СИБУР И ПРОИЗВОДСТВЕННАЯ СИСТЕМА СИБУР. Псс сибур
производственная система дойдет до каждого
СИБУР: производственная система дойдет до каждого
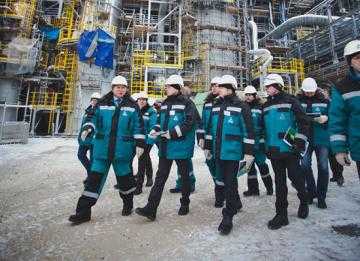
Василий Номоконов, руководитель службы технологии и обеспечения производства СИБУР
В компании началась активная фаза реализации проекта по внедрению производственной системы СИБУРа (ПСС).
Как повысить эффективность производства, затратив при этом минимум средств? Ответ на этот вопрос ищут менеджеры любой компании. Вариантов много, но все они сводятся к одному: необходимо менять организацию труда и поведение работников. Нужно, чтобы время и другие ресурсы расходовались максимально эффективно, а каждый человек на своем рабочем месте понимал, что помочь компании улучшить производственные и финансовые показатели – в конечном счете, в его собственных интересах.
В мире накоплен большой опыт организационных изменений. Но сегодня производственная концепция компании «Тойота», получившая название «бережливого производства», по праву признана одной из наиболее эффективных. Ведущие мировые производители, в том числе в нефтехимической отрасли, активно осваивают элементы бережливого производства, достигая значительных результатов в снижении затрат и повышении скорости реагирования на постоянно меняющиеся требования рынка. Основа философии бережливого производства – постепенное устранение из рабочего процесса так называемых «потерь» – всего, что требует времени, ресурсов или места, но не добавляет продукту ценности в глазах клиента. Именно на этой философии будет строиться производственная система СИБУРа.
Если кратко, ПСС – это система принципов, стандартов и регламентов, позволяющая максимально эффективно использовать ресурсы, способствуя при этом росту качества продукции и стимулируя людей добиваться постоянных улучшений в работе.
ПСС состоит из четырех основных блоков: технического, блока развития способностей персонала (обучение передовым практикам), блока мышления и поведения (того, что мы называем корпоративной культурой) и процесса управления.
Уже сейчас компания занимается развитием отдельных элементов системы и применяет многие из перечисленных инструментов, например, в проектах развития системы управления качеством, системы управления эффективностью. Одна из целей ПСС – объединение этих «кусочков паззла» в единую систему.
Что именно изменится в производстве, а главное, в жизни сотрудников?
На рабочих местах по определенной пятиступенчатой методике (системе 5S) будет наводиться и поддерживаться порядок. Из производства будет удалено все лишнее, ненужное. На рабочих местах будут находиться только необходимые материалы и инструменты, причем располагаться они должны на удобных стендах и стеллажах, спроектированных с участием самих рабочих. Будут ведены стандарты порядка (в т.ч. визуальные – в виде фотографий на стенах). Обязательными станут регулярные аудиты рабочих мест на соответствие стандартам порядка, а бригадам и сменам будут выставляться оценки. В результате рабочие места станут удобными и безопасными, инструмент, материалы и детали не придется искать по всем закоулкам, теряя на это рабочее время. Единственное, к чему надо будет привыкнуть – возвращать все на свое место и поддерживать порядок постоянно.
В производствах вводится принцип визуализации результата. Это не только таблички с обозначениями, знаки безопасности, обозначение цветовой маркировкой всех проходов, проездов, ограждений, маркировка технологической тары, обозначение периметров мест хранения и мест парковки техники. Важное нововведение – в производствах, в операторных появятся стенды, на которые будут вынесены основные производственные и технологические показатели. Каждый сотрудник будет видеть все параметры, на которые влияет он сам, его бригада или смена, установленные верхние и нижние границы для каждого параметра, динамику показателей. Должно войти в привычку проводить передачу смен около такого стенда: всем видно, как отработала предыдущая смена, «хорошие» и «плохие» смены.
Для всех уровней управления будет реализован принцип стандартизированной работы. Этот принцип означает, что каждая операция – как технологическая, так и управленческая – должна иметь определенный стандарт выполнения. Стандарты должны быть для всех: операторов, технологов, ремонтников и даже менеджеров. Необходимо уйти от ситуации, при которой каждый оператор или механик выполняет одну и ту же технологическую или ремонтную операцию своим собственным способом, в зависимости от своего опыта, навыков и даже личных качеств. Эту задачу и призваны решить стандарты, разработанные при непосредственном участии наиболее опытных и квалифицированных сотрудников.
У каждого производственного подразделения появится набор своих КПЭ. Их будет немного, рассчитываться они будут с учетом меняющихся условий работы. Такими показателями могут быть, например, расход сырья или пара.
Все внутренние подразделения завода будут функционировать по принципу «клиент-поставщик». Очевидно, что каждое подразделение завода одновременно является поставщиком и клиентом по отношению к другим подразделениям. Соответственно, будут созданы внутренние договора по аналогии с обычными коммерческими контрактами, которые будут содержать критерии взаимной оценки подразделений. Подразделения будут выставлять оценки друг другу, и оценки будут размещены на стендах в производствах. По итогам месяца на совместной встрече представителей клиента и поставщика будет происходить обсуждение взаимных оценок, будут выявляться проблемы и пути их решения. Взаимные оценки подразделений должны быть увязаны с системой КПЭ и будут напрямую влиять на мотивацию сотрудников.
Ресурсы в производство будут поставляться по системе «точно в срок». Ни один ресурс не будет поставляться в производство без предварительного заказа с рабочих мест. Роль заказа будет выполнять карточка заказа («канбан»), а сроки и объем поставки будут строго соответствовать указанным в карточке. Поставка будет осуществляться непосредственно к рабочим местам.
Работники будут обучены методикам бережливого производства, методам поиска и устранения потерь и будут принимать активное участие в выработке предложений по повышению эффективности производства, в так называемой системе непрерывного совершенствования. Каждый сотрудник сможет оформить собственную идею в простейшей форме, ни одна из поданных идей не окажется не рассмотренной, а получившие одобрение будут быстро воплощены в жизнь.
Каждый сотрудник будет встроен в свою функциональную вертикаль (например, вертикаль механиков или энергетиков), проходя внутри этой структуры тренинги для повышения квалификации, как профессиональные, так и управленческие. Уровень, которого работник достиг в развитии своих функций, будет регулярно оцениваться.
Дальнейшее развитие получат центры компетенций. Это даст возможность получать «скорую техническую помощь» и обмениваться передовыми практиками в масштабах предприятия и компании.
И, наконец, с каждым сотрудником будет проведена беседа для выявления «болевых точек» его предприятия. По результатам собеседований появятся планы устранения слабых мест.
Как будет проходить реализация проекта?
Внедрение системы начнется с разбивки предприятия на участки. При этом мы должны понять дистанцию, которая отделяет каждый участок от лучших практик, и определить для себя, сколько средств теряется из-за неэффективной работы на том или ином участке производственной цепочки.
В организационную структуру проекта входит команда дизайна, команда внедрения и команда проектов-ускорителей. Команда дизайна состоит из 9 человек – это лидеры и эксперты по различным направлениям.
Заниматься внедрением будут специально выделенные сотрудники компании – корпоративная команда внедрения. На каждом предприятии организуется еще и своя команда внедрения – передовой отряд из 30 человек. Корпоративная команда внедрит систему на первых нескольких участках, остальное будет делать команда внедрения предприятия. После этого корпоративная команда переедет на другое предприятие, периодически проверяя, как продвигается уже запущенный процесс. Центры компетенций также станут активными участниками перемен. Они будут отвечать за техническую сторону, разрабатывать стандарты.
Вместе с сотрудниками СИБУРа над проектом будут работать консультанты из компании «Дюпон».
Проект рассчитан приблизительно на 5 лет. За три года мы запустим процесс на всех предприятиях, еще два года потребуется на полное внедрение ПСС.
«СИБУР сегодня», корпоративный журнал, январь 2011г. www.sibur.ru
Источник
beleader.com.ua
«Скажи, не молчи» или «Производственная система СИБУРа – это диалог»
Производственная система СИБУРа – это диалог, который с первых же дней ведется между всеми, кто вовлекается в процесс внедрения. Эффективность подхода оценили на первом этапе проекта, завершенном на «Томскнефтехиме».
С точки зрения развития любое предприятие можно улучшать в трех направлениях: повышение надежности производства, совершенствование технологий и организационной эффективности. При этом все изменения на предприятиях должны быть приведены к единым стандартам компании.
«Производственная система СИБУРа нацелена на воспроизведение стандарта повышения эффективности,– подчеркнул на прошедшей в Тобольске «Полимерной неделе» генеральный директор «Томскнефтехима» Игорь Климов. – Это имеет отношение и к развитию корпоративной культуры. На уровне топ-менеджмента СИБУРа, руководителей предприятий изменения уже хорошо заметны: исповедуются единые подходы к эффективности. На уровне производственных участков ситуация иная – люди, как правило, применяют очень разрозненные подходы. ПСС изменит корпоративную культуру предприятия на всех его уровнях. То, что мы видим на двух пилотных участках «Томскнефтехима», где идет внедрение системы, оправдывает наши надежды».
… производственная система СИБУРа нацелена на воспроизведение стандарта повышения эффективности …
С февраля 2011 года на томской площадке работала команда из 90 человек: сотрудники «Томскнефтехима» и других предприятий СИБУРа, консультанты «Дюпон». Одиннадцать стартовых недель отвели на диагностику предприятия. «Необходимо было определить дистанцию, которая отделяла тот или иной участок работы от лучших мировых практик, и понять, сколько средств теряется из-за неэффективной работы на отрезках производственной цепочки», – пояснил руководитель корпоративного проекта «Внедрение производственной системы» Рустам Галиахметов.
Полигонами внедрения стали установка полимеризации этилена, цех ремонта технологического оборудования и химической защиты и один из складов. Это позволяло охватить несколько непохожих звеньев производственной цепочки. «Мы поставили перед собой две основные задачи: во-первых, внедрить культуру высокой производительности, во-вторых – создать механизмы и функции, которые будут поддерживать преобразования уже без участия проектной команды», – объяснил руководитель проекта по внедрению ПСС на «Томскнефтехиме» Александр Сметанин.
Центром изменений должен был стать человек – работник предприятия. Первый же соцопрос показал, что далеко не все понимают, как этот принцип может быть реализован. При этом выяснилось, что люди думают над недостатками, с которыми сталкиваются в производственном процессе, но плохо представляют себе, как воплотить появляющиеся идеи. Начали с вовлечения всего персонала пилотного участка в процесс разработки ключевых показателей эффективности. Важно было показать, что они формируются не директивно «сверху», а на коллективных собраниях, где люди сами предлагают показатели. Участвуя в их разработке, работник может оценить собственное влияние на бизнес-процессы. Еще один инструмент, который несет в себе ген «ментальной трансформации», – стандартные операционные процедуры (СОП). Это просто небольшой плакат с иллюстрациями и лаконичным текстом, отражающий суть операции и лучшую практику ее выполнения. «Стандартная операционная процедура» составляется с участием всех людей, выполняющих эту операцию.
… центром изменений должен был стать человек – работник предприятия …
Василий Номоконов, управляющий директор СИБУРа:
ПСС состоит из нескольких частей. Каждая из них позволяет более системно управлять предприятиями и получать экономический эффект.
Во-первых, глубокая диагностика, не только техническая и экономическая, но и морально психологическая. При этом 10–20% сотрудников предприятия проходят подробное интервью и могут говорить о чем угодно. Главное – составить объективную картину того, что происходит на предприятии, чем оно живет, что мешает работать над повышением эффективности производства.
Во-вторых, проверка технических возможностей по всему предприятию, поиск организационных улучшений. Например, изменение процесса планирования ремонтов, упрощение и упорядочивание технической документации, прозрачна я и упорядоченная система отчетности между подразделениями предприятия, разработка графиков приема руководителей.
В-третьих, стандартизированное улучшение основных процессов на участках. Мы берем участок за участком, преобразуя за полугодие каждый из них. Внедряются инструменты бережливого производства, проходит системное обучение всех работников этих участков методам бережливого производства, разрабатываются и внедряются ключевые параметры эффективности.
Каждый инструмент проходил многократную обкатку на практике. Например, доски передачи смен, на которые выносятся основные производственные и технологические показатели, менялись около 20 раз: добавляли одни элементы, убирали другие, меня ли месторасположение стенда в зале. В результате получили инструмент, который действительно помогает в работе: основные параметры отражены, описаны проблемы, возникшие в предыдущую смену, начальнику следующей смены стало легче расставить приоритеты и обозначить задачи на следующие 12 часов. На оборотной стороне записываются предложения и вопросы работников, запросы на дополнительное обучение.
По словам Рустама Галиахметова, слабая вовлеченность персонала – главный источник потерь. В этом плане еще одним удачным инструментом оказалась система «Улучшения малыми шагами», опирающаяся на инициативы работников. На участках размещены стенды с большими прозрачными карманами – идея, изложенная на бланке, проходит понятный путь от подачи предложения до его одобрения или отклонения экспертным советом.
… слабая вовлеченность персонала – главный источник потерь …
«Люди включились в процесс: предлагается пополнить оборудование или изготовить элементы и приспособления, улучшающие работу», – рассказывает начальник смены пилотной установки ремонтного производства Кирилл Лашкевич. К середине сентября на ремонтном производстве было подано 106 предложений. Из них 48 принято, 16 уже реализовано.
Одновременно внедряется система 5С – инструмент оптимальной организации рабочего места. «На пилотных участках обучение системе проходило по 2–3 раза, производственники сами на этом настаивали, – говорит Александр Сметанин. – Сложность состояла в том, что люди воспринимали 5С как простое наведение порядка, тогда как к этой системе стоит относиться скорее как к инструменту, который позволяет снижать потери времени, материалов, энергоресурсов». 5С на «Томскнефтехиме» в итоге подхватили даже те участки, которые не являются пилотными, куда с ПСС формально еще не заходили. Так, работники участка по ремонту технологического оборудования на РП привнесли изменения в обустройство рабочей зоны.
«Что сделали? Вот стенд для ключей, теперь каждый ключ – на своем месте, – поясняет бригадир участка Владимир Алексеев, подводя к аккуратной стойке с инструментами. – Раньше они все хранились в общем ящике навалом, а порой «застревали» на рабочих местах ремонтников. В практике 5С говорится: если человек тратит на поиски нужной ему вещи более 15 минут и не находит, то просто бросает это дело. У нас, конечно, никто на выполнение задачи не махал рукой, но тратить на поиск столько времени неразумно».
… если человек тратит на поиски нужной ему вещи более 15 минут и не находит, то просто бросает это дело …
Все предложенные ПСС инструменты несут в себе потенциал содержательного диалога – между работниками и руководителями, внутри подразделения и с работниками смежных участков. А диалог рождает изменения. Но это не исключает более прямых высказываний, как в ходе проведения структурированных интервью. На них работники говорят о плюсах и минусах работы на предприятии. На старте внедрения ПСС в Томске состоялось около 200 таких бесед. А затем на встречах, названных «зеркальными сессиями», работников знакомили с перечнем проблем, выявленных экспертами ПСС и мешающих предприятию работать в полную силу. В «зеркальных сессиях» приняли участие 2,5 тысячи сотрудников «Томскнефтехима».
«Удалось создать хорошую инфраструктуру для работы проектной команды, заинтересовать руководство пилотных подразделений, получить обратную связь в виде конструктивных предложений от работников, – подчеркнул Игорь Климов. – Вместе с тем, для полноценного диалога нужен план внедрения изменений и понимание, к чему должно привести каждое из них. А значит, обязательны также закрепленные результаты».
С 2012 года стартует второй этап внедрения производственной системы на «Томскнефтехиме». Команда внедрения, сформированная из томичей, будет работать на всех установках производства полипропилена, двух ключевых установках производства мономеров и продолжит работу на производстве полиэтилена, ремонтном производстве и в службе управления запасами.
… диалог рождает изменения …
Павел Рабунец
Руководитель и главный редактор Leaninfo.ru. В Институте комплексных стратегических исследований отвечает за развитие издательского направления - книги по бережливому производству. Преподает "бережливое производство" в Томском политехническом университете.Поделиться с друзьями:
Подписывайтесь на Leaninfo.ru в соцсетях: Facebook или ВКонтакте.Или следите за новостями бережливого производства по email.
Смотрите также:
www.leaninfo.ru
КЛИП » СИБУР И ПРОИЗВОДСТВЕННАЯ СИСТЕМА СИБУР
Открытая лекция Михаила Гордина,члена правления и управляющего директора ООО «Сибур», выпускника МГТУ
10 февраля 2015 года, 17-30Москва, 2-я Бауманская, д.5, МГТУ им. Н.Э. Баумана, Главный корпус, аудитория 433Регистрация: http://clip-russia.ru/meetings/registration/ | Схема проходаС 8 февраля 2015 станция «Бауманская» закрывается на реконструкцию. Как добраться
Краткое содержание лекции:
- Активы, масштабные проекты и вертикально-интегрированная бизнес-модель крупнейшей в России нефтехимической компании СИБУР
- Почему компания СИБУР решила внедрить Производственную Систему – систему, ориентирующуюся на изменение корпоративной культуры, на изменение сознания и поведения каждого человека, позволяющую творчески и эффективно использовать все возможные ресурсы/потенциал предприятия и устранять все имеющиеся потери
- Основные инструменты ПСС
- Ключевые результаты внедрения ПСС
Гордин Михаил Валерьевич
Член правления – управляющий директор СИБУР
Родился 16 августа 1969 г. в Москве. В 1993 г. закончил кафедру ИУ-5 МГТУ им. Баумана по специальности «Автоматизированные системы обработки информации и управление». С 1990 г. работал научным сотрудником в Институте системного анализа РАН. В период с 1997 по 2005 г. занимал различные должности в компании ConocoPhillips, сначала в Москве, а с 1999 г. — в европейской штаб-квартире компании в Лондоне.
В 2005 г. вернулся в Россию и был назначен директором департамента проектов переработки попутного газа ОАО «ТНК-ВР Менеджмент».
В 2008 г. приглашен на работу в СИБУР заместителем руководителя дирекции синтетических каучуков по развитию. Параллельно с 2009 г. возглавлял корпоративный проект по модернизации в СИБУРе функции управления цепочками поставок. В декабре 2011 г. назначен управляющим директором компании, руководителем Дирекции синтетических каучуков. Член правления ООО «СИБУР» — управляющей организации ПАО «СИБУР Холдинг».
СИБУР — крупнейший нефтехимический холдинг России. ПАО «СИБУР Холдинг» является газоперерабатывающей и нефтехимической компанией с уникальной бизнес-моделью, ориентированной на интегрированную работу двух основных сегментов — топливно-сырьевого и нефтехимического.
Похожие лекции
Информационные партнеры
Похожее
clip-russia.ru