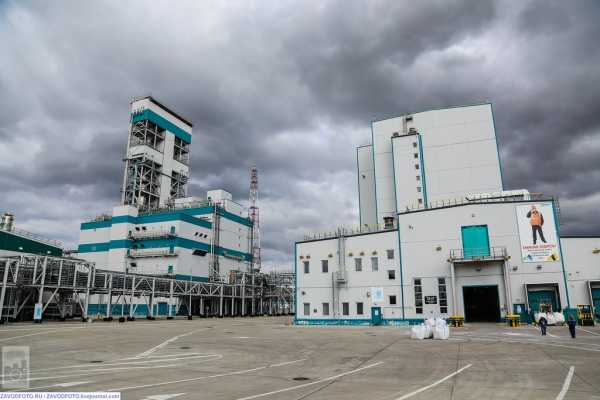
Полипропилен является 3-м по потреблению в мире пластиком после полиэтилена и ПВХ, и широко применяется в различных отраслях промышленности: автомобильной, ЖКХ, производстве товаров народного потребления упаковка, плёнка, мебель, посуда). Из себя он представляет твердый термопластичный полимер. Всего в ассортименте выпускаемой продукции завода более чем 70 позиций. Сырье для предприятия (пропан) поставляется с газофракционирующих установок «Тобольск-Нефтехима», вот такая синергия получается.
19.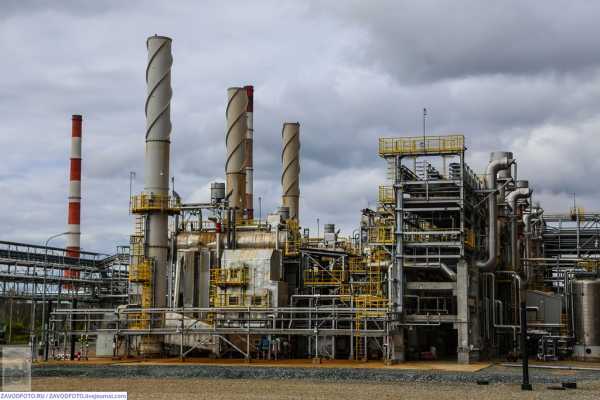
Что касается самого технологического процесса, то производство дегидрирования пропана (ДГП) основано на новой современной технологии «Oleflex» фирмы UOP. Эта установка представляет собой процесс каталитического дегидрирования пропана в пропилен с использованием непрерывной регенерации катализатора. Горячее сырье последовательно проходит дегидрирование в четырех реакторах с непрерывной регенерацией катализатора. Горячий отходящий поток из реактора охлаждается, компримируется, и направляется на осушку в секцию сепарации, где отходящий газ разделяют на рецикловый газ и жидкий продукт. Жидкий продукт направляется в этаноотгонную колонну. Кубовый продукт из этаноотгонной колонны поступает в пропан-пропиленновый разделитель. Пары, отводимые с верха пропан - пропиленного разделителя конденсируются. Часть жидкости возвращается в колонну в виде флегмы. Оставшаяся часть товарного пропилена направляется на производство полипропилена или на склад.
20. Производство дегидрирования пропана «Тобольск-Полимер»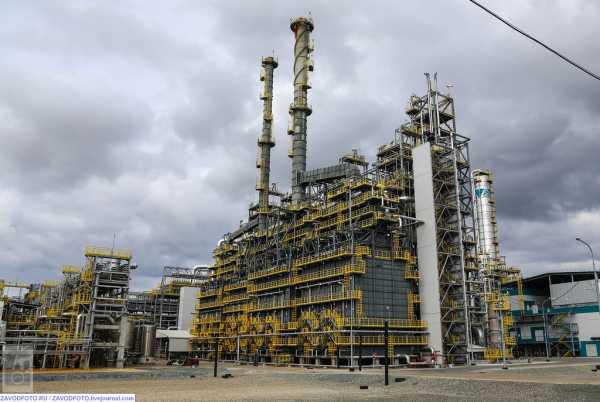
21. Это самая большая колонна комплекса, её высота 96 метров, диаметр 10,5 метра, а вес 1 086 тонн. Чтоб её установить потребовалось 6 часов.
Производство полипропилена (ПП) основано на каталитическом процессе и производится на лицензионной установке (компания-лицензиар INEOS LLC, США) по запатентованной технологии полимеризации пропилена в газовой фазе «Innovene». Здесь используется высокоактивный, обладающий очень высокой селективностью, катализатор, что позволяет получать продукцию очень высокого качества, при этом есть возможность изменять выход продукции и марку получаемого полипропилена в зависимости от параметров технологического процесса (давление, температура и пр.).
22. Производство полипропилена «Тобольск-Полимер»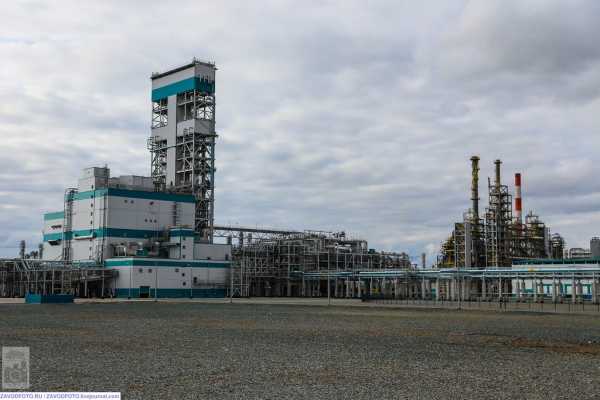
23.
24.
25. Проверено блогерами, здоровская компания! Надеюсь, что я сюда ещё вернусь и более подробно познакомлюсь с этой производственной площадкой, тем более, что здесь ещё что-то строится, а мы из-за отсутствия времени, это так и не посмотрели.
Большое спасибо организаторам за приглашение, а ребятам: Антону anton_petrus , Марине rebro_a_dama , Сергею sergeimac , Пушбе pushba , Раису rais , Сергею aquatek_filips , Ниязу mamonino , Борису ochendaje , Александру aperestoronin и Олегу freedom за компанию!
Ещё из нашей поездки в Тобольск-Тюмень:
Другие производственные активы ПАО «СИБУР ХОЛДИНГ», которые я посетил:
P. S. Уважаемые собственники и акционеры, представители пресс-служб компаний, отделы маркетинга и другие заинтересованные лица, если на Вашем предприятие есть, что показать - "Как это делается и почему именно так!", мы всегда рады принять участие. Не стесняйтесь, пишите нам сами [email protected] и расскажите о себе, пригласив нас к ВАМ в гости. Берите пример с лидеров!
ПРОЕКТ: ZAVODFOTO - Шагает по стране! и ПРОЕКТ: «Пермский край - Нам есть чем гордиться!»
zavodfoto.livejournal.com